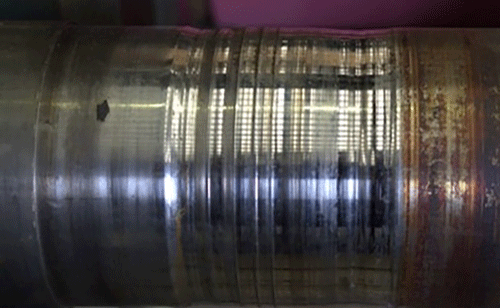
Rotating shaft seals can be found in virtually every facet of daily lives—household appliances, cars and trucks and across industries. Though often treated as a commodity product, their failure can result in costly downtime and lost productivity. Despite their use in countless applications, many still have basic questions about how to use them. Here are some frequently asked questions.
1. What is a retainer plate (cover plate), and why is it required with an all-rubber split seal?
A cover plate is a piece of metal (or other hard material) installed after the oil seal has been placed into the housing bore. The cover plate pushes on the back side of the oil seal and compresses it into the housing. All-rubber split seals require cover plates because this style does not have an outer reinforcement to help retain the seal, so it needs compression inside the housing to ensure the best possible sealing capability.
2. Which direction should the lip face when installing my oil seal?
A single lip seal is unidirectional and will only seal in one direction. The primary sealing lip should always be facing or pointing toward the media that needs to be sealed. The media being sealed is usually a grease or oil lubrication, but it could also be a chemical media that needs to stay inside of a tank. If the seal is to function as an excluder and keep out contamination, the seal should face out towards the contaminant, which could be dirt and dust or chemical washdown. Sometimes seals will either have a secondary lip or dual opposed lips to keep dirt or contamination away from the bearing system and/or the media being sealed.
3. Which rubber material should I select for my oil seal?
Proper material selection is essential for good sealing performance. One of the factors that drives elastomer selection is the application temperature. A common rubber used in many sealing applications with mild operating conditions is nitrile (NBR), which is generally rated for use up to 200 F (continuous). Nitriles offer low cost and good wear resistance but will harden and/or crack if used at elevated application temperatures. At temperatures higher than 200 F, some choose carboxylated or hydrogenated nitrile (HNBR), which are generally rated for use up to 300 F (continuous). Another type of elastomer used at higher temperatures would be a fluoroelastomer (FKM), rated for use up to 400 F (continuous). However, in exchange for the higher temperature capability, the cost of these materials will be higher than the standard nitrile.
Aside from temperature considerations, some applications contain chemical media that might require a more compatible material like fluoroelastomer (FKM) or even polytetrafluoroethylene (PTFE), which can be impervious to many chemicals. It is important to note that PTFE lip material is closer to a plastic than an elastomer and will have different application considerations.
4. Which lip seal material(s) should I use if my application requires FDA compliance?
The food and beverage industry often requires FDA compliant seals. This means that the lip and case materials must meet FDA standards for sanitation. Some available lip materials that are FDA compliant include FDA Silicone, FDA Viton and some PTFE formulations, to name a few. If the seal has a metal case, FDA compliance requires the use of 316SS. Additionally, much of the equipment in food and beverage applications needs cleaning or steaming when in use. The seals must withstand the cleaning chemicals and the high temperatures associated with these processes.
5. Which lip seal material or design might be recommended for an application with harsh chemicals?
Depending on the application, some applications exposed to chemical media might require a PTFE lip seal, which will be compatible with the widest range of chemicals. In addition, some PTFE lip seal designs can withstand high pressures and dry running conditions that standard elastomer seals cannot. PTFE seals can be found both with and without a metal case, and can be installed in the same groove as a traditional oil seal.
6. Should I select a seal with a metal case or rubber outer diameter (OD)?
Seals with a metal case generally have the most OD interference, or ability to remain inside the housing. The trade-off for this extremely tight fit is that housing damage might occur when a metal case seal is installed. Some users prefer a rubber OD seal because it will not scratch or damage the housing during the installation process. Changing to a rubber OD seal might also do a better job statically sealing previous housing damage caused by a metal-cased seal. Another consideration is that standard steel metal cases might oxidize or rust over time. This would not be a concern with an all-rubber or metal-encapsulated rubber OD seal.
7. I have removed my leaking oil seal from the equipment. How do I know what size oil seal I need?
When replacing a failed oil seal, do not measure the used seal, as it will give erroneous measurements. Along with the fact that different manufacturers use different design interferences, used and worn-down oil seals often suffer damage during removal. Manufacturers design oil seals to fit the user’s equipment, so all a user needs to do is provide the seal manufacturer with the equipment’s shaft diameter, bore diameter and bore depth. Also, check
the markings on the seal, as some oil seals display the equipment dimensions that it requires.
8. How are oil seals measured?
Under most circumstances, users will not need to measure the oil seal. To size the seal correctly, users only need to know the shaft diameter, bore diameter and bore depth of the equipment.
Users might need to measure the seal, though, if they are trying to verify its manufactured size. The most important dimensions on an oil seal are the inside diameter (ID), outside diameter (OD) and width (height). The ID of the seal is not measured directly, as it is difficult to do without stretching or altering the lip. The OD of the seal measures most accurately with a special piece of equipment called a pi tape. The pi tape can consider any out-of-round condition with the seal that a pair of calipers might not. The seal’s width (or height) measures best with a pair of calipers, taking a few measurements around the whole diameter.
9. Does oil seal thickness matter?
As long as the seal correctly fits the shaft and the bore diameters, there is not any sealing advantage to different seal widths. If the seal is larger in width than the actual bore depth, the only potential issue might be interference with the surrounding equipment. Conversely, if the seal width is smaller than the actual bore depth, this is usually not a problem unless the seal is an all-rubber style being compressed by a retainer or cover plate. In this case, the best practice is to take up the extra space inside the bore housing with gasket spacers to ensure correct compression on the seal by the cover plate.
10. What is the purpose of the spring used in oil seals?
The spring provides loading around the sealing circumference and keeps the sealing lip tight against the shaft surface. Some seal designs use a garter spring design, which applies pressure everywhere around the shaft. Other seal styles employ a finger spring design, which provides an independent finger action only in areas where needed. Spring dumping can happen to garter springs, as they typically rest inside a molded groove disconnected from the sealing lip. If the spring dislodges during installation, for example, it can enter the equipment at startup, often causing serious damage to expensive bearings and other equipment. Finger spring designs, however, are usually either molded in or mechanically connected to the seal so the spring will not fall off or damage the equipment.
11. How long does an oil seal last?
Seal life is difficult to determine on equipment in the field because operating conditions are unknown, and they vary considerably. Furthermore, the applications are usually not ideal (defined as clean lab-type environments, fully lubricated, low speed, ambient temps, no pressure, no misalignment or runout, no exposure to chemicals or solids, correctly sized components, etc.), and the reality is that these factors change seal life considerably.
12. I replaced my oil seal and found the shaft grooved underneath the lip. What causes this, and what should I do?
When grooving occurs at the shaft, this is typically a result of shaft hardness and/or finish not meeting industrial recommendations of a minimum 30 Rockwell C and 10 to 20 microinches Ra. The lip materials themselves will not cause shaft grooving, however, if there is dirt or contamination in the application. It might be possible for some particles to stick underneath the lip and groove of the shaft if it is too soft. It is not recommended to install a new oil seal over shaft grooving, as this could likely result in leakage. Cover any shaft grooving with a shaft sleeve, or offset the new sealing lip to contact a surface free of grooves or scratches.
13. Should I glue the ends of my split seal back together during installation?
If the split seal needs a garter spring, there will generally be a hook or screw attachment that will pull the two split ends together. Some other split seal designs, with a finger spring, hold tightly together by the interference (or press fit) between the OD of the seal and the machined bore housing. In either case, it is generally not recommended to glue the split ends of the seals back together, as it is difficult to get the lip alignment correct. Also, the chemical compatibility of the adhesives and lip elastomer requires testing.