Two steps forward, one step back. That is what it feels like to run an operation with a leaky pump, which inevitably leads to unscheduled downtime and increased maintenance needs. This stalls productivity and can cost companies hundreds of thousands of dollars per hour of downtime. When hazardous chemicals are involved, the situation is even more serious. Aggressive acids and slurries can cause pumps to leak much faster, and they create an unsafe work environment. Air-operated double diaphragm (AODD) chemical pumps offer many benefits to manufacturers that require the use of hazardous materials. Most other pump designs rely on mechanical seals for chemical containment, but mechanical seals are known for being prone to chemical erosion and leaking. AODD chemical pump designs eliminate the need for mechanical seals by using bolts to secure the pump together and create an effective seal. The AODD pump’s diaphragms move in gentle cycles to minimize turbulence and protect the liquid from shearing. In many instances, these chemicals can be as fragile as they are hazardous, and any mild turbulence could alter their chemical properties, wasting the material and costing money. Because AODD pumps are powered by compressed air rather than electric motors, they can run dry and deadhead without the risk of burning, seizing or harming their components. The problem with AODD chemical pumps is that their designs can vary in quality and effectiveness. The crucial factors of the AODD chemical pump selection process are chemical containment capabilities, corrosion resistance and icing prevention.
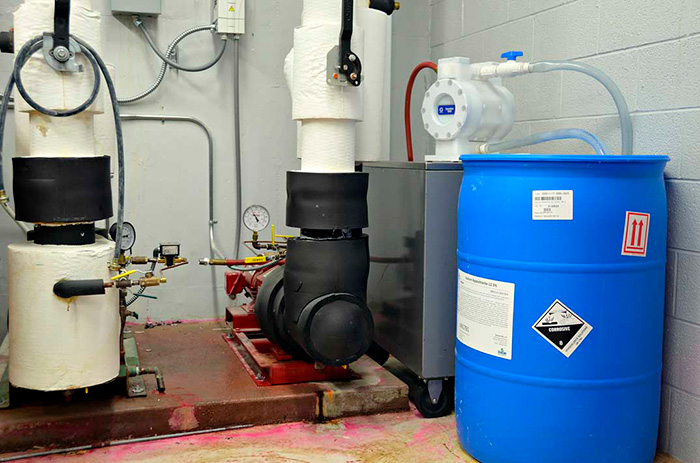