Pumping Prescriptions
Pumping Machinery
10/03/2016
When a pump experiences internal wear, its performance drops. Flow is reduced and efficiency plummets. But what happens to power? Does it drop, stay the same or increase? The answer to this question depends on how a pump wears internally. In extreme cases, when the impeller is completely worn, there will be no flow and hardly any power. But in many cases, tight clearance parts, such as wear rings and bushings, are the first to wear.
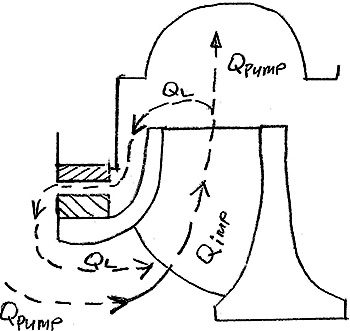
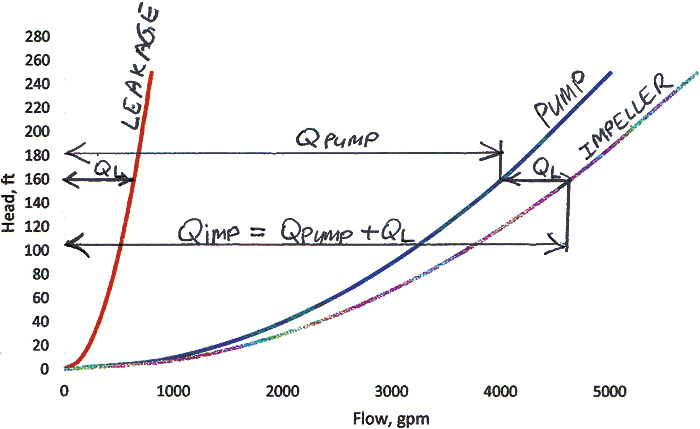
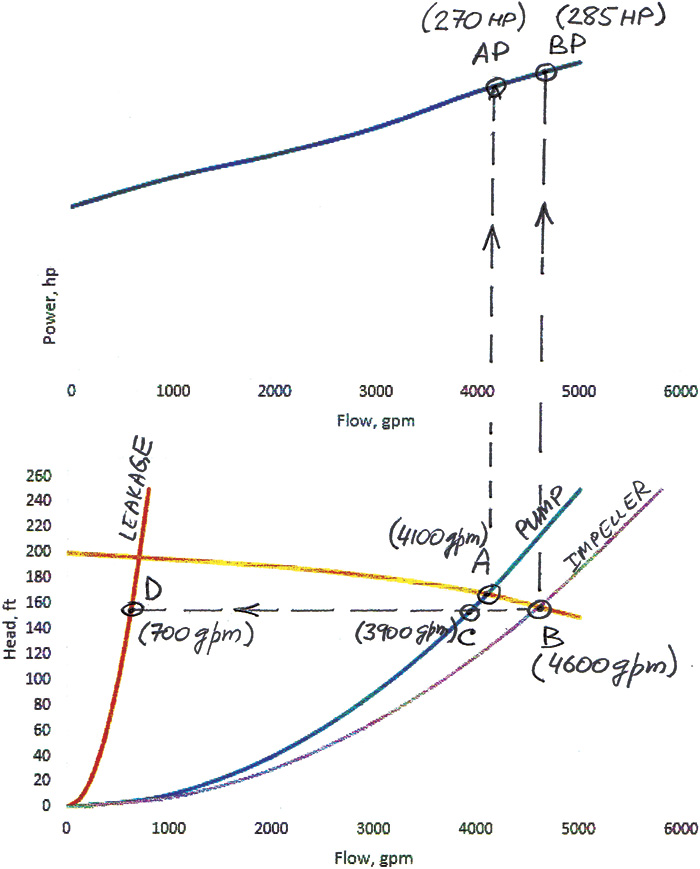
- System flow dropped.
- Pump power increased.
- Pump efficiency decreased.
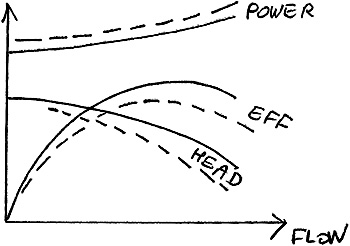
See other Pumping Prescriptions articles here.