The best components and algorithms can bring peace of mind.
Siemens
04/10/2018
Level devices are small components that are critical for keeping systems running smoothly. Across industries, operators need precise data and reliable equipment. With the right level device in place, they can focus on more complex system requirements.
1. Mining Process Tanks with Circulation Conditions
Richard Lemire is electrical technical coordinator at the Laronde division of Agnico Eagle Mines Limited, one of Canada’s largest mining companies. Lemire gets called in when things are not working. He is the problem-solver when instrumentation is not delivering the results that the mill needs. The mill operators were frustrated with the performance of Agnico Eagle’s standard level transmitters in several process tanks with circulation conditions. “Every time the recirculation is started, the surface becomes quite turbulent and the environment fills with vapor,” Lemire said. “And almost every time, the transmitter would have difficulty tracking the level.” Lemire consulted an instrumentation provider who recommended that their technology and algorithms would likely work with default settings, even with these difficult conditions. “They said that all we had to do was set up the geometric tank properties using quick start parameters,” Lemire said. “The transmitter worked with no special adjustments and has been reporting the level very reliably where others didn’t.”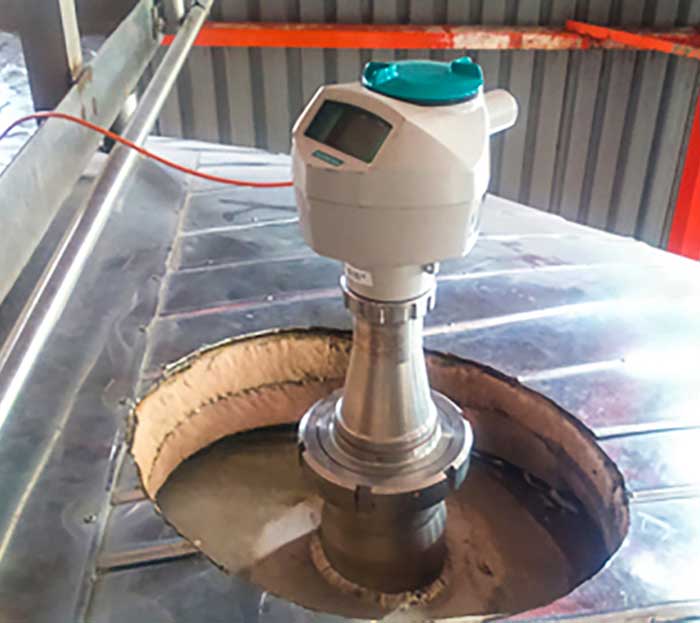
- Noncontacting radar and ultrasonic technology’s advanced echo processing enables reliable and accurate level measurement, dealing with obstructions and changing environments.
- Guided wave radar can be installed in a matter of minutes.
2. Cement Kiln Dust’s Second Life
One type of radar transmitter measures levels in a U.S.-based company’s process and storage vessels for cement kiln dust (CKD), an unavoidable byproduct of cement production that is used for many different commercial applications. The transmitter’s high-frequency antenna does not have any issues with the extremely dusty environment inside either vessel. In addition, the device’s narrow beam allows technicians to install them almost anywhere on top of the vessel.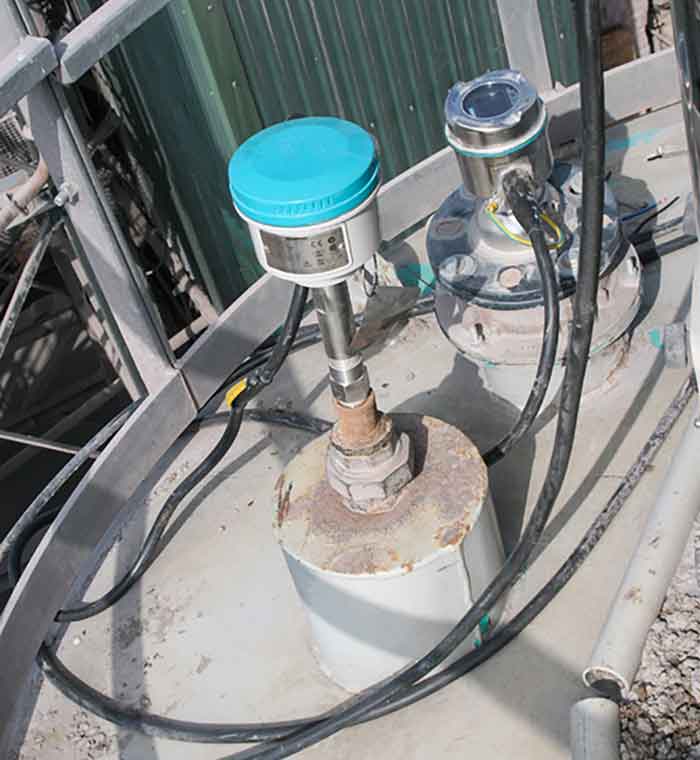
3. Global Standard for Fill Measurement
Today’s brewing industry is characterized by a constantly growing range of varieties and bottle shapes, as well as increasing cost pressure. This led to a growing need for hygienic, reliable and low-cost systems capable of measuring the precise content of pressurized tanks prior to filling, as well as fermenting and storage tanks. To meet this need, multinational brewing and beverage company SABMiller chose a radar level transmitter with hygienic antenna. SABMiller installed the transmitters on vessels that are continually filled and emptied throughout brewing operations.