Piston pumps and inflatable seals create a system that protects employees and products.
Graco, Inc.
07/24/2017
Imagine scooping and scraping a 55-gallon drum of tomato paste by hand. Imagine doing this five, 10 or even 20 times per day. Surprisingly, this is how many food producers unload ingredients from containers. Not only does this seem inefficient and labor-intensive, but with arms scooping into drums about three feet deep, this method is taxing to the human body and not ideal from a sanitation perspective. Even more surprising is that hand scooping is used for many high viscosity ingredients that are thick, sticky, and will not pour or fill back in when scooped. Some examples are peanut butter, tomato paste, icing, caramel and fruit filling.
.jpg)
Manual Scooping
Manual scooping was once the only option available to food manufacturers. It is becoming less common for four main reasons: labor costs, ergonomics, sanitation and waste. Scooping is the most labor intensive of the four options and is not usually feasible from an economic standpoint in areas where labor is more costly, such as the United States, Canada and Europe. It is more prevalent in areas where labor is less expensive, such as South America, Asia and Mexico. In the latter areas, manual scooping can be the least costly option when compared to purchasing equipment. One drawback for manual unloading is the effect it has on employees. Ergonomics can be an issue, and it is not uncommon for employees to become injured from performing this task repeatedly. Compensation claims can quickly negate any cost savings realized by not investing in other equipment. In addition, manual unloading exposes the ingredients to the atmosphere and allows employees to introduce contaminants into the food product. A person who has been scooping tomato paste all day would understandably be dirty and sweaty and can easily introduce bacteria and contaminants into the food products. Lastly, manual scooping can leave material waste in the drum.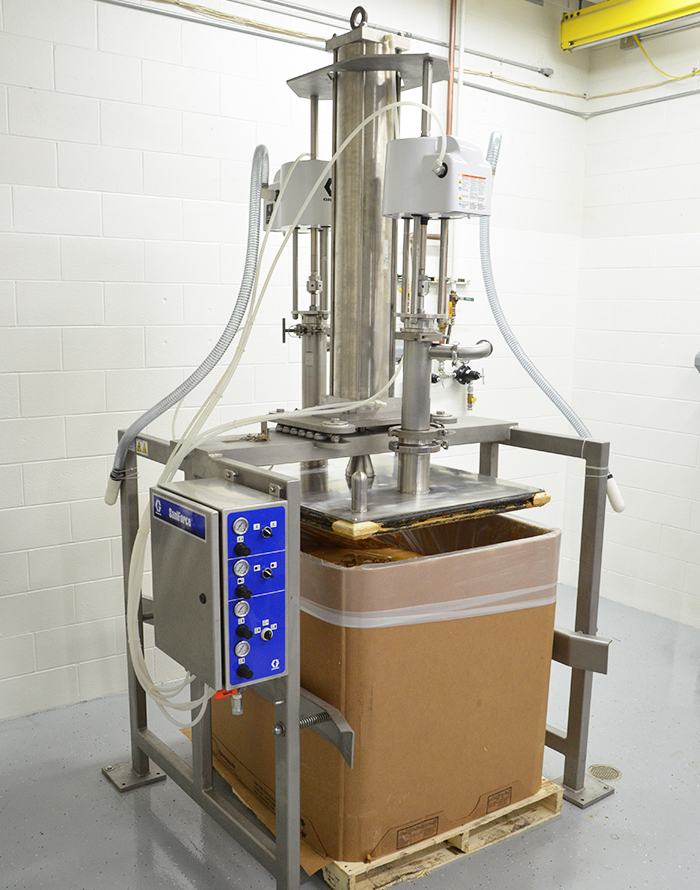