Common Pumping Mistakes
Summit Pump Inc.
01/11/2017
The famous Swiss psychiatrist and psychotherapist Dr. Carl Jung is often quoted as saying, “What you resist persists.” I always took it to mean that because I had problems with calculus in college, I would always be in professional positions that would require me to be proficient in the subject. I was painfully correct. If you do not set goals and face these situations, the things that you resist will persist by repeatedly popping up, typically at the most inopportune times. In this new year, I propose we work on items on this “resist” list of common damage-causing issues for pumps.
1. NPSHA Mystery
The subject that requires the most attention is understanding net positive suction head available (NPSHA). Some people resist learning about it because the name and subject can be difficult and confusing. Others believe they know all about the concept, but their calculations and applications prove otherwise. Their pumps consequently cavitate, incurring expensive damage and downtime. The “resisting” category also includes anyone who thinks that NPSHA is purely a function of suction pressure, suction energy and/or static height (submergence), as in having a flooded suction. I propose that the subject is really not that difficult. There are numerous sources of information and instruction on this topic. Pumps & Systems has published many articles on the subject—several in the last couple of years. A good starting place is my Pumps & Systems column from August 2015 titled “Rethinking NPSH” (read it here).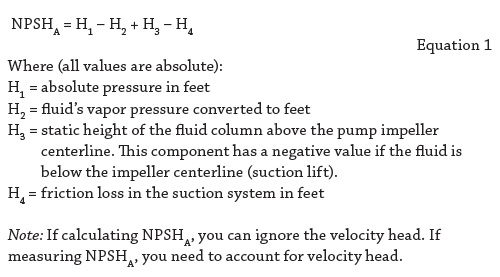
2. Best Efficiency Point
Operating the pump away from the best efficiency point (BEP) is the second most common issue affecting pumps. I acknowledge that, in many applications, operators or owners are helpless to do anything about the situation because of circumstances beyond their control. Others can look to change something in the system that allows the pump to operate where it is designed to run. Just as someone should not drive a car down the interstate in first gear, end users should not operate a pump near the shutoff point. Helpful options include variable speed operation, trimming the impeller, installing a different size pump or a different model pump, and/or changing something on the system that could be as easy as installing a three-way control valve or an orifice.3. Pipe Strain: The Silent Pump Killer
A pump is the most expensive piping hangar you can purchase. It seems that piping systems are often not properly designed, installed and/or anchored. Provisions for thermal expansion and contraction are often not considered. I observed a situation where pipe strain was the suspected root cause of bearing and seal issues. After we instructed the mechanics to remove the pump foundation bolts, the 3,200-pound pump was lifted several inches by the piping. For those who are not sure, that is an example of severe pipe strain. Another way to check is to place dial indicators on the coupling in the horizontal and vertical planes, then unbolt either suction or discharge piping. If the dial indicators show more than 0.002 inches of movement, there is too much pipe strain. Repeat for the other flange. The coupling should have inserts/spacers removed.4. Preparing for Startup
Pumps of any size, other than fractional horsepower close-coupled, rarely arrive at the final site ready to start up. Pumps are not “plug and play.” End users must add oil to the bearing housing, set the rotor and impeller clearances, set the mechanical seal, and perform a rotational check of the driver prior to installing the coupling. Read and understand the instruction book.5. Alignment
The alignment of the driver to the pump is critical. No matter how well the pump was aligned in the manufacturer’s facility, the alignment was lost the second the pump was transported. If you aligned the pump when it was set in place, it was likely lost when you connected the piping.6. Oil Level & Cleanliness
More oil is usually not better. In ball bearings with splash lubrication systems, the optimal oil level is when the oil is touching the very bottom of the bottom ball. Adding more oil just increases friction and heat. Remember this important point: The biggest cause of bearing failure is contaminated oil.7. Running the Pump Dry
Submergence (simple submergence) is defined as the distance (D) measured vertically from the liquid’s surface to the centerline of the inlet suction pipe. A more important descriptive term is required submergence, also known as minimum or critical submergence (SC). Required submergence is the vertical distance—from the fluid surface to the pump inlet—required to prevent fluid vortexing and fluid rotation (swirling and or pre-swirl). Vortexing will introduce unwanted air and non-condensable gases, which can cause pump damage and reduce pump performance. A centrifugal pump is not a compressor, and performance is significantly affected when pumping dual and/or multi-phase fluids (gas and air entrainment in the fluid). There are simple formulas and charts to calculate how much submergence is required. For more on this topic, see my April 2016 Pumps & Systems article titled “Guidelines for Submergence & Air Entrainment.”8. Driving Blind
You cannot manage (or repair) what you do not measure. Use gauges or pressure transducers on all pumps. Gauges will measure pump performance and display the differential pressure across the pump. That information, along with knowledge of the pump and system curves, will provide details about the equipment’s health. The differential pressure across the pump is key to knowing where the pump is on its operating curve. Knowing where the pump is on the curve is critical for managing the pump’s health. Converting the pump’s differential pressure to head will provide a location on the curve. Convert pressure to head by multiplying the differential pressure by 2.31 and divide the product by the specific gravity. Compare your results to the manufacturer’s performance curve.9. The Pressure of Knowing Vacuum
Vacuum is a subject that causes confusion. A thorough understanding of the subject is especially important when calculating NPSHA. Remember that even in a vacuum, there is some amount of (absolute) pressure—however small. It just is not the full atmospheric pressure you have normally worked with at sea level of 14.7 pounds per square inch gauge (33.95 feet). For example, during an NPSHA calculation involving a steam condenser, you will likely have a case where there is 28.42 inches of mercury (inches Hg) of vacuum. Even with this high vacuum, there is still 1.5 inches Hg of (absolute) pressure in that vessel. The pressure of 1.5 inches Hg converts to 1.71 feet of absolute head. For background: A perfect vacuum is about 29.92 inches Hg. The difference is how much pressure still exists in the vessel (29.92 – 28.42 = 1.5 inches Hg). The 1.5 inches Hg (multiply by 1.139 to convert) is equal to 1.71 feet.10. Wear Rings & Impeller Clearances
Pumps wear out. As clearances wear and open, there are negative effects on the pump (vibrations and unbalanced forces). In general, pump efficiency will decrease one point for every one-thousandth of an inch (0.001) for the first 0.005 to 0.010 inches the clearances open (from original settings). After the clearances open by 0.020 to 0.030 inches from the original clearance, the efficiency begins to drop exponentially. At some point of gross inefficiency, the pump is just agitating the fluid—killing the bearings and seals in the process.11. Suction Side Design
The suction side is the most important part of the pump. Fluids do not have tensile properties/strength. Consequently, a pump impeller cannot reach out and pull fluid into the pump. The suction system must provide the energy to deliver the fluid to the pump. The energy may come from gravity and a static column of fluid above the pump, a pressurized container/vessel (even another pump) or simply from atmospheric pressure. Most pump problems are on the suction side of the pump. Think of the whole system as three separate systems: the suction system, the pump itself and the discharge side of the system. If the suction side of the system adequately provides fluid energy to the pump, then the pump, if properly selected, will handle most of the issues that occur on the discharge side of the system.12. Experience & Training
Do you have 30 years of experience or one year of experience that is 29 years old? Stephen Covey, the author of “7 Habits of Highly Effective People,” identifies the seventh habit as “sharpening the saw.” The short version of what he means is that even the people at the top of any profession are constantly working to improve their knowledge. Pumps will operate more efficiently and reliably if you know how to accomplish the goal.
To read other articles in the 'Common Pumping Mistakes' column, go here.