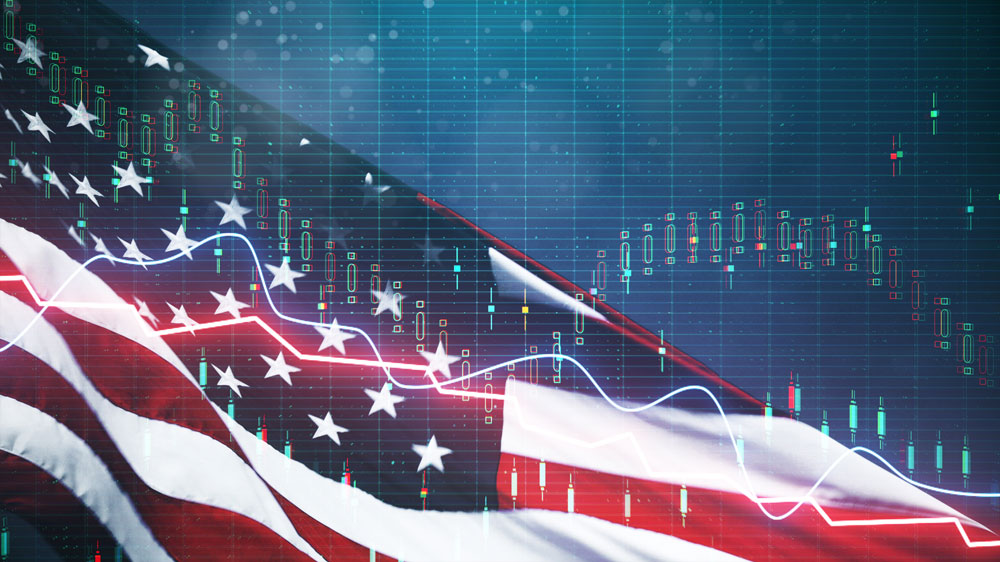
Impellers and casings. You can’t make a pump without them, right?
Hopefully, pump manufacturers won’t have to face that challenge as the requirements become stricter for Made in America components for projects funded with federal dollars.
In July, the Biden administration announced it would take the domestic content threshold from 55% to 60%, with a phased increase to 75% by 2029. Thus, the value of the U.S. component parts used in any federally funded project must be at 60% today. Then the Build America, Buy America section of the Infrastructure Investment and Jobs Act introduced strong language on forced localization, including eliminating the American iron and steel exemptions for pumps under Environmental Protection Agency/U.S. Department of Agriculture (EPA/USDA) revolving funds.
The issue is, as Michael Michaud, executive director of the Hydraulic Institute, explained recently, the vast majority of clean water centrifugal pumps are made with casings and impellers that are forged overseas. Even if the pumps themselves and additional components are engineered or manufactured in America, pump manufacturers are reliant on international supply chains.
Long ago, North American-based pump manufacturers had to offshore items like casings and impellers due to costs, access to raw materials, and because the work is not environmentally friendly so it was more difficult to do in the U.S., Michaud said.
“Biden’s Executive Order raised the requirement for U.S. components and is being integrated into new legislation that focuses on federal spending,” Michaud said.
In the past, projects funded with federal dollars—including federally financed water or wastewater projects—allowed exemptions or waivers. Water and wastewater project exemptions were created in the 2009 American Iron and Steel Act, which applies to projects funded by the EPA. If a project receives even a small fraction of federal funding through the State Revolving Fund (SRF) or other federal financing mechanisms, the content restrictions can apply to the whole project.
Now, however, those waivers are being tightened under the Biden administration’s new directive, spending bills and coordinated under the newly formed Made in America office.
“The reality is that we live in a global economy, so we need to strike a balance with this strict Buy American language and what we need to do to invest in improving our critical infrastructure,” said Hydraulic Institute Vice President of Governmental Affairs Mark Chaffee.
Chaffee recently met with the U.S. Secretary of Commerce Gina Raimondo and Celeste Drake, the director of the Made in America office.
“The current component test for Buy American is strictly the percentage of foreign material based on price. There’s no consideration for value added by the American workers,” said Chaffee, who is also vice president of governmental affairs and C&I product management for Taco Comfort Solutions. “From Taco’s standpoint, we’re determined to protect and grow the over 500 manufacturing jobs we have in the U.S. However, to keep those jobs we have no choice but to source globally. We believe there should be some consideration to the value added by the American worker, and there’s not. That’s probably the biggest ask—for a change in the way the component test is calculated. We believe it benefits us all.”
The recently approved $1.2 trillion infrastructure investment will drive billions of dollars to fund water and wastewater projects, Michaud said. However, if pumps, which are made in America but with some components from overseas, are not allowed due to the new restrictions, it will limit the number of projects or cause significant delays in the project completion. There are lots of wrench-ready projects that include installing more energy-efficient pumps. Delaying or excluding those projects would also hurt the administration’s climate change agenda, Michaud added.
The timing factor is critical, as the 60% threshold went into effect immediately and the administration is trying to get the infrastructure money out quickly.
“Long gone is the idea of a vertical, U.S.-only based supply chain,” Michaud said. “Most casings and impellers come in from overseas—they are globally sourced and completely integrated into the pumping system once they arrive here in the U.S.”
The Hydraulic Institute is pursuing a strategy to educate policymakers on the need for a global supply chain and the value of maintaining the current waivers and exemptions that are in place.
“We’re not anti-Buy American,” Michaud said. “We are American manufacturers with complex global supply chains.”