Advanced test analysis tools, remanufacturing and training help end users solve problems.
03/23/2015
Once a machine or system is up and running, monitoring the asset's operation and performance and deploying proper solutions when problems develop can pay big dividends. With the increasingly demanding needs in the marketplace to more effectively manage and support assets, various aftermarket tools, technologies and services have emerged to help operations successfully do the job. Specialized tools collect data regarding machinery health and detect system abnormalities. Similarly, remanufacturing (rather than replacing) components to full working specifications, as well as maintaining spare parts inventory and management services, can be quick and cost-effective ways to minimize downtime.
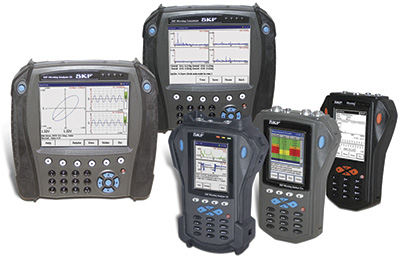
Evaluating Machinery Health
Owning and operating equipment is one of the biggest costs for a plant. Global competitive pressures have increased demands to keep operations running better, longer and more cost-effectively by reducing unscheduled downtime and increasing uptime for machinery assets.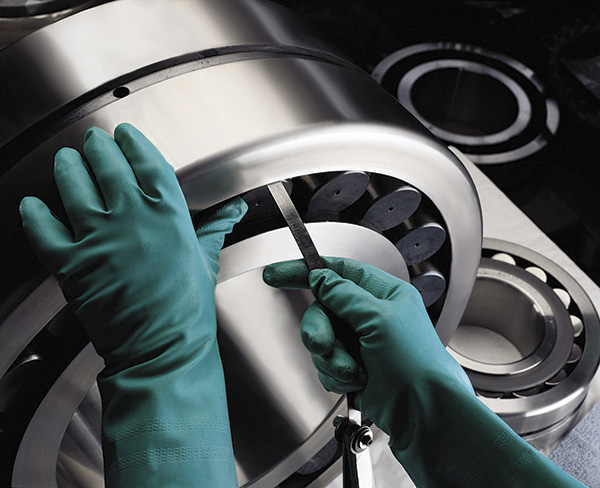
- Basic handheld condition monitoring tools place the benefits of condition-based maintenance within reach for experts and novices alike. Examples include thermal cameras, vibration measurement tools, stroboscopes, tachometers, sound pressure meters, ultrasonic instruments and electrical discharge detectors.
- Portable data collectors and analyzers supported by enabling software can handle all tasks needed to perform on-the-spot analysis of rotating machinery.
- Online surveillance and protection systems integrate permanently installed sensors for machine monitoring to alert plant personnel of deteriorating machine condition changes. Data are transmitted to a host computer running applicable software. The technology is especially suited for unsafe or hard-to-reach locations where accessibility is limited.
- Electric motor test equipment encompasses a wide range of product solutions offering capabilities for static testing and dynamic motor monitoring to help plants avoid unexpected electric motor failures.
Remanufacturing vs. Replacing
When good components go bad, replacing them can be expensive, both in terms of cost and delayed availability. Remanufacturing can be an alternative way to save time and money without compromising performance or productivity.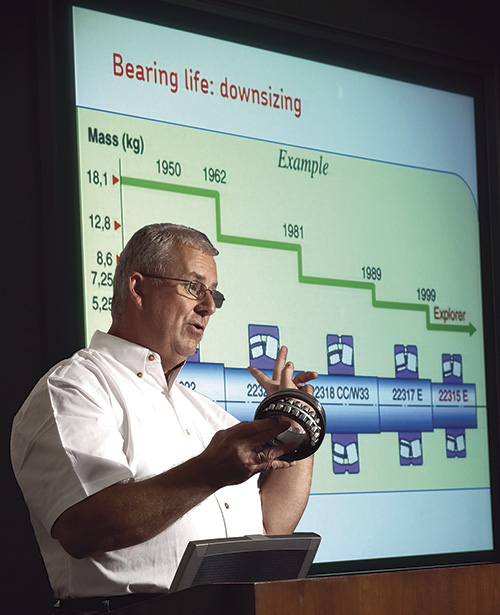