In establishing the Pump Energy Index to rate the energy performance of commercial and industrial pumps, the U.S. Department of Energy (DOE) estimates that 0.29 quadrillion British thermal units (BTUs) will be saved between 2020 and 2049, which translates into a savings of about 10 gigawatt-years of electricity. Energy conservation has been a driving force behind the DOE’s five-year process to regulate pump efficiency in the U.S., which is changing industry perception of what constitutes an efficient pump. Since the Energy Conservation Standard for Pumps became effective this spring, manufacturers have been seeking guidance from the Hydraulic Institute (HI) and other industry leaders on the necessary steps for compliance by 2020. This article is intended to be a general overview of the steps to compliance with the DOE standards and testing for pumps; the complete DOE rules provide greater detail. With members of HI and others working closely with the DOE to develop the new regulations, the test procedures closely follow the HI’s existing test methods contained in HI 40.6-2014, Methods for Rotodynamic Pump Efficiency Testing. However, there are some exceptions and additional requirements put forth by the DOE to ensure repeatable and reproducible test results and to provide measurement methods and equipment specifications for the entire scope of pumps under the rule.
1. What Will Be Tested?
The first step is to identify the parameters for each pump that falls under the rule. The standard targets five classes of rotodynamic pumps designated for use in pumping clean water in commercial, industrial, agricultural and municipal applications:- end suction close-coupled (ESCC) pump
- end suction frame mounted (ESFM) pump
- in-line (IL) pump
- radially split, multistage, vertical (RSV) in-line casing diffuser pump
- submersible turbine (vertical turbine submersible [VTS] pump)
2. What Are the Metrics?
As noted above, the DOE has established a new metric called the Pump Energy Index (PEI) to rate the energy performance of pumps. Beginning Jan. 27, 2020, all pumps distributed in commerce in the U.S. must have a PEI less than or equal to 1.00. The PEI is a ratio of the representative performance of the pump being rated over the representative performance of a pump that would minimally comply with any prospective DOE energy conservation standard for that pump type. Minimally compliant pump efficiency is determined by a calculation that includes specific speed, the BEP flow in gpm and a constant (C) that varies by pump type. This determines the Pump Energy Rating (PER), the weighted average of input power to the motor at defined duty points, and is the standard basis for all PEI ratings. The DOE’s rules on testing outline the steps to calculate PER in greater detail. The ruling requires testing methods for both constant load and variable load equipment classes. A metric of pump energy index constant load (PEICL) applies to pumps sold without variable speed controls; pump energy index variable load (PEIVL) applies to pumps sold with variable speed controls. Both PEICL and PEIVL describe the weighted average performance of the rated pump at specific load points, normalized with respect to the performance of a minimally compliant pump without controls. DOE test procedures also contain methods to determine the appropriate index using either calculation-based methods and/or testing-based methods. Calculation refers to default loss calculation for a driver or driver and controls that are applied to bare pump test data. Testing-based methods refer to measuring wire-to-water power consumption inclusive of the driver and controls when applicable. Figure 1, compiled by HI, is a guide to select the appropriate test method.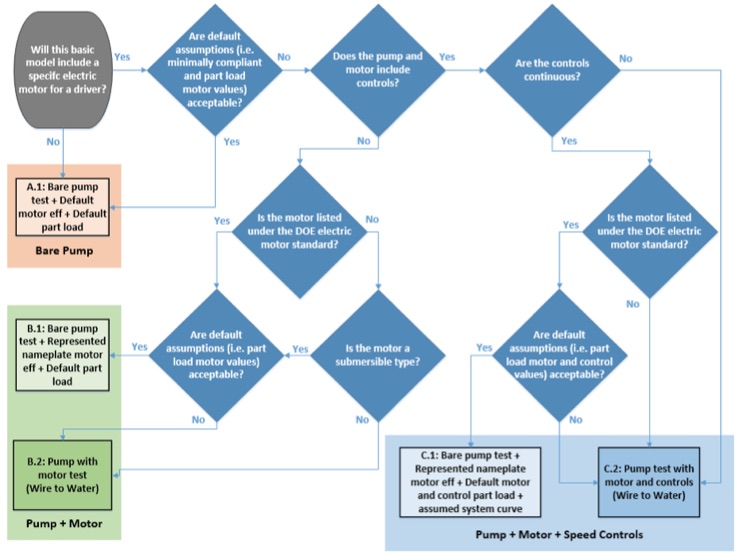
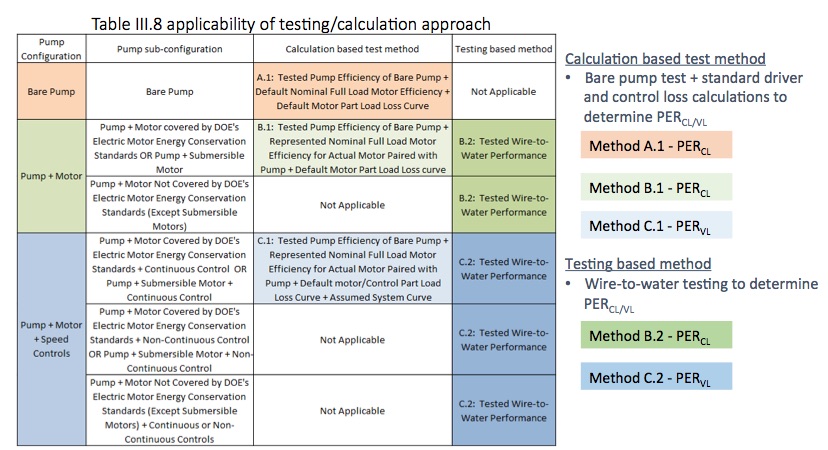
3. What Is Required During Testing?
In setting up the actual testing procedures, the DOE follows HI 40.6 guidelines for permissible amplitude of fluctuation and the maximum permissible measurement device uncertainty. In addition, the DOE requires that at least two unique measurements be recorded more than five seconds apart and their mean computed. The DOE also requires that the two unique measurements are not farther away from the mean than the tolerance specified in the permissible amplitude of fluctuation table. Any damping devices are only permitted to integrate up to the data-collection interval.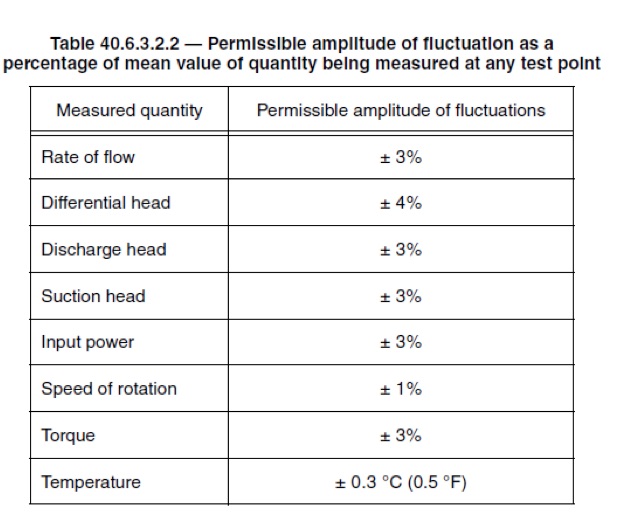
- At 40, 60, 75, 90, 100, 110 and 120 percent of BEP
- At 40, 50, 60, 70, 80, 90 and 100 percent of expected BEP if expected BEP is within 20 percent of the maximum flow