The benefits of variable speed pumping were recognized decades before the invention and successful commercialization of variable frequency drives (VFD). Despite superior reliability and low cost, AC induction motors are limited to certain specific speeds, which are a function of the applied power frequency and internal windings of the motor. This limitation has been problematic for pump specifiers and users ever since centrifugal pumps were first used. One early idea for variable speed pumping that remains relevant today is the eddy current drive. Alternately known as magnetic drives, or electromagnetic drives, these cleverly simple machines use the mechanical energy of a suitably rated constant speed motor and adjustable-strength magnetic flux to regulate the torque (and thus, speed) available to the driven load. Image 1 illustrates this process. The motor drives a cylindrical drum (light blue) at constant rated speed. A magnetically active rotor (red) rotates on a separate shaft and drives the pump at variable speed. The magnetic rotor is equipped with a low voltage coil that is energized by DC excitation current from the controller. Variation of the excitation current results in a proportional variation in torque, enabling the system to control speed to within 0.5 percent of demand.
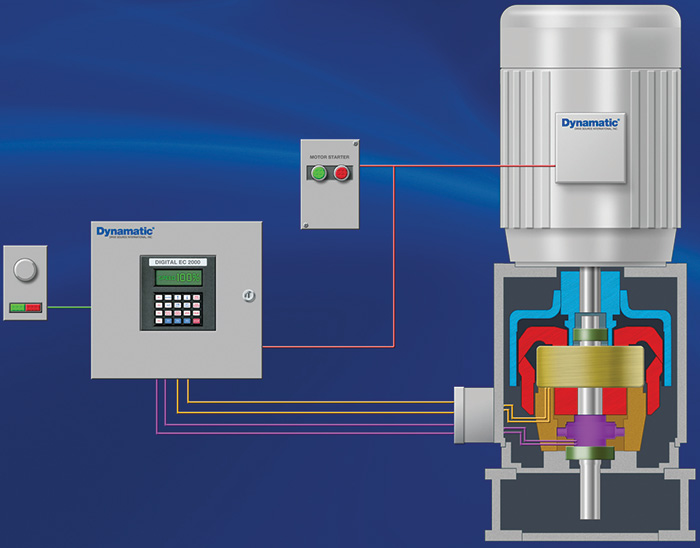
Controls Are Vulnerable
Older mechanical units are almost always repairable using widely available standard parts, such as ball bearings, carbon brushes, slip rings and speed feedback tachometers. Despite their long life of service, some controllers are vulnerable to failure and parts obsolescence. For a relatively low cost, the entire controller can be replaced. Modern adaptations of the controller can utilize the rugged and reliable silicon controlled rectifier (SCR) conversion technology to produce variable DC excitation from a single-phase AC input. This old-school technology is mated to a 21st-century digital-microprocessor-based control platform, giving this device a modern feel and far more flexibility than any preceding design. This makes possible a series of new features for the eddy current drive, like compact size, keypad monitoring and a single control platform..jpg)