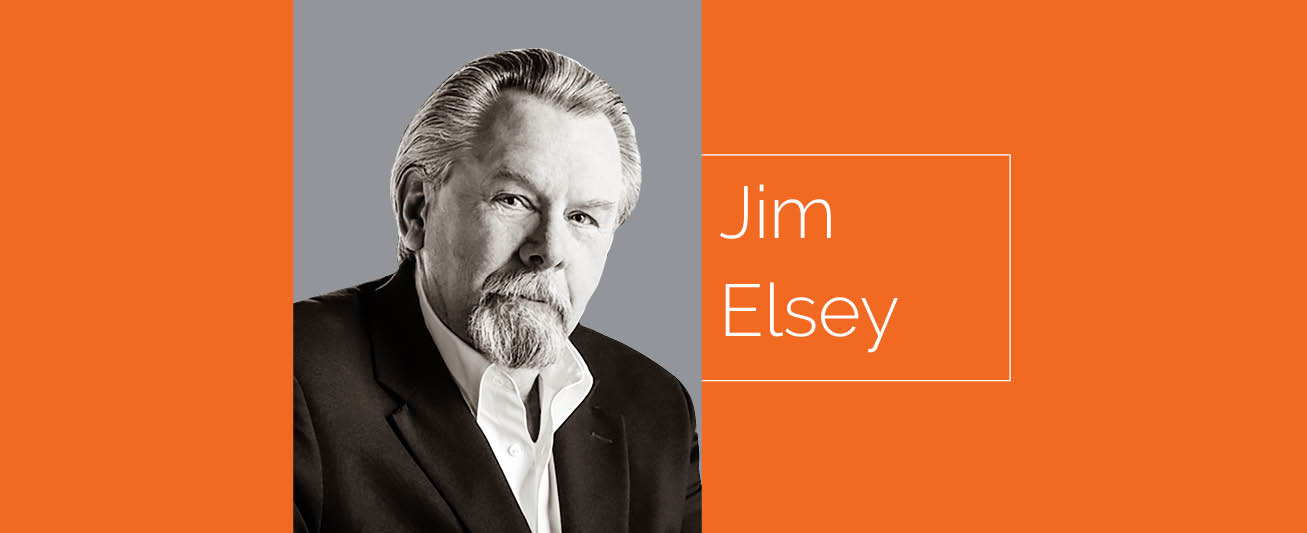
Here I go again on the tedious subject of net positive suction head (NPSH). I know it seems like this is my favorite subject, but before you turn the page, NPSH is a critical subject that pops up daily in my work. (And for the record, anyone who knows me will tell you my favorite topic is maximizing small block Chevy engines.)
This column will address possible mitigation steps to correct an existing situation where the NPSH margin is not sufficient. My comments are based on pumping water.
There is good news and bad news. The good news is there are several potential ways to correct situations with inadequate NPSH issues. The bad news is that most mitigation measures will be cost prohibitive and objectional to the equipment owner. It is best to avoid the issue in the first place because the corrective solutions, if any, are typically painful.
NPSH Margin
The suction side of the pump system must somehow supply the energy required by the pump (above vapor pressure) to avoid cavitation issues. Contrary to urban myth, the pump is not capable of reaching out and pulling the liquid into the eye of the impeller. The energy will typically come from gravity (static head) or atmospheric pressure but may also be induced by an external pressure source.
Equation 1:
NPSH Margin = NPSHa/NPSHr
It is incumbent on the system owner or their proxy to determine the amount of NPSH available (NPSHa). The pump manufacturer will in turn test the pump and publish the amount of NPSH required (NPSHr). To avoid/mitigate cavitation issues, you must have more NPSHa than NPSHr. The ratio of NPSHa to NPHSr is referred to as the NPSH margin.
A general rule of thumb is to have the system provide a minimum of more than 3 to 5 feet available than the pump requires. Designing by this thumb rule will eventually land you in trouble, and I recommend you read and follow Hydraulic Institute 9.6.1 guidelines and standards for proper margin. Sometimes even a 30-foot margin (ratio 1.5) will not be enough. Also, realize that even with a high margin, you are not truly eliminating cavitation—you are just hopefully lowering it to a level that will not cause pump performance or material degradation issues.
