Bearings are precision components that require clean lubrication in adequate amounts to ensure a long, trouble-free life. Even small amounts of contamination or slightly elevated temperatures can lead to bearing failure. A study of equipment reliability conducted at a major refinery concluded that 40 percent of rotating equipment failures (pumps, mixers, etc.) were attributable to bearing failure. It further estimated that 48 percent of bearing failures were due to particle contamination and 4 percent were due to corrosion (caused by liquid in the oil). In fact, bearing oil contamination accounts for 52 percent of bearing problems and 21 percent of rotating equipment failures.1 If water, dust or other process fluids enter a bearing, it is headed for trouble. Modern labyrinth bearing protection seals can help prevent these issues.
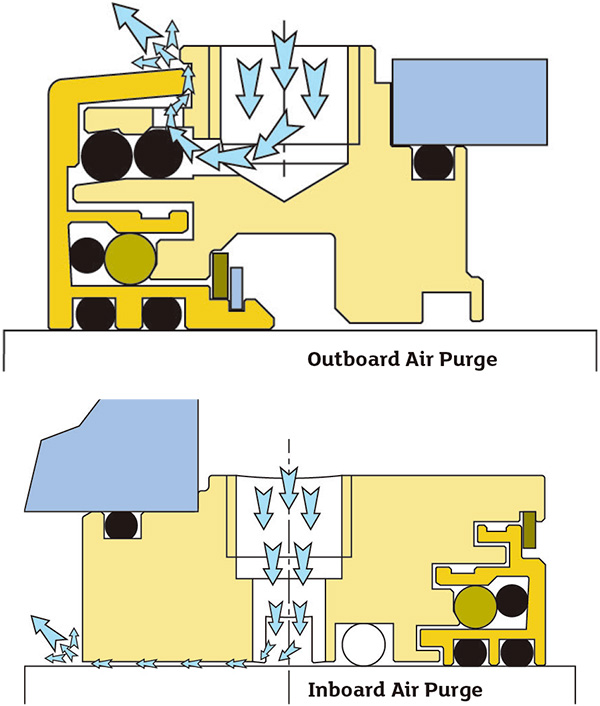
Dust Contamination
Dust in the production environment is a major problem for bearings. Heavy dust is made of particles as small as 50 microns that can become airborne. Because they fall at about 200 millimeters per second, these particles are unlikely to move beyond the production area. Heavy dust is readily seen as a cloud with the naked eye. Light dust, which is smaller than 50 microns in size, may stay in the air for more than 30 minutes. This type of dust can travel well beyond the manufacturing site, although it is commonly seen as a fine coating when it settles on machinery, bearing housings and other surfaces. Both types of dust are a concern because even light dust will find its way into a bearing. Although the housing offers some protection, ingress still happens. One significant factor in bearing oil contamination is the breathing process that occurs with all rotating equipment. When equipment rotates, the bearing housing heats up, and the oil and air mixture inside expands and is forced through the seal. The problem arises when equipment cools, because the oil and air mixture also cools and contracts, sucking air laden with dust from the external atmosphere through seals back into the housing. Over time, dust builds up inside the bearing and eventually leads to oil contamination, abrasion to components and bearing failure. Bearing seals must facilitate this breathing cycle to extend bearing life, while preventing dust contamination. Some modern labyrinth seals with an air purge design are suitable for use in extreme environments and applications where contamination may completely cover the seal or equipment (see Image 1). These use a positive air purge to enhance the performance of the labyrinth in combination with mechanical seal pressure balancing technology to maximize the performance of the seal and minimize air consumption.
Humidity & Moisture Contamination
Moisture can enter bearing housings through old-style labyrinth seals or lip seals as airborne water vapor or as a stream of water from hose-down operations. It can also enter through other ways, such as the breather vent or from the widely used non-pressure balanced constant level lubricators or abraded oil ring material.
Lubrication Issues
Improper lubrication accounts for about one-third of all bearing failures. Poor lubricant viscosity, prolonged service or infrequent changes, excessive temperature, using the wrong type of lubrication or over-lubrication are common problems. External contamination is another major cause of compromised performance of the lubricant. Creating optimum lubrication conditions is a balancing act between over-lubrication and under-lubrication. Both create a problem as do contamination or the use of a lubricant not suited to the equipment. Consistency, viscosity, oxidation resistance and anti-wear characteristics all play a role in the selection of a lubricant. Usually, the application will dictate the amount, type and frequency of lubrication needed.Extending Bearing Life
Manufacturers have developed more advanced labyrinth bearing protection seals that can offer protection against all types of contamination. For example, one seal that is non-contacting in operation to avoid shaft wear incorporates patented dynamic lift technology to protect against the breathing issues that contribute to 52 percent of all bearing failures centered around contamination. This dynamic lift technology uses the centrifugal force of rotating equipment to open a temporary micro-gap, allowing expansion of the oil and air mixture in the bearing housing, which allows the equipment to breathe. When the equipment stops rotating, the micro-gap immediately closes, forming a perfect seal. This prevents dust and moisture from being sucked back into the housing and therefore prevents contamination (see Figure 3).