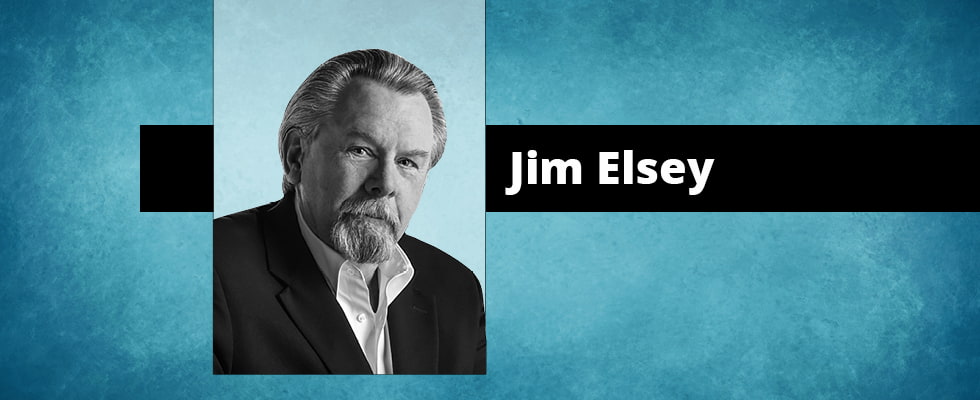
I’ve been around for a while and have observed the parade of fashions and trends coming and going through the years. From my college days in the ’60s—miniskirts, peace signs, corduroy pants, tie-dye and paisley shirts were “groovy” and “far out.”
Now 50-plus years later, many of these faded ideas have made a resurgence, at least in some circles. Perhaps some of these fashions and trends were good ideas and some were not. In retrospect, I have few regrets of my own personal choices from the past, but I do wish I had held on to my car, a muscle car that I street raced.
Thinking back to my car from the ’60s, I typically evaluated my odds of winning or losing the race by estimating the car’s horsepower to weight ratio as compared to my opponent. Going forward in the pump business the last 50 years, end users have also pushed industrial pump manufacturers toward a similar goal—exponential horsepower increases for more head and flow—all contained within smaller and smaller pump sizes or, simply, get more with less.
Suction Energy
I have been involved with industrial rotating equipment in one way or another since those days of wearing bell-bottom jeans, and sometime in the last half century, I was also exposed to the theory of suction energy (SE). SE is a concept that explains how the momentum of the fluid entering the pump suction can potentially be an issue or not. Similar to disco music, it appeared to be a good idea at the time. Thankfully it faded quickly and, like an odd wrench in the bottom of my toolbox, I did not use it anymore, but I could not throw it away either.
I dismissed the practicality of SE in a column many years ago; however, I am seriously rethinking the decision because I am now looking at it in a different way. Many readers may not have heard of this thing called suction energy. SE is, in essence, a measurement of the liquid momentum at the impeller eye. SE, in its simplest definition, is the unit-less mathematical product of the nominal inside diameter of the pump suction nozzle (D), multiplied by the pump speed (N), multiplied by the suction specific speed (Nss). Note: The speed is revolutions per minute (rpm) and the diameter is inches.
Formula 1:
Suction Energy = D x N x Nss
A more refined definition of SE exchanges the first factor of the pump suction nozzle size for impeller inlet (eye) size (De). Note: They are frequently close to the same dimension. Specific gravity (SG) was also added to the formula and, if pumping cold water it is obviously not a factor, but if pumping hot water or a different fluid, the factor should be weighed.
Formula 2:
SE = De x N x Nss x SG
If the impeller eye diameter is unknown and cannot be determined, you may estimate it by using the following factors: For an end suction pump, multiply the suction nozzle size by 0.9, and for a horizontal split case or radial inlet pump, multiply by 0.75.
Defining Levels of SE
The results of these equations produce high numbers, and so it is common to use a form of short-hand scientific notation, but the coefficient remains as a three-place number.
- Low SE is defined as values below the high SE levels.
- High SE is defined as values at or above 160 x 106 for end suction pumps and 120 x 106 for split case and radial inlet pumps.
- Very high SE is defined as values at or above 240 x 106 for end suction pumps and 180 x 106 for the split case and radial inlet pumps.
Pumps Have Boundaries
We are still not allowed to violate the laws of physics, and so this imposing goal of more with less requires improved impeller designs, higher rotating speeds and fluid velocities. Along with the benefits of more horsepower and head (generated per stage) all in a smaller box, there are caveats that require higher net positive suction head (NPSH) margins, diminished operating ranges and often more wear.
Technological advances have helped us design and manufacture better pumps since Lyndon Johnson and Richard Nixon were president, but some consequences will defiantly persist, simply to cruelly remind you of the serendipitous karma that pervades our universe.
And this brings me back to the subject of SE and the suction side portion of the pump system. Most pump manufacturers will ask for a minimum of 10 or more diameters of straight, unobstructed piping prior to the pump suction flange in a seemingly fair exchange for a trouble-free and reliable pump. This means no valves, no elbows, no tees, no strainers, no reducers and surely no flow meters. In the unfair light of the real world, the pump never gets to check off any of the boxes on this wish list of desired requirements.
Additionally, it is highly suggested that the liquid velocity in the pump suction inlet piping should be less than 10 feet per second (3 meters per second—slower is even better). This velocity requirement is also often cast aside.
To oversimplify what can be a complex design requirement at the entrance to the impeller, in a perfect world we are looking for an equalized hydraulic loading with zero pre-swirl, eddies and recirculation in the fluid as it is presented to the impeller around the entire 360-degree profile. When the SE level is low, the pump owner can often disregard many of these aforementioned requirements and still avoid the downside consequences that would normally result with these violations.
What I witness more and more with industrial applications are suction side issues that could have been avoided if the end user had paid more attention to the suction system from the dual aspects of energy (suction energy) and piping geometry.
What I frequently hear is that there is enough net positive suction head available (NPSHa) and the margins are adequate or the specific speed (Ns) and/or the Nss is in an acceptable range—so, what is the problem?
One of the remaining unaddressed issues is uneven hydraulic loading of the impeller with copious amounts of pre-swirl, recirculation and high velocities. One recent application I visited had more than six obstructions introduced in three different planes within the last 10 feet of suction piping. There was adequate NPSH margin, but the pump was in the very high range of SE and, consequently, the pump was not performing properly.
What I am ultimately trying to do is help the owner-operator have a reliable pump and operating system. I don’t know where all the boundary lines are exactly for your specific application.
Additionally, note these guidelines and guardrails are often grey areas—not black and white. There are also no flashing red warning signals for the inexperienced designer.
Another way to say all of this is: If you have adequate NPSH margins and properly selected impellers for the operating range, you still need to evaluate your total system design. The typical design will be a compromise based on best practice hydraulics on one side and the initial cost of the system on the other. What many organizations do not allow is an evaluation of pump/system reliability and the associated cost over some period of time, perhaps five to 10 years or even 20.
Look at the SE level of your system and if it is low, then perhaps you have nothing to worry about and can move on. However, if it is at a high or very high level, then I suggest that you re-examine your system design with a higher degree of due diligence regardless of the NPSH margin and the impeller geometry.
Prediction Clues
When you have pump and system issues and can’t seem to figure it out, look at the SE level and, in conjunction with that data, also consider these additional prediction factors/indicators of pump issues.
- liquid personality: temperature, viscosity and specific gravity
- impeller speed: watch for inlet tip speeds above 75 feet per second (above 100 for sure)
- pipe size suction: typically the size should be one size larger than the pump itself; in some high energy cases, you may want to design even bigger
- fluid velocity suction: looking for less than 10 feet per second at the suction
- pipe geometry (suction side): looking for elbows or components to be far
- from the pump suction nozzle, proposing 10 diameters
- impeller type: dual suction/shaft through the impeller or end suction
- impeller: number of vanes
- impeller vanes: the absence of—or the amount of vane overlap
- impeller: inlet incidence angle and also compare that angle to suction nozzle
- suction specific speed (Nss) and the D2 over D1 ratio
- specific speed (Ns)
- NPSH margin: even with an adequate margin, operating left of the best efficiency point (BEP) can be an issue when the SE is high
- operating point on the curve relative to the BEP
Additional Perspective
If you have a system that seems plagued with unexplained pump issues, take a look at the SE level. Professional engineer Alan Budris, who is a leading expert in the pump world and a champion of this concept, has successfully corrected system issues for clients when he persuaded end users to change to a different pump (or sometimes simply an impeller change) at a lower level of SE. This is not covered here, but there are additional tools that use the SE and NPSH margin ratios.
In a Pumps & Systems article from February 2012, Terry Henshaw, whom I respect deeply, questioned the concept of SE and suggested it was perhaps a flawed concept. Henshaw argued (and I am surely oversimplifying here) that when you algebraically compare the SE formula to NPSH, pump speed and Nss, many aspects (factors) are diminished or even eliminated. I agree with the argument as it was presented. I postulate that maybe there are ranges were SE is more important than in others?
However, my main point for this column is this: When making pump application decisions, the ultimate goal is to win. And just like on the race track from years ago, I want every competitive advantage I can garner.
References
- Allan R. Budris, 10th International Pump Symposium 1993 Proceedings
- Allan R. Budris, 15th International Pump Symposium 1998 Proceedings
- Terry L. Henshaw, “Is Suction Energy a Flawed Concept,” Pumps & Systems, February 2012
- Hydraulic Institute Standard ANSI/HI 9.6.1-2012 NPSH Margins
- Hydraulic Institute Standard ANSI/HI 9.6.6 Rotodynamic Pump Piping
- Allan Budris and Heinz Bloch, “Pump Users Handbook Life Extension”
Read more Common Pumping Mistakes articles here.