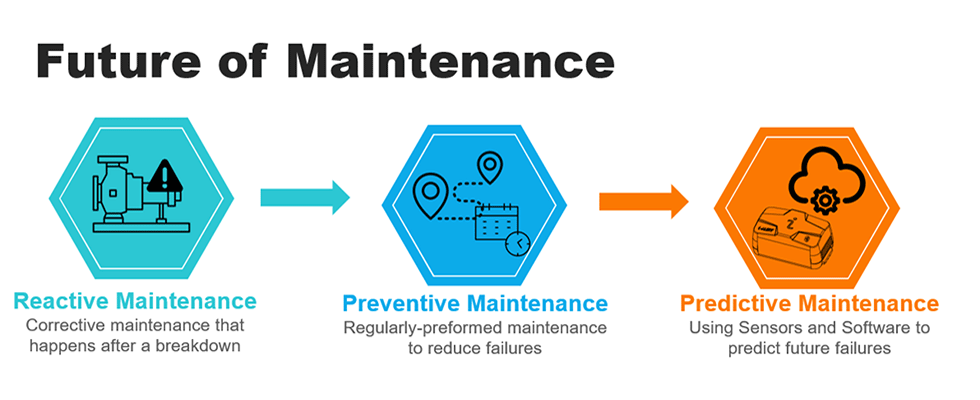
Machine unpredictability is at an all-time high. Traditional machine monitoring can be tedious, and multistep diagnostic processes can complicate maintenance needs when an issue arises. If a user does not have the right technology or service in place, it can become the job of multiple different employees to collect and analyze data before determining a solution. With an advanced reliability program or partner in place, this waste of time, money and resources will be a thing of the past.
With advanced technology, reliability programs can monitor the health of the whole facility, not just the ones that are deemed critical. This can also be accomplished while staying within budget and not intruding on infrastructure. This is done with wireless smart sensors, on edge computing and cloud-based platforms where data can be analyzed, viewed and shared seamlessly to the respective individuals or team.
Smart sensors work by monitoring and logging different parameters such as vibration, speed and temperature of machinery, thereby capturing transient events and malfunctions in real time. This data is then processed and presented to the end user with actual solutions.
This is preferably done using wireless communication that can ensure security while having sufficient bandwidth for remote capabilities. The solution is an easy and smart way to ensure machinery is functioning correctly, and the reliability team can be alerted of issues before they become serious risks. Better yet, working with a full-service monitoring partner will ensure that problems with machines are identified, evaluated and brought to attention where resources are limited. This will take a user from being reactive to predictive as fast as possible.
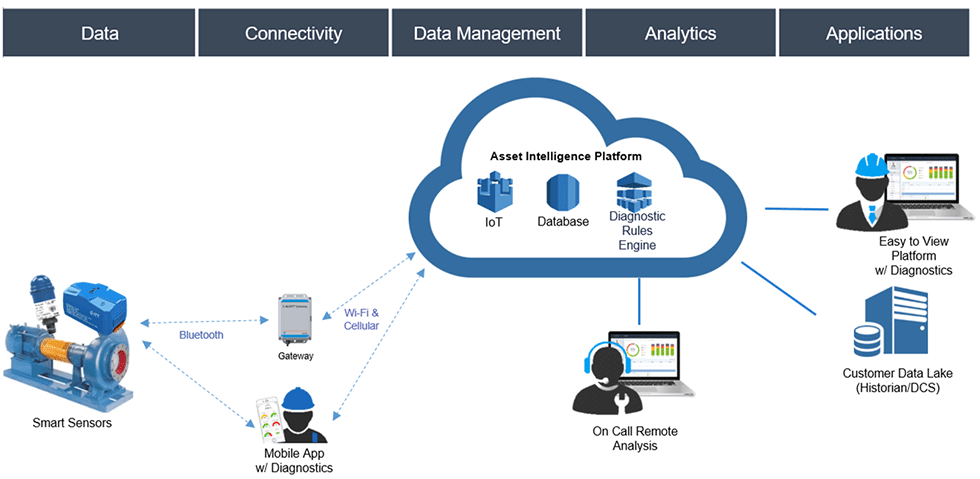
Here are some of the benefits of working with real-time condition monitoring to manage the health of machinery.
1. Flexibility of Services
When partnering with a reliability solution service provider, companies can choose to be hands on or hands off with the analysis of their data. Services are flexible and customized based on what the company’s goals are and what metrics they value the most. Basically, corporate leaders can rest assured that their machines are in good health while they focus on other important aspects of the business.
Flexibility is important when it comes to integrating the new technology to already existing programs. Many facilities have an existing process to monitor, analyze and fix machine issues. The goal is not to reinvent the wheel, but to advance the program so that resources are optimized, data is analyzed faster and results are presented in an environment that complements the existing methods.
2. Less Downtime, Increased Productivity
When something goes wrong with a machine, it can waste time and raise costs. Not only will there be a disruption in production, but there could be injuries or property and environmental damage that puts a financial strain on the business.
Sensor service technicians help companies by training the staff on how to maintain a healthy and efficient facility by educating them on techniques to monitor and flag data that could be indicative of a machine issue. This is critical, as the dysfunction of the smallest machine part can have a major impact on the overall performance of the machine. Paper machine bearings, for example, are critical to the machine function. If one fails, paper production is brought to a standstill. Having smart technology on these machines to keep them running smoothly can safeguard revenue streams. It is important to note that these services were only implemented in the past on machines that were deemed critical due to resource constraints. By advancing to the use of smart sensors, the whole facility can benefit from predictive methods of monitoring without overextending resources.
3. Stable, Experienced Support Staff
As many employees have left their jobs over the last two years, finding top engineering and technology talent is becoming more difficult. This is more apparent when it comes to finding skilled individuals with experience analyzing complex data and maintaining industrial machine health. For companies without sensor solutions and partnerships with machine health experts, diagnostics and solutions can be costly, hard to manage and very reactive.
Whether directly or through distribution partners, working with a smart sensor provider can ensure uninterrupted support. Vendors often have local sales techs, customer service representatives and service-shops made available.
4. 24/7 Risk Mitigation
For critical equipment and processes, the reliability partner can assure an unplanned event is not missed. All the sensor and process data from companies are transferred to the reliability partner in real time where it is reviewed by vibration experts. This allows experts to perform an informed and educated analysis to ensure the quickest, earliest identification of the potential issue. Most companies will find that the lead time for response will be reduced by approximately 50%.
A recent example of using continuous monitoring was in a facility that handles hazardous fluids, where the system caught high vibration levels indicating a malfunction. On-site staff was alerted in real time and was able to shut down the pump immediately. It was then discovered that the pump had a broken impeller and severe washout. As a result of quick detection, the factory was saved from potentially catastrophic consequences to the staff, property and the environment.
No matter how it is done, diligent monitoring of machine health is critical to a company’s uninterrupted operations. With current technology and services companies can have a pulse on the machine health of the entire facility without overextending resources.