The demand to balance innovation and environmental sustainability with reliability and cost efficiency is a challenge for managers across all industries. Yet when it comes to selecting sealing solutions, these priorities can be seriously undermined—and pump reliability routinely compromised—by simple force of habit. There have been significant advances in sealing technology in recent years that can reduce, and in some cases eliminate, the problems regularly faced by pump maintenance engineers, including leakage, shaft wear, bearings failure, and excessive energy and water use. These advanced designs have consistently demonstrated swift return on investment (ROI) and improved long-term reliability, while also helping companies comply with the International Organization for Standardization (ISO) -50001 standard for energy management systems and meet their own financial targets. Why do companies with an otherwise exemplary approach to operational, financial and environmental efficiencies persist in using outdated sealing solutions? The answer is as mundane as it is illogical. Some seals have been used for decades, and have been failing so regularly for so long that it seems to have become an accepted part of routine procedures by maintenance and repair personnel.
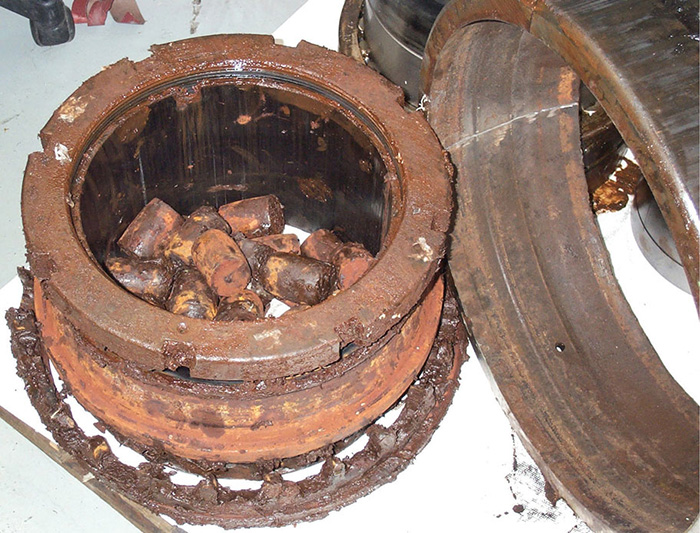
Bearing Protector Seals
Bearings failure accounts for about 40 percent of all pump and rotating equipment breakdowns, so it makes sense to tackle the root cause. Surface contact with the rotating shaft means some seals can start to deteriorate and wear almost as soon as they are installed, leading to ingress of liquids or particles, bearing corrosion and breakdown. The cost of regular downtime to replace lip seals can be exacerbated if contact with the shaft also causes the seal or the shaft sleeve to become worn, requiring replacement. The cyclical expense of replacing lip seals, and in some cases pump shafts, can be eradicated by upgrading to modern, labyrinth-style bearing protector seals. These comprise drive O-rings to grip the shaft and shut-off O-rings that land on a smoothly contoured surface, sealing the oil chamber when a machine is stopped, protecting it from liquid or particle ingress, but allowing the air in the oil chamber to expand outward during operation.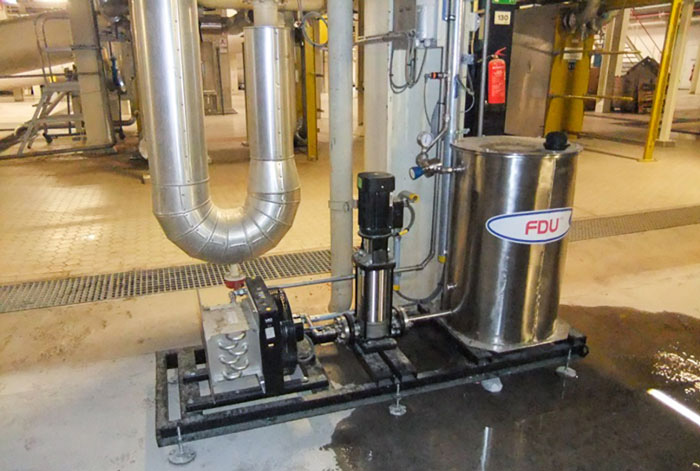
Cartridge Seals
Cartridge seals, originally the preserve of petroleum, natural gas and chemical industries, are increasingly replacing component seals as the sealing solution of choice across other industries due to the huge gains they offer in terms of reliability and cost efficiency. They offer advantages from installation through repair and refurbishment to inventory management. Cartridge seals arrive at a plant as a preassembled, pressure-tested unit that is locked to the shaft at the end of the pump assembly. This design eliminates the risks of damaging seal faces during transportation or build, which are inherent in traditional installations, as well as removing the need to measure and set spring compression. That is no small matter when considering the negative impact on durability that an incorrectly set working length of a seal can have.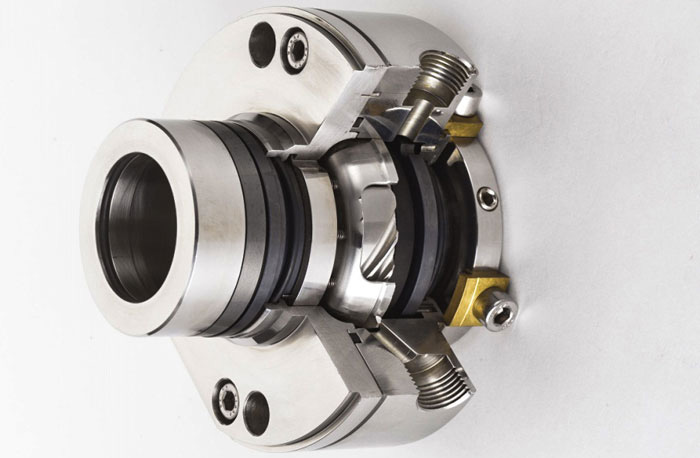