Modern real-time monitoring allowed this plant to drastically improve its reliability strategy.
KCF Technologies
11/16/2016
Motor-driven roots blowers are a critical part of everyday operations for one of the nation’s leading chemical companies, which creates chemical components for vehicle tires. Unexpected failures in the roots blower parts have cost the plant up to $80,000 in lost productivity for one specific incident. When a leaky seal on one of the plant’s 10 roots blowers was causing shutdowns, the reliability manager ramped up monitoring. The seal was expensive to fix, so he wanted to wait until the problem worsened to perform a total fix. The manager placed a bucket under the roots blower’s seal to monitor for complete seal breakage—the failure would be indicated if the bucket filled up quickly rather than a drop at a time.
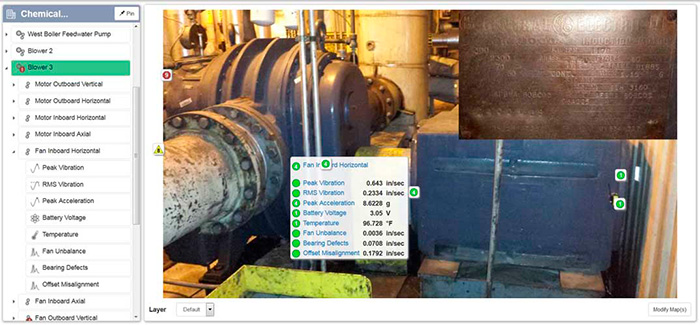
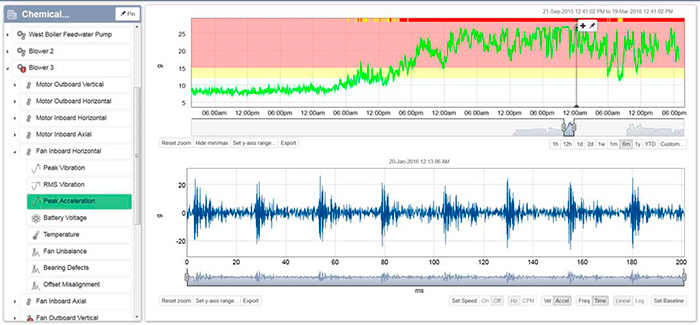
Questions to Ask When Installing Wireless Sensors
When considering installing wireless sensors on machinery, make sure to ask potential vendors these questions:
- What is your installation support process?
- Do you provide on-site installation?
- Are the alarm thresholds appropriate?
- Is ongoing, cloud-based monitoring available to help us catch failures?
- Who owns the data?
- For cloud-based data, how long do you store it?
- How much training is included in your packages?
- Is the training on-site or virtual?
- Are in-house, certified vibration analysts available to help with remote monitoring and machine diagnostics?
- Is the data full-spectrum or trend-line only?
- What is the frequency of full-spectrum readings?
- Is the battery proprietary or Duracell?
- What is the battery life?
- Is the system a true wireless or an “octopus” system?
- How large is the footprint of the wireless signal?
- How will the wireless signal impact my mill’s other wireless signals?
- Is there a cell modem option, or am I forced to ask my IT department for bandwidth?
- What is the price (sensors, collection servers, software licensing, troubleshooting, training and ongoing analysis)?