Steady-state accuracy and repeatability help facilities improve performance and eliminate waste of expensive chemicals.
05/30/2016
Whether at a municipal water treatment facility, a petrochemical plant or an offshore platform, operations that use chemicals for processing, treatment and production enhancement seek to increase efficiency and save money. Meaningful savings can result from ensuring that the chemicals used are not wasted. A good way to deliver these efficiencies is to properly leverage the turndown capabilities of metering pumps. Turndown is expressed as a ratio of the metering pump output. If a pump is capable of a maximum of 1,000 gallons per hour (gph) and it has a 100-to-1 turndown ratio, then it can be adjusted to a flow rate as low as 10 gph and still perform within its accuracy rating.
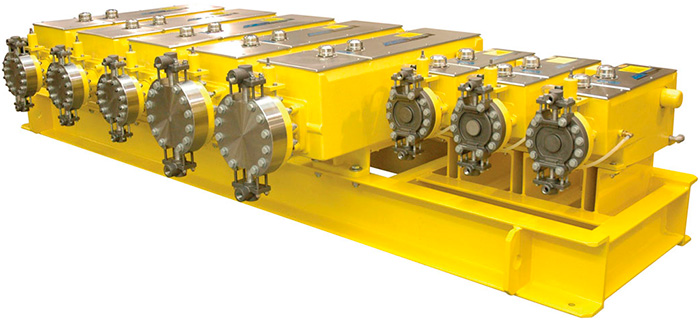
Turndown & Accuracy
Over the years, different metering pump manufacturers have promoted turndown capabilities of 1,000-, 3,000- or even 1 million-to-1. On the surface, these numbers may appear impressive, but what do they really represent? Turndown ratios do not offer much value unless they are tied to accuracy that can be measured. Without noting accuracy, a metering pump's turndown is essentially infinite—pumps can operate from maximum flow to no flow at all. Accuracy ratings can be misleading when they are expressed as a percentage of the pump's maximum rating. When this is the case, a pump with a maximum capacity of 1,000 gph can vary 1 percent of 1,000 gallons, or 10 gallons at any setting. As pump capacity is reduced, the actual resulting accuracy becomes less effective. What happens if this particular pump is required to operate at its minimum capacity of just 1 gph? A 1 percent variance (in this example) can still equal +/- 10 gph, which could result in a flow rate that is 10 times what is expected at the minimum setting. A better way to determine metering pump accuracy is to use deviation from the pump's current capacity setting, or set point. When accuracy ratings are expressed as a function of set point, turndown is defined by the pump's flow rate variation as a +/- percentage of mean delivered flow under fixed system conditions applied over the pump's full turndown ratio. This steady-state accuracy enables operators to dial in turndown ratios of 1,000-to-1. With steady-state accuracy, the same 1,000-gph pump operating at minimum capacity (1 percent) would deliver maximum variances of 1.01 gph and minimum variances of 0.99 gph. Flow repeatability is another form of accuracy. Also stated as a percentage of rated capacity, it describes how much the pump output is allowed to deviate when its capacity setting is changed and then returned to the original setting. If a pump provides 500 gph at 50 percent capacity and is temporarily changed to 80 gph, when the setting returns to 50 percent, the pump should accurately return to a flow of 500 gph, or be within a minimum range of +/- 3 percent flow repeatability.Why Is Turndown Necessary?
Metering pumps are specifically designed to dose precise volumes of chemicals. For operations with multiple processes running concurrently, or with multistage processes where different volumes of different chemicals need to be metered at different times, flow rate adjustments according to varying operator specifications and accurate dosing are critical. Numerous examples demonstrate why turndown is necessary for chemical treatment processes in different industries. For water treatment, municipal wastewater plants engage in various activities such as removing solid material like sludge and sedimentation, dissolving suspended organic material such as nitrogen and phosphorus, and disinfecting water by killing disease-causing microorganisms. The processes used to clean water vary based on the intended use of the final product. Drinking water requires more intensive cleaning than water reused for irrigation or industrial processes. Each process involves a series of steps: coagulation and flocculation, pH control, de-chlorination, chemical precipitation and oxidation, ion exchange, chemical neutralization and stabilization, and various measures for taste and odor control. Each step requires an assortment of chemicals used in different combinations until the desired water standard has been achieved. Turndown is important in water treatment because the volume and quality of the incoming water varies on a regular basis. Treatment plants located on rivers need flexibility to deal with storms that bring mud and sediment, while those on large lakes with relatively small variations in turbidity may only require minimal dosage changes. Seasons also prompt demand for turndown flexibility because seasonal changes in water quality affect chemicals that lose concentration in higher temperatures. Striking the proper balance of chemicals based on these factors is important. Overtreating water is wasteful and expensive and does not produce a better product. But undertreating in process steps, such as the disinfection of drinking water, could potentially harm people. Achieving this balance is best accomplished through metering pumps that offer a wide turndown ratio and repeatedly provide +/- 1.0 percent steady-state accuracy at any capacity setting. In petrochemical processing, accuracy, turndown and flow repeatability are non-negotiable items because of the toxicity of the chemicals and operational conditions. Hydrocarbons follow a dynamic continuum where pressure and temperature are varied through multiple processes. Dosing the precise amount of catalysts at exactly the right time is essential to produce the desired product. In this environment, accuracy goes beyond quality control; it directly affects the bottom line. Chemical plants run continuous operations, and processes must be correct the first time because repeating the setup is expensive and, in some cases, impossible. Errors in one part of the process can create ripple effects elsewhere that cost time and money. For all of these reasons, metering pumps must be designed to deliver +/- 1.0 percent steady-state accuracy with a minimum of 100-to-1 turndown ratios and capacity that can be adjusted by manual controls, variable speed drives, and electronic or pneumatic actuators.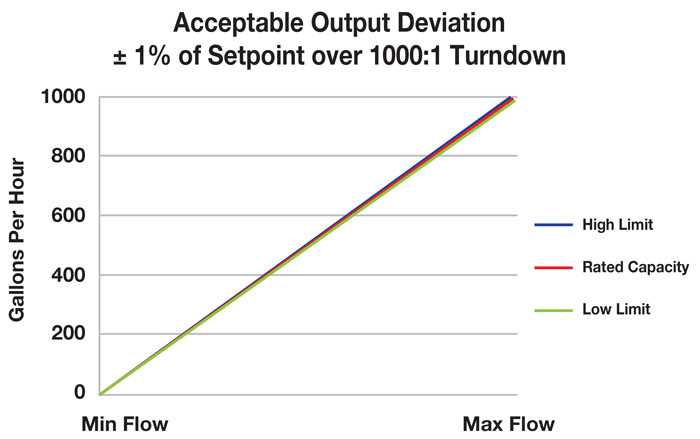