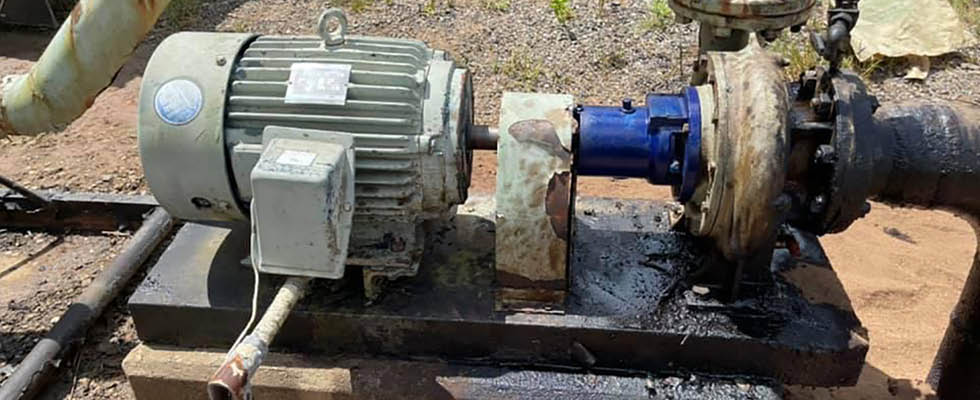
Pumps are a competitive market that can be made simpler through honesty, integrity and putting people first. Since downtime is one of a user’s biggest concerns, it may sometimes be beneficial to fix up an old pump when needed. This can mean a multitude of things, such as the pump needed having a long lead time, or the pump no longer being manufactured. It could also mean putting another brand/manufacturer in place is the right solution.
Recently, an aftermarket repair company worked closely with a pump company based in Texas. A municipal lift station was in dire need of getting their system up and running. They were nearing overflow on their waste tanks, and there was not a pump/vacuum truck to buy time. The OEM pump in place was several days out from being able to have an answer. The aftermarket repair company made a phone call to the pump company and had a pump on-site four hours later ready to install. It may not have been an exact replacement, but it fit perfectly where it was needed.
Sometimes it is not as easy as picking up the phone and making one call. There will be times when it takes a whole team and a handful of logistics to get the job done. For example, in one instance, a user had a small pump, which in this case was obsolete and impossible to find. It needed to be rebuilt immediately, but it had a broken shaft. In this case, a visit to the “bone yard,” where old pumps go to die, provided the answer. After finding an old pump in poor shape, tearing it down and discovering the types of bearings and seals it used, it was possible to track down the parts by contacting several different companies across the country. In about six hours the freshly rebuilt pump was in place and running again. It could be argued the money needed to achieve this goal was considerable, but it was worth it to the user who could now avoid costly downtime. Through direct communication and transparency, what seemed like a difficult task was made much more possible.
To be of the best possible help to a user, it is critical to have the willpower to stick around and properly diagnose what is wrong with a pump or system when a problem arises. Using critical thinking to diagnose a situation with what is on hand, rather than spending unnecessary money, can often mean a lot to any user.
Recently, at an amine plant, the head (H) pump on the system had excessive vibration, and the problem needed to be determined quickly. With a little research, it was possible to find out what their booster pump was and where exactly on the curve that pump was going to produce the correct amount of flow rate needed for the main pump. Given the pressure it was producing, it was not giving the proper amount of fluid the main pump was demanding. With the click of a button, they were able to switch to their backup booster pump, which had a completely different pounds per square inch (psi) output, stopping the vibration in the main pump.
With this diagnosis, it was made clear that either the impeller and casing were worn and not producing at peak efficiency or the impeller to casing clearance was not set at the right tolerance. So, without taking the pump out of the system and by asking the operators of the plant if they had seen a gradual decrease in pressure over the past year, the answer was determined. Because the pump had been at that pressure constantly over the past year, by unsetting the mechanical seal, sliding the impeller toward the casing to the appropriate measurement and resetting the seal, the pump was instantly putting out 20 psi more than before. What could have been a costly and unnecessary task was avoided thanks to critical thinking and ingenuity, and the issue was resolved with just an hour of downtime.