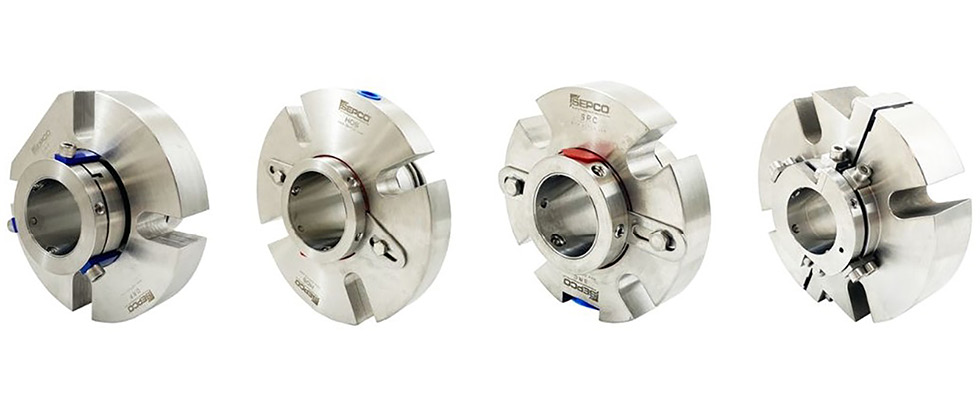
1. Operating Condition Changes Impact Reliability
Dry gas mechanical seals rely on a thin gas film to separate the seal faces, minimizing contact and wear. However, this design makes them highly sensitive to changes in operating conditions such as pressure, temperature and gas composition. When these parameters fluctuate, the gas film can destabilize, leading to face contact and premature seal failure.
Liquid mechanical seals benefit from the lubricating and cooling properties of the liquid film, which can be less susceptible to external variations. This inherent stability allows liquid seals to maintain performance even under dynamic conditions, making them an option for applications with frequent operational changes.
Case study insight
A 2018 study by the Texas A&M Turbomachinery Laboratory highlighted that dry gas seals in hydroprocessing units often fail due to external factors like sudden pressure spikes and contamination from hydrocarbons. Liquid mechanical seals, with their ability to tolerate such variations, demonstrated high reliability under similar conditions.
2. Maintenance Requirements
Dry gas mechanical seals are sophisticated devices that require precise alignment, specialized materials and advanced environmental control systems. These complexities demand highly trained personnel for installation, maintenance and troubleshooting. A lack of expertise can lead to improper handling, reducing seal performance and increasing downtime.
Liquid mechanical seals are comparatively simpler in design and operation. They require less specialized knowledge to maintain, which reduces the risk of errors and associated costs. The availability of standardized components and straightforward repair processes further enhance their appeal for facilities with limited technical resources.
Industry feedback
A LinkedIn discussion by Zubair Talha highlighted the challenges of retrofitting dry gas seals into existing compressors, noting that the intricate environmental control systems can lead to additional failure points. Liquid seals, with their simple requirements, avoid such complications.
3. Short- & Long-Term Costs
The initial investment for dry gas mechanical seals is significantly higher than for liquid mechanical seals due to their complex design and the need for auxiliary systems like gas panels and filtration units. Over time, the cost disparity grows as dry gas seals often require more frequent inspections, replacements and specialized repairs.
In comparison, liquid mechanical seals can offer a more economical solution. Their low upfront cost, combined with reduced maintenance expenses and long service life, aligns with the budgetary constraints of many industrial applications. Furthermore, the widespread availability of liquid seal components contributes to cost savings by minimizing downtime and ensuring rapid repairs.
Economic analysis
A 2022 American Fuel & Petrochemical Manufacturers (AFPM) report on seal reliability noted that dry gas seals’ lifetime costs often exceed budget expectations, particularly in applications where operating conditions are not ideal. Liquid mechanical seals consistently performed in terms of cost-effectiveness and operational efficiency.