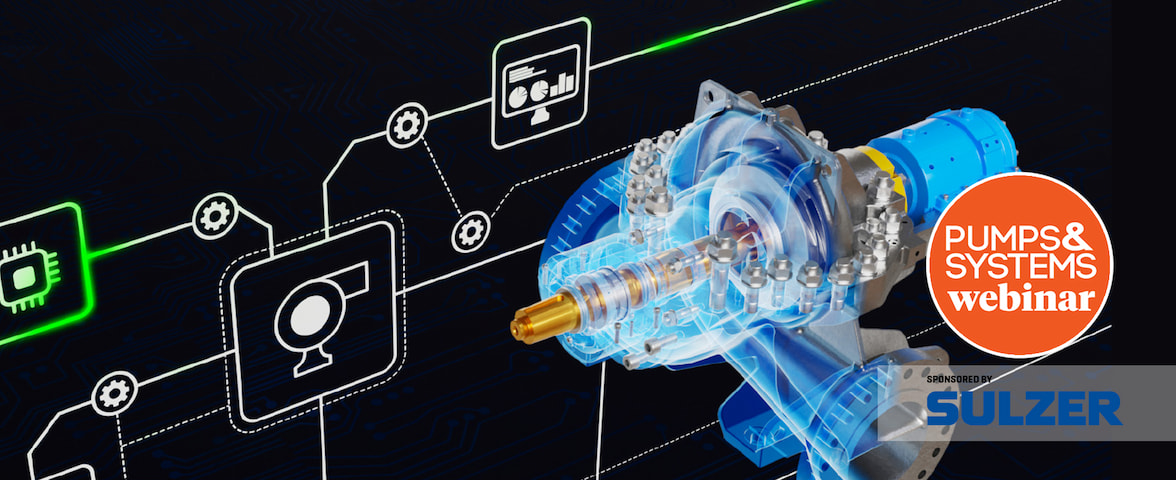
Date
Time
In the wake of ongoing concerns over security of supply, heightened supply chain and energy costs and increased pressure on businesses to improve sustainability, the demand for energy efficiency in industrial equipment and assets has been accelerated.
The call for pump operators to act now has never been greater, and the risk to operators who fail to do so has never been higher. However, the savings from improving pump efficiency are all too often overshadowed by those afforded by increasing heavy equipment efficiency such as turbines.
According to the Hydraulic Institute, energy is the largest single expense over a centrifugal pump’s life cycle cost, and there remains substantial opportunities to reduce energy costs and decarbonize. In our upcoming webinar, Sulzer’s retrofit experts will discuss and explore the following:
- Top five root-causes for energy losses in centrifugal pumps
- Holistic end-to-end energy efficiency solution possibilities comprising of audits, retrofits, machine learning based monitoring and more
- Proprietary calculator: identify and visualize pumps’ best efficiency point (BEP) gaps and energy savings potential in a matter of minutes
- Real-world energy efficiency case studies via targeted retrofit with tangible outcomes such as $200k of energy savings and more than 450 kilograms of carbon reduction
SPEAKERS
Retrofit Speciaist (Southeast Asia)
Sulzer
Solution Engineer
Sulzer
Sponsored by
