Positive displacement pumps can provide cost savings over similar dewatering solutions.
ABEL Pumps L.P.
03/02/2017
Positive displacement (PD)pumps are chosen for some of the most challenging slurry pumping duties. Here are four important factors to consider when choosing a PD pump for mining applications.
1. Abrasive Wear
Mining slurries tend to be abrasive with solid specific gravities of 2.65 or more and slurry specific gravities of 1.65 or greater at solids concentrations as high as 70 percent. Abrasive wear varies with velocity. End users should consider the effects of abrasive wear during pump selection. PD pumps operate at relatively slow speeds and are effective in transporting mineral slurries. This industry utilizes the progressive cavity and rotary lobe designs found in PD pumps; however, the slurry’s path travels through tight places, such as rotors and stators or lobes. These designs are unfavorable to abrasive wear in intense applications and should never be run dry. One of the best pump options for this duty are piston diaphragm designs that can run dry and are highly abrasive-resilient. Slurry does not pass through tight constrictions. Instead, elastomer diaphragms are used, and they are relatively passive in displacing the slurry. As a result, the diaphragm’s fatigue limit—not so much the abrasion—determines the diaphragm life.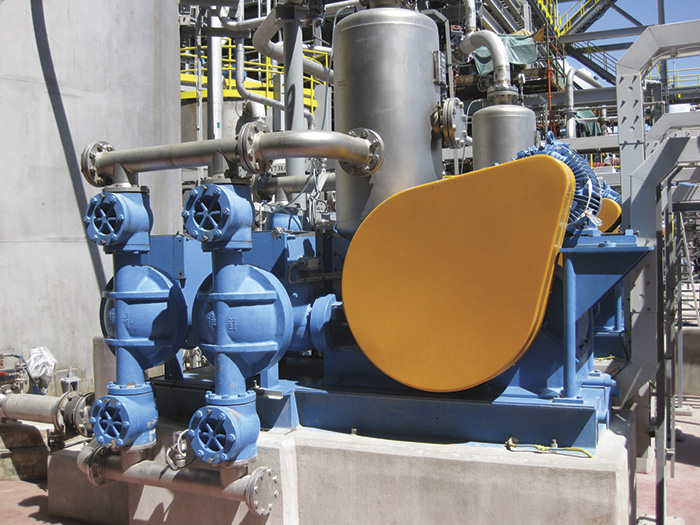
2. Maintenance
Some applications such as mine dewatering allow end users to pick between staging centrifugal pumps or using a high-pressure PD pump. Lowest initial capital cost often favors the staged centrifugal pumps; however, other factors need consideration. Maintenance of centrifugal slurry pumps can be considerable compared with PD pumps, which require maintenance only on an annual or semi-annual basis.3. Operating Efficiency
PD pump efficiencies may run as high as 90 percent. Centrifugal pumps have a peak efficiency at their best efficiency point, but actual efficiencies could be considerably lower. In one example, six centrifugal pumps are placed in series to pump a tailings slurry at 55 percent solids with a combined discharge pressure of 1,022 pounds per square inch (psi). Capacity per pump is 910 gallons per minute (gpm). Assume efficiency per pump is 55 percent. Power use per pump is 165 horsepower (hp) or 123 kilowatts (kW). For six pumps, the total power consumption is 738 kilowatts an hour (kW/hr) or about 6.1 million kilowatts a year (kW/year). A PD piston diaphragm pump operating at 90 percent efficiency consumes, by comparison, about 3.7 million kW/year. Savings, assuming 10 cents per kW, is about $238,000 per year. The six centrifugal pumps each need gland seal water. Assume each gland seal water pump uses 30 gpm of water, pumping at 750 psi and consuming 18 kW per gland seal water pump—or 107 kW for the six pumps. The pumps run 8,300 hours per year.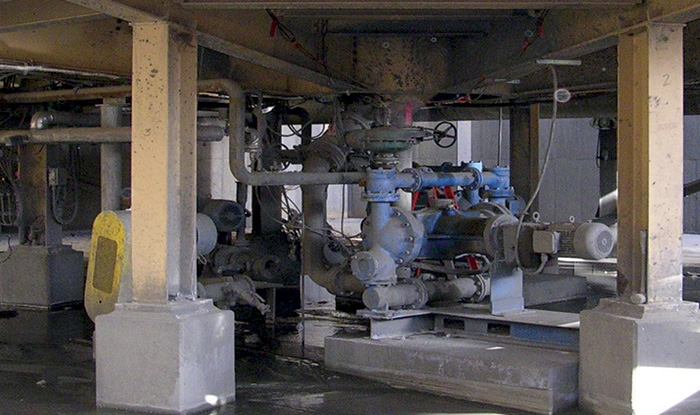