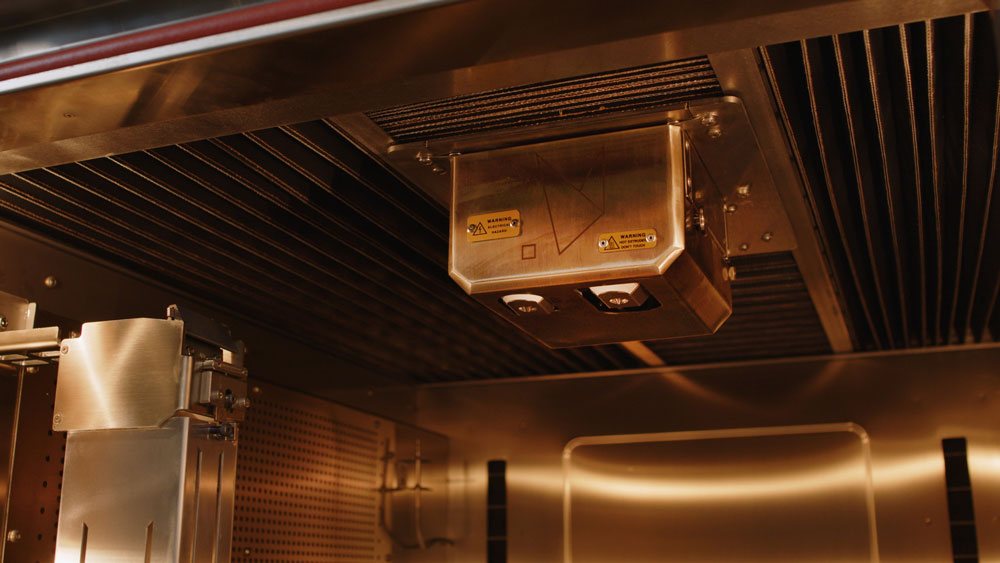
Our LinkedIn feeds are filled to the brim with bits and bobs of new this and new that. But who cares? What difference does it make? 3D printing can often seem like one of those bits. New trinkets are coming out constantly with the ever-advancing wave of modern iteration (now backed by the “all-seeing” AI). But can this technology bring value to industries that are actually keeping the world in motion? Does 3D printing belong in long-established regulated industries such as fluid motion, food and beverage, chemicals and even traditional oil and gas?
3D Printing in Industrial Applications
The answer comes not when considering the latest desktop bauble, but instead, the supply system as a whole. We live in a connected world—that is a given. Open trade is the mantra of our industrial age. But how is that going for us? Are the global chains of give and take operating with excellence and efficiency? Are suppliers providing their components and services quickly and reliably? Is it straightforward for an aftermarket pump repair company, for instance, to source spare impellers, wear rings, casings, etc.? The answer (especially after the pandemic that must not be named) is clear. There is a massive presence of inefficiency in the global supply chain, and 3D printing can—at least in theory—relieve some of this need.
But there is a second prong to this spear. If we are stuck with the generic desktop printers zipping out pumpkin-orange kitchen sponge holders in PLA (a beginner plastic), regulated industries will remain uninterested and uninfluenced. In other words, high performance materials are paramount to bringing value to the regulated sectors. Plastics that can stand up to use at temperatures above the boiling point of water would be a nice start. But printing polymers strong enough to rival (some grades of) aluminum that can provide exceptional tribological performance, endure temperatures up to 572 F (300 C), easily handle chemical challenges (such as hydrolysis, acids and bases, organic solvents, halogenated solvents, hydrocarbons, etc.) may open a wide range of applications for the world of fluid motion. And if those components can be manufactured on-demand and near the point of use, the impact becomes exponential.
Example: Impellers in the aftermarket
To provide an example, take the following not-so-hypothetical case. Aftermarket repair Company A has a large operator in the Middle East who needs a custom impeller for a plant. It is an important pump for the plant’s operation and is handling treated water contaminated with sulfuric acid. Company A will consider a handful of options. Having the impeller cast would be very expensive. For impellers with approximately a 15-inch diameter, a good mold alone would start around $8,000 (understand, that is just the mold) and could have the plant waiting 20 weeks or more for manufacturing. The second option? Machining a similarly sized impeller from a solid block of metal or engineering polymer would require design work, computer-aided manufacturing (CAM) programming, material procurement, machining time, heat-treatment, coatings and more. The bill, depending on material choice, would be at least as much. For this impeller, Company A was quoted for over 36 weeks turnaround time from the impeller OEM. This trend becomes exaggerated with larger diameter impellers. The third option follows—the localized production of spare parts and replacement components with additive manufacturing (AM) in high-temperature, high-strength composite materials.
Material Considerations in 3D Printing
Industrial printing machines can now repeatably print materials like polyether ether ketone (PEEK); polyether ketone ketone (PEKK), a close cousin; and carbon fiber reinforced PEEK. The formal term is fused filament fabrication (FFF). Fused deposition modeling (FDM) is also widely accepted. For those not familiar with the technology (I suppose there are some who still live in caves), a heated nozzle mounted on a 3-axis conveyance system is fed plastic filament, melts the filament and deposits it onto a build platform layer-by-layer until a final shape is formed. The conveyance system is programmed by a “slicing” software that breaks CAD files up into thousands of layers and calculates the most efficient paths for the nozzle to take within each of those layers. And as the print job progresses, polymer is deposited molten onto either the build platform or the previous layer and solidifies into a fully dense functional polymer component ready to hold kitchen sponges throughout the nation and world.
PEEK, PEKK and carbon fiber reinforced PEEK
Where this process becomes difficult is with the aforementioned materials such as PEEK, PEKK, carbon fiber reinforced PEEK and some polyetherimide (PEI)-based materials such as ULTEM 9085. The very reason these materials are selected for demanding engineering functions is because they do not melt at high temperatures. PEKK is the highest performer in this group with a 200-hour lifetime at 572 F (300 C) and a 20,000-hour continuous service temperature at 500 F (260 C). To remedy this challenge, the best-in-class industrial 3D printers are constructed with a heated chamber—within which the nozzle-conveyance system operates—that can keep the material at its glass transition temperature as it is laid down. So, it is extruded just above its melting temperature (Tm) into a chamber heated just above its glass transition temperature (Tg).
Without going too deep into polymer rheology, this practice allows large components to be manufactured in advanced polymers with consistent material properties along their entire height and without ripping themselves apart as they are constructed. (As a bonus insight, the industry is now moving toward fused granulate fabrication (FGF) technology which uses injection molding pellets as the feedstock instead of filament and takes advantage of larger nozzle sizes, faster deposition rates and reduced feedstock costs.)
3D Printing & Standards Compliance
An industrial 3D printer’s capability to perform automatic quality monitoring to comply with industry specifications is also crucial in the industrial application of this technology. While the pump, industrial and energy sectors have been notoriously slow moving with regards to their standards and uptake of new technology, there have been recent movements toward adoption. Specifications such as the American Petroleum Institute (API) 20T outlines best practices for the qualification of the manufacturing process to ensure optimal and repeatable quality of additively manufactured polymer-based components.
The specification integrates with International Standards Organization (ISO) 9001 or API Q1 and provides a framework for first article manufacturing and ongoing production according to three levels of component criticality (AMSL 1, 2 and 3). As this trend—albeit a slow one—continues in the industry, a printer’s capability to capture real-time data of all essential variables of the printing process will be essential to remain relevant ensure final component quality, and comply with these new standards.
To conclude with the case study, carbon PEEK was chosen for a few reasons. Its ultimate strength in the direction of the extrusion path is 125 megapascals (MPa), it does not creep, and it would be comfortable at 90C. The material has excellent corrosion resistance and would handle the 1% sulfuric acid (H2SO4) and slightly abrasive working fluid with no problem. Polymer impellers, when balanced and installed correctly, can also operate quieter and with less start up energy draw due to their reduced weight as compared to their metal counterparts (stainless steel, Duplex-family alloys, bronze, etc.). The impeller was manufactured, balanced and installed in March of 2021 and is still in use today. The long-term adoption of this technology within the regulated sectors is still ongoing. However, in the current market the global need is certainly not waning, and given the technological maturation of applications, the additive manufacturing of advanced polymers may be a solution to make the globe run just a bit smoother and increase the bottom line of players both large and small.
For more on 3D printing, visit pumpsandsystems.com/tags/3d-printing.