NASA Tech Briefs describes proportional integral derivative (PID) controllers as "the modern industrial workhorse" because of their distinct role in automating the regulation tasks of today's advanced process control systems. PID controllers are well-suited for many speed, temperature, flow and pressure processes. In industrial and commercial settings where these elements are sometimes matched with processes that are nonlinear, that exhibit high inertia or that require multiple complex calculations, PID control can add significant value, automating many operations that would otherwise need to be performed manually. Yet, for many hydronics and heating, ventilating and air-conditioning (HVAC) applications that use induction motors to power pumps and fans, the torque needed to drive the motor loads varies based on the shaft speed of the motor, which can be controlled by a variable frequency drive (VFD). Leveraging advanced VFD algorithms for PID-controlled applications in industrial and commercial building settings is a unique approach that can improve the longevity of electric motors and reduce energy consumption for systems.
Tuning into Control Modes
PID controllers regulate output through the sum of their proportional, integral and derivative actions. Most control loops require proportional and integral methods, while motion control responds best to derivative methods. Temperature regulation often requires a mix of all three. The following descriptions highlight the differences between each type of control. Proportional control simply matches output action to error proportionally. In integral control, the controller reduces errors through incremental or decremental outputs that gradually improve or refine the overall process. The speed with which this occurs can be fast or slow depending on whether the error is large or small, respectively. But the integral timing must be precise to avoid problems in the loop, such as sluggishness or instability.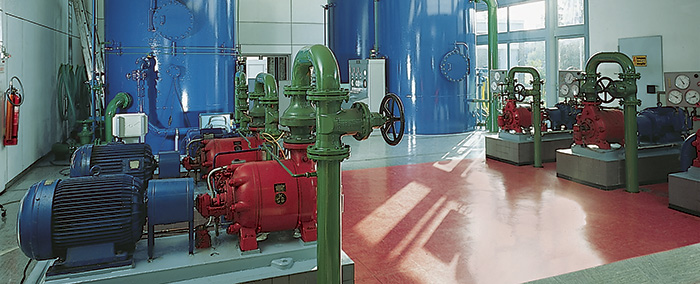