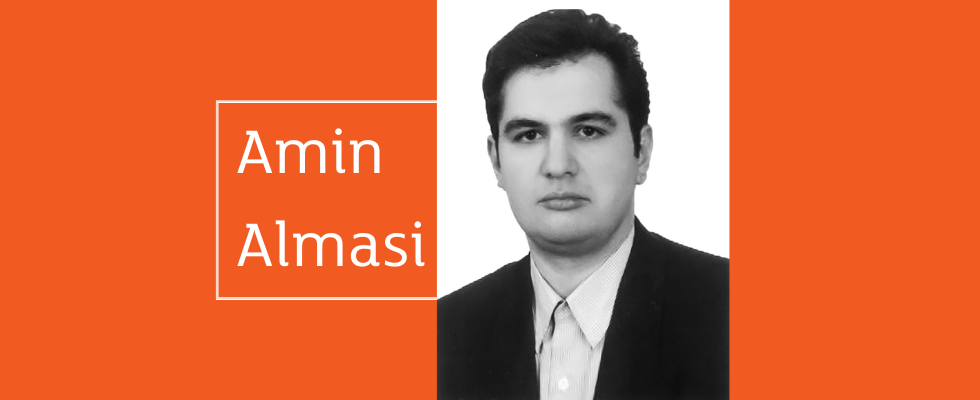
A rotating shaft (or rotor) can generate vibration and propagate it to the pump and subsequently to surrounding equipment, piping and facilities. The amplitude of vibration usually varies with the speed of the rotor/shaft. At critical speeds, the amplitude of the vibration becomes large, and the shaft experiences a resonant vibration. Unbalance and misalignment are important causes of vibration in pumps. However, there have been other sources and forms of vibration related to pumps.
Vibration—and particularly the vibration due to unbalance and misalignment—have been the focus of attention for operation, performance, reliability and safety of many pumps. A key point is a systematic approach to the vibration, balancing, alignment and monitoring (vibration monitoring). Most of the investigations on pump vibration, balancing, alignment and vibrational condition monitoring have been theoretical.
Special attention should be paid to practical aspects and simplified methods and rules for the operational applications (for operators, plant engineers and experts). This article discusses vibration in pumps and the complexity and subtlety of issues that may be encountered.
Vibration in Pumps
Pumps have been widely used in modern plants and facilities. Through the years, there has been a tendency to use faster, higher power and better performing pumps with lower vibration levels. However, to fulfill these challenging goals, it is necessary to better specify, operate and maintain the pumps. This would translate to better designing, modeling, simulating, analyzing, manufacturing and maintenance.
Excessive vibration can be an indication of a developing problem or impending failure. The vibration and associated shaking/noises have been regarded as sources of operational difficulties, reliability issues, failures, discomfort and safety concerns.
Vibration Components
The fundamental properties of the vibration of rotors are usually discussed based on traditional and simplified
explicit formulations. In this way, the vibration of the rotor can theoretically be divided into two major parts: free vibration and forced vibration.
Vibration has two major components, namely a forward vibration and a backward vibration. In the forward component, the rotor follows a spiral path around the bearing axis in the direction of shaft rotation. Conversely, in backward vibration, the rotor center moves in a spiral path around the bearing axis in the direction opposite to the shaft rotation. If the pump is manufactured and operated well, the free vibration will usually decay rapidly, thus making the forced vibration the principal concern.
There have been different challenges and difficulties in vibration analysis, vibration monitoring and their interpretations. Too often, with increasing vibration frequencies, correlation between calculated/analytical vibrations and experimental/actual readings becomes increasingly difficult because of the complex mode shapes.
Practical Pumps & Resonances
For many categories of pumps, such as those with variable-speed capabilities, it is not practical to design and build a pump which is clear by reasonable margins from resonances between all possible periodic disturbances (excitations) and all possible natural modes of vibration.
Resonance situations are often unavoidable, as in the case for variable-speed electric motor drivers (VSDs) or variable-speed steam turbines, gas turbines and engines. In practice, the pump train should be dimensioned accordingly to cope with the resonances. Some resonance cases are not practically risky due to reasons like high damping involved in the mode.
For others, a proper mitigation method should be formulated. One mitigation method is achieved by reducing the excitation loads acting on the vibrational mode(s). For instance, the excitation forces due to unbalance and component weight variations can be minimized by proper balancing. These excitation forces can normally be reduced by 70% to 80% from the original/ordinary level.
For a real excitation in pumps (actual resonance), the direction of the excitation should match the natural mode shape in a way that the natural mode can be excited by that excitation loading (or action). Most often, it is possible to live with the resonance if the excitation direction does not match the natural mode shape. For instance, a bending excitation cannot usually excite at a natural frequency of torsion. In rare cases, there might be a coupled torsional-lateral resonance case. The possibility of such a special case or rare circumstance should be properly evaluated.
The worst possible resonance situation is congruity of the natural mode shape and the excitation mode shape at the same frequency. Under certain conditions, some compliances would be enough for an excitation to excite a mode shape.
Also, there could be complicated coupled cases where a specific excitation would excite an unlikely mode through a coupled vibrational mechanism. By comparing the excitation patterns and natural mode shapes, it is possible to form an impression of whether the excitation at a particular frequency or harmonic order is risky/dangerous for the pump or not. Actual experiences, accurate testing and operational reference checks are ways to evaluate how risky a theoretical resonance case is.
Misalignment
Misalignment is a major source of pump vibration. Limited accuracy in the alignment of shafts and couplings is usually a key challenge. There are typically small offsets of the rotor center lines (radial offset) and angular deviations of the connection, for instance, due to out-of-squareness coupling flanges. Therefore, there are always some vibrations due to misalignment.
When the coupling halves are forced together by bolting, the rotation of the shaft produces a rotating pair of forces caused by radial offset and a rotating pair of bending moments caused by the misalignment. For the misalignment, there are typically two events per each rotation of the shaft/rotor and the signature vibration excitation speed is two times the shaft speed.
For many pumps, the operating speed range and/or their harmonics interfere with the critical speeds (natural frequencies). Therefore, the aim is to avoid risky resonances, problems and failures. The associated risk assessments are based on proper simulations and operational experiences.