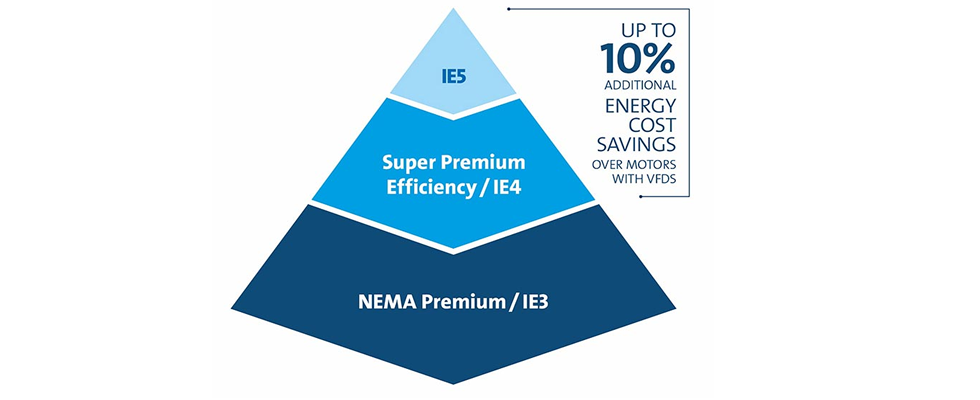
Before talking about pumps, take a look at another piece of equipment used to maintain comfort in a building: chillers. A chiller consists of a compressor, condenser, evaporator, expansion valve, power and controls unit, and many other ancillary items. When chillers were first introduced to the market, they were supplied as separate components, bringing many challenges during installation and commissioning. This is why manufacturers started manufacturing chillers as complete packages. Why should pump systems be any different? Pumping systems are comprised of pumps, motors, isolation valves, check valves, a power and control unit, and other ancillary items such as gauges and sensors. One could argue that pumps should be supplied as packages for the same reasons as chillers and boilers.
HVAC Design Requirements & Pumping Guidelines
The principal role of the pumping system is simple: provide enough flow so the building can be adequately heated or cooled. The pumping capacity, namely flow and head, is determined based on the building’s peak demand requirements. Since the building will rarely reach these peak design requirements—or if it does, it is only for a short period—the pumping system should be optimized for part-load conditions. Today, the most common approach to ensure good pumping efficiency at part load is the use of variable frequency drives (VFDs). The increased use of variable speed is also being driven by the building construction codes, which now include energy. The American Society of Heating and Air-Conditioning Engineers (ASHRAE) has included hydronic variable flow pumps in the Energy Standard for Buildings (ANSI/ASHRAE/IES 90.1, section 6.5.4.2). This section of the code requires pumps to have controls that will result in pump motor demand of no more than 30 percent of design wattage at 50 percent of design water flow.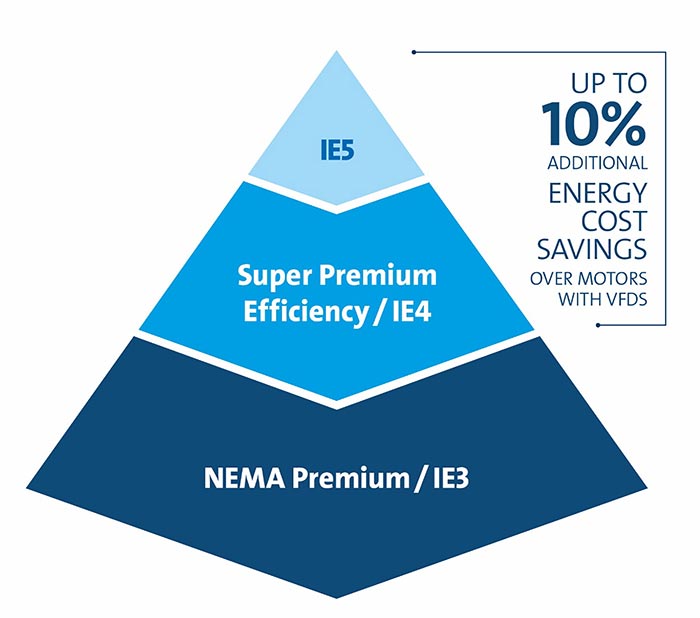
HVAC Pumping Design Practices
A common approach is to select one pump to handle the total flow and specify a second pump as a backup, resulting in what is considered “100 percent redundancy.” With the use of VFDs, this has been an acceptable approach and, in most cases, can meet the building energy code requirements. When looking at actual building cooling or heating requirements, this can result in pumps operating at below 20 percent of the rated capacity, and even with variable speed drive (VSD) control this can result in less than optimum pumping efficiency. Engineers should look at actual cooling and heating water demands over time when selecting which pump configuration to go with. This can result in multiple smaller pumps being more efficient than larger counterparts. Software can help determine building loads, which can help calculate flow rate data for each hour of the day for a full year. This information can be summarized to help select the optimal number of pumps. Table 1 shows the chilled water flow demand for a variable flow system.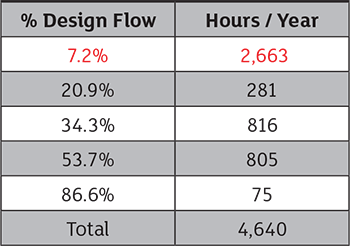
Field-Built Multipump Systems
Specifying pumps is more than addressing hydraulic considerations. Specifications must include motors, drives, controls, valves and any other equipment necessary for the successful installation and operation of the pump system. Engineers and building operators need the assurance that the pumps, motors and drives will work in harmony for many years. What sets the stage for this is proper installation—which requires planning—and that starts in the design phase. See Table 2 on page 67 for design phase considerations.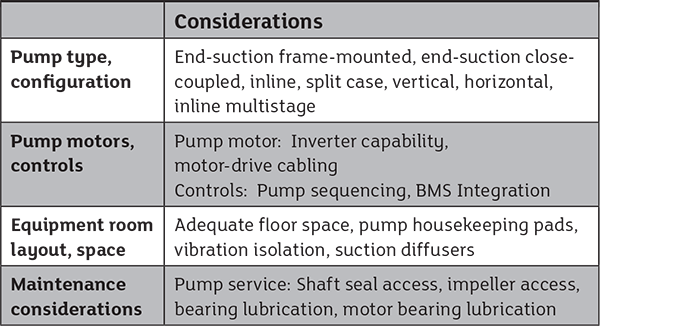