Tip: If you are not already aware, please understand that the published NPSHr numbers for a pump (also referred to as NPSH3) can be slightly misleading to the uninitiated. In the test process for determining NPSHr, the operating pump is held at a constant flow rate and head and simultaneously forced to a point of cavitation by lowering the NPSHa. When the head drops by 3%, that NPSH point will be the published data point for NPSHr. That is, at conditions where NPSHa equals NPSHr the pump will cavitate. Or another way of stating it is the pump is already cavitating at the published point.
This is not some dirty little secret—the industry has been doing it this way since 1903 (formally adopted in 1932), but sometimes the OEMs need to be better at communicating to the end users. In defense of the pump manufacturers, there are no easy methods to accurately conduct these tests.
The Formula Is Your Friend
I learned this maxim initially in college and later it was tattooed into my brain during my U.S. Navy nuclear power training: “When in trouble…start with the formula to find the solution.” And so, to this day I still tell my students that the “formula is your friend.”
The easy formula for calculating NPSHa appears in Equation 2. One at a time, examine the factors in the formula. See my previous column in the October 2021 issue or consult “Cameron Hydraulic Data” book chapter 1 for detailed definitions and conditions for the individual terms.You should always calculate NPSHa for the worst conditions (think tank/sump levels and maximum flows at the highest temperatures). Also, look at and add for the system age and fouling factors. All of the factors in the formula should be expressed as absolute.
An alternative method is to measure NPSHa in the field. I recommend using the formula specified in Hydraulic Institute 9.6.1. Note the difference between the calculation of NPSH and measurement of NPSH.
Equation 2:
NPSHa = ha - hvpa +/- hst - hfs
Where:
• ha = absolute pressure
• hvpa = vapor pressure
• hst = static head (positive if flooded; negative if a lift)
• hfs = friction head
• Note: Not shown is velocity head (hvel), which can be ignored in most cases. However, if you are measuring (empirical tests in the field) you should consider the factor and note it possesses a positive sign. If you are simply calculating NPSHa using the above formula, it is not necessary to include. If the suction piping system is undersized it will be
a factor.
Absolute Pressure
This is the absolute pressure pushing down on the liquid source. If it is an open system, it is the atmospheric pressure (barometric) pushing down on the surface. Note that the atmospheric pressure changes with altitude above (or below) sea level, consequently the pressure must be adjusted for altitude and converted to absolute terms. If the system is closed, you will need to look at the pressure and convert to absolute head. If the system is in a vacuum, first realize there is still some pressure in a vacuum—it is just a pressure lower than atmospheric.
Now, let’s look at what we can do to change this first factor to our benefit in a situation with insufficient NPSHa.
In the event of an open system, chances are the owner is not going to change the weather or move the plant to an area of higher atmospheric pressure (lower elevation). There is not anything commercially feasible we can do about this situation. In the event of a closed system, there is a remote possibility that the pressure can be increased, but real-world issues and process requirements will normally preclude any changes. Nevertheless, ask the question and expect some negative critique. Closed hydronic systems can typically have the pressure increased slightly with little to no issues.
Vapor Pressure
Next up is vapor pressure. If you are not familiar, please review my April 2018 column, “Under Pressure: The Dangers of Vapor Pressure.”
Vapor pressure is temperature-dependent for the liquid you are pumping. The higher the temperature, the higher the vapor pressure. Because the factor is always negative, vapor pressure is never your friend in the race for more NPSHa. To improve NPSHa, the mitigation step is to lower the liquid temperature if you can. Again, the system owner will fight you on this because in almost every case there is a good system design reason why the temperature is what it is. To lower the temperature in a process typically means the temperature will need to be raised (heat added) somewhere else in the system and the overall cycle efficiency will be reduced. In my 50 years in the business, I have only one example of a user acquiescing to lower the temperature of the process.
Static Head
As explained earlier, the static head factor will be positive if the suction is flooded and negative if the pump is on a lift.
In industrial and process plants, there is good reason you will see so many pumps with the suction source elevated and/or the pump location in a lower level or basement. The reason is to gain/maximize static head. In countless NPSHa calculations I have made, the static head is the only factor that allows the system to work correctly. Go to any plant that has a steam system and look for the condensate pumps—with the possible exception of packaged boilers, the condensate pumps will always be on the lowest level. The plant owners don’t want the initial construction expense (elevated towers and excavations), but it is a smart compromise to increase equipment reliability and reduce the cost of operations and maintenance over the life of the plant.
On your mission to increase NPSHa on a system with flooded suction, you can increase the height of the supply source and/or lower the pump. Both options are expensive and disruptive to plant operations. In my career experience, I’ve had two instances where the pump owner accepted one of these changes.
Note: For suction lift situations, if possible/feasible you can set the sump levels higher to reduce the lift. My experience with this option usually reveals it is either not feasible or the gains are small.
Friction Head
The last factor in the NPSHa formula is friction. This is a factor that can sometimes be manipulated. In recent years I have witnessed clients making pipe changes on several occasions. Pipe changes, like the other factors, can be expensive and disruptive. The added gremlin that often surfaces in these cases is artificial financial restraints on the size of equipment and plant footprint. One sector of upper management will demand a small plant footprint to reduce cost, but often these decisions are made in the absence of a reliability champion with a long-term perspective on total cost of ownership (TCO).
Calculate the friction head and look at the suction velocity. Look for methods and means to reduce the friction and velocity. I have seen systems so poorly designed and constructed that we were able to easily correct the NPSHa issue by simply installing unobstructed straight pipe of the proper size. Yes, there was some downtime and cost associated with the project but in the overall picture, the return on investment (ROI) was realized in less than a year.
The Formula Was Fun, But My Mission Failed
As I predicted at the beginning of the column, most of the time the required corrections will be either cost prohibitive or not feasible. Now the question becomes, what else can I do? I offer the following list of possible mitigation methods.
1. Operate the pump in a region that requires less NPSHr. Not always possible, but I have also been surprised by the number of times the client was not aware the pump was operating too far right or left on the curve.
2. Very small amounts of air or gas introduced into the suction side of the system will mitigate the negative effects of the cavitation damage. The pump performance will be slightly diminished.
3. Be aware that 1% air entrainment is normally the maximum limit and amounts exceeding 1% will have a negative effect.
4. Investigate a different type of impeller. Many manufacturers will have alternate impeller offerings for a given pump model and size. Ask the manufacturer if they have an impeller that requires less NPSHr. Note that the optional impeller will most likely be of a higher suction specific speed (Nss) and may present recirculation issues in the operating areas between shutoff and best efficiency point (BEP). Some choices will and some will not, but you need to ask.
5. Investigate another pump model or different manufacturer. Either decision will at the very least involve piping changes and perhaps foundations, baseplates and electrical supply changes.
6. You can improve NPSHa and/or reduce NPSHr by eliminating items that protrude into the piping such as instrumentation and even the penetrations themselves. Also, look at changing the impeller leading edge vane profile and the surface finish of the pump, especially the impeller.
7. Change the speed of the pump to be slower, which will commonly play out as a change to a different pump. NPSHr varies approximately as the speed ratio squared. For example, if your current pump is operating at 3,550 rotations per minute (rpm), you can choose a pump that is operating at 1,750 rpm and expect the NPSHr to reduce by somewhere in the range of 50%. The caveat will be that the new pump will be about twice the physical size of the original pump. The good news is that the added cost will eventually play out as reduced maintenance and longer mean time between failures (MTBF).
8. Switching to a different style pump/impeller may help. Horizontal split case pumps have dual suction impellers that will reduce the NPSHr by approximately 50%. Some OEMs offer vertical pumps with dual suction first-stage impellers—a real winner on condensate systems because the pump can be extended (further down) into a pit/can to gain more static head and at the same time offer a 50% reduction in NPSHr with the dual eye impeller.
9. An often-overlooked remedy to fix NPSHr issues is to add a booster pump in series. Instead of trying to accomplish all of the hydraulic head requirements in one step, look at doing it in two steps. The booster pump could also be a slower speed to reduce NPHSr requirements even more. If space requirements preclude adding a booster pump, look at changing the base pump to a two-stage, which is in essence doing the same thing, just in one casing/volute.
10. An alternative subset of adding a booster and/or two-stage pump is to change to a pump that can incorporate an inducer. I warn end users not to add inducers on their own. Inducers must be matched to the impeller.
11. My next-to-last suggestion is to live with the cavitation but treat the symptom by changing the impeller material. I don’t have room for details, but your pump manufacturer will be able to inform you of materials that resist cavitation damage better than others.
12. I know of at least a dozen clients that simply live with the results of insufficient NPSH. Their cost analysis and business decisions are that it is just simpler to live with the issue and replace impellers, mechanical seals and bearings on some regular maintenance schedule.
In the end, it is always simpler and less costly to first calculate and allow for a proper NPSH margin and then select the correct pump in the first place.