End users must be aware of the valve emission standards to meet industry requirements.
04/16/2014
An article in the October 2013 issue of Pumps & Systems discussed how to minimize leaks by applying proper design and material-selection standards. This article details new codes that have been established because the International Organization for Standardization (ISO) is currently updating certain standards, including ISO 15848 Parts 1 and 2. American Petroleum Institute (API) 624 was updated in February 2014. A summary of the standards and their test methods are shown in Table 1.
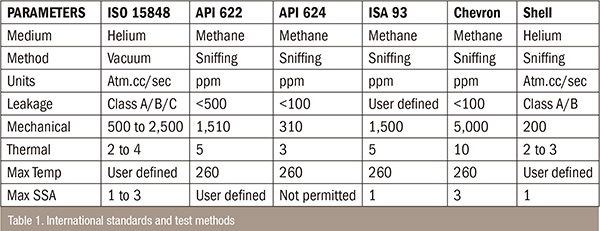
- Leaks greater than 10,000 parts per million (ppm) are being eliminated.
- Leakage to 500 ppm maximum is being limited.
- New API 624 (released February 2014) has moved toward allowable leakages of 100 ppm or lower.
- Awareness of environmental initiatives in North America has grown tremendously, and such initiatives have given visibility to projects such as the Keystone XL Pipeline.
- Hydraulic fracturing is being examined more closely and codes and regulations in this space have been updated.
- Policy makers are becoming strict and inspectors are imposing fines when necessary.
- Maximum stem to seal tolerance allowance (finishing)
- Criteria on leakage rates
- Maximum temperatures
- Minimum temperatures
- Leakage class
- Cycles
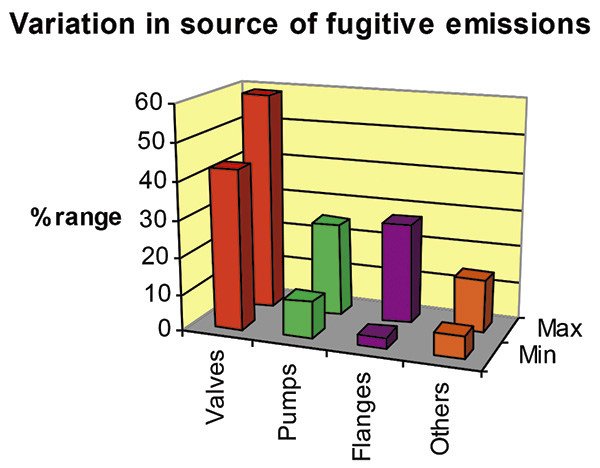
- The total cost of the valve
- Maintenance, shutdown and reliability costs
- The manpower required
- Meeting corporate safety and regulations
- Their industry image to be green and a clean producer