The Valley Forge Sewer Authority system has pumped clog-free and mostly maintenance-free for 14 years.
KSB
09/25/2017
Fourteen years ago, the pumps operating at the septage receiving wet well at the Valley Forge Sewer Authority’s (VSFA’s) collection system in Phoenixville, Pennsylvania, were constantly clogging. This created frequent headaches for the operators and cost valuable time and expense for unscheduled maintenance. Unscheduled downtime created delays in unloading for the septage trucks and interrupted the normal plant operations as trucks were unable to off-load upon arrival.
.jpg)
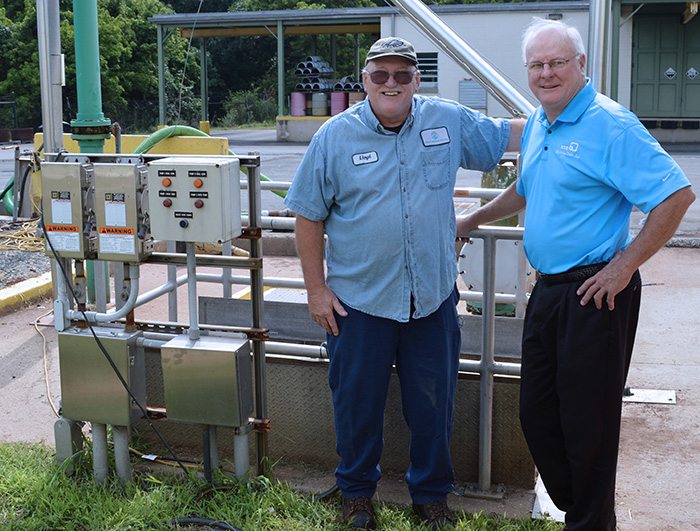
Background of the Site
The VFSA is a utility that is owned by its customers and was incorporated as an operating authority in 1968. VFSA owns and operates 90 miles of sewer pipeline, nine pump stations and a regional treatment plant rated for 10 million gallons per day (gpd), and treats an average of 8 million gpd. VFSA serves approximately 22,000 customers in nine Chester County municipalities: the townships of Charlestown, East Pikeland, Schuylkill, Easttown, East Whiteland, Tredyffrin, Willistown, West Vincent and Malvern Borough. In addition to treating the influent wastewater into clean water for stream discharge, the plant also produces a specialized fertilizer product used by area farmers.The Problem
Part of the plant includes a dedicated septage receiving wet well. The septage waste is then pumped to an equalization tank, prior to being flow-paced into the treatment plant process. Knauer said that before the pumping system upgrade in 2002, the wells were overflowing regularly because the truck operators did not realize that the pumps were not transferring the materials that were causing the clogs. “We would either find out from the operators after an overflow occurred, or from the high-level sensors that we eventually had to install,” Knauer said. “Whenever the overflows would happen, two mechanics would have to come over and get down inside the dry well, shut off all the valves, pull the pump apart, pull the impeller out, unclog it, and put it back together. In the septic business, downtime means lost money. During emergency shutdown of the pumps, the dumping process was curtailed until the pumps could be returned to service, with the result that septage trucks would be waiting as long as several hours until the pumps were back in service.”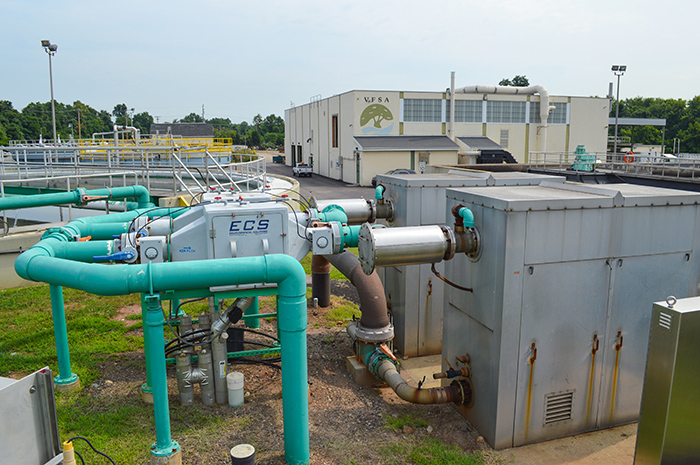
A Cycle of Changes in Wastewater
A 23-year veteran of the VFSA, Knauer has seen his share of changes in wastewater pumping, particularly with the use of flushable wipes, and other fibrous materials that can knit and cause pump clogging. “Fortunately, these non-clog pumps can handle it,” Knauer said. Over the past 10 to 15 years, the low-flow water toilet has reduced the volumetric flow. There has been an increase in the use of personal wipes, in addition to traditional fabric and fibrous materials. The overall impact has been increased clogging issues in a lot of places. Additionally, there has also been a steady demise of large industrial and general manufacturing plants with high water effluent volumes, which has greatly increased the percent of solids in the pumpage, given the reduction in dilution water from those large industrial users. Often, “rag balls” form inside the collection system pipes. This is caused by small fibrous materials that re-knit to create much larger formations. In this geographic area, there are many homes with on-site septic tanks. When the septic tanks reach a certain level, they must be pumped out. That fluid is difficult for standard sewage pumps to deal with. It has an unusually high percentage of abrasive solids (sand) when compared to sanitary waste streams in wastewater collection systems..jpg)