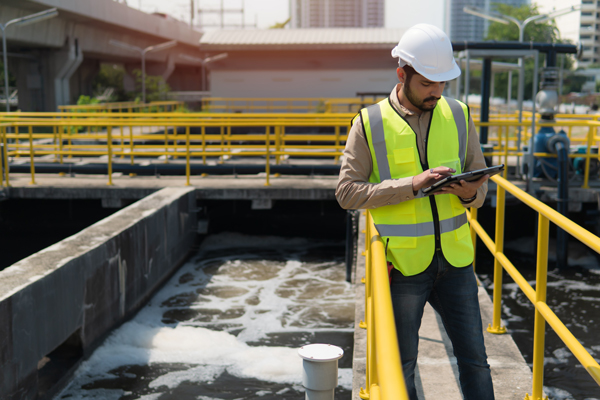
Lift stations are typically constructed by the lowest bidder. Often, drawings are not to scale, and the contractor must be an expert in assembling the parts and pieces that make up even the simplest station. In that case, the contractor must turn to the (low-bid) supplier of the pumping equipment and attempt to get as much system responsibility as possible included in a purchase order or purchase contract.
The constructor of a facility designed using the systems approach as the basic philosophy will avoid many of the pitfalls inherent in the often-convoluted, low-bid approach, but how far should the designer take this approach in creating lift or pumping station construction projects? The answer depends on several factors, such as the system complexity, the sophistication level of the contractors and the capability of the local manufacturer’s representatives.
The most complex systems may include several stations on a common manifold. For such systems, hydraulic analysis software is necessary to select the pumping equipment. In addition, because of the potential for improper operation, bidding restrictions to a few preselected manufacturers are justified. At minimum, the scope of supply should include pumps and guiderails, access frames and covers, motor controls and pump station control systems. The scope can be expanded to include access hatches over a valve vault (if included), variable frequency drives (VFDs), precast concrete wet well, valve vault and accessories. The goal is a quality project with no major issues during construction and successful operation with minimal call-backs. The proper application of a systems approach can help reach this goal.
The systems approach typically includes a combination of the pump, the motor and the controls. Pump efficiencies have not historically been standards based, but with the Department of Energy (DOE) definition of minimum pump efficiency, that has changed as pumps will need to be designed to meet guidelines. Motors also play a critical role, with premium efficiency motors gaining market presence. On the controls side, there are two solutions that contribute to the pump system’s efficiency. On one hand, for systems that have been oversized to meet anticipated future growth or have varying duty cycles, VFDs can provide the path to optimum performance. Controls can also provide monitoring functions to ensure pumps are operating at the optimal point. Time can reduce operating efficiency, for example, with impeller wear. Monitoring energy consumed provides feedback and allows the end user to better maintain optimal performance.
Why Is It Important?
Even a well-designed system can become inefficient or unreliable if operated incorrectly. The systems approach goes beyond design and construction to incorporate proper operation. Since operators may not be aware of the optimal way to operate the system or the component limitations, it is critical that operation be considered part of the system’s design and commissioning. Guidelines such as minimum and max speeds, flows, pressures and temperatures, as well as wet well elevation levels, cycle time, alternation and operation during emergencies must be documented.
Optimizing Bottom Line Performance
The goal of any pumping system is to move the liquid at the lowest cost and with the highest reliability. In wastewater, moving the liquid is simply a matter of getting it from point A to point B in an acceptable time. In many applications, the pumping system supplies liquid to a process and must be controlled to prevent over or under pumping. The systems approach requires that each component be evaluated for the particular purpose, with an eye toward creating an efficient, reliable system, at a reasonable cost. Examples include whether to use a VFD to control the pump speed, what type of pump and impeller design is most suitable for the application and proper selection of other components. As much as proper component selection will yield an efficient system, failure to consider every component can result in inefficiency, lack of reliability and system failure.
What Are Some of the Key Benefits?
The systems approach: determines the system responsibility unit and eliminates the question of cause of failure and isolates it under a single source; reduces the time element for repairs; promotes proper design and can establish a standard format for submittals and approvals; and optimizes pumping system performance.
There are two key benefits: energy savings and system optimization. VFDs can ensure that systems are operating at the best efficiency point (BEP), as well as help optimize applications where pumps operate with varying duty cycles. During the peak cycle, the VFD can ensure operation at optimal load, but during off-peak cycles, the VFD can adjust the pump to meet lower demand criteria. As many pumps represent variable torque loads, the energy savings are significant. A lesser known impact of the systems approach is that the controls can provide feedback on energy consumption. This allows for a preventative/predictive maintenance approach and aids in avoiding shutdowns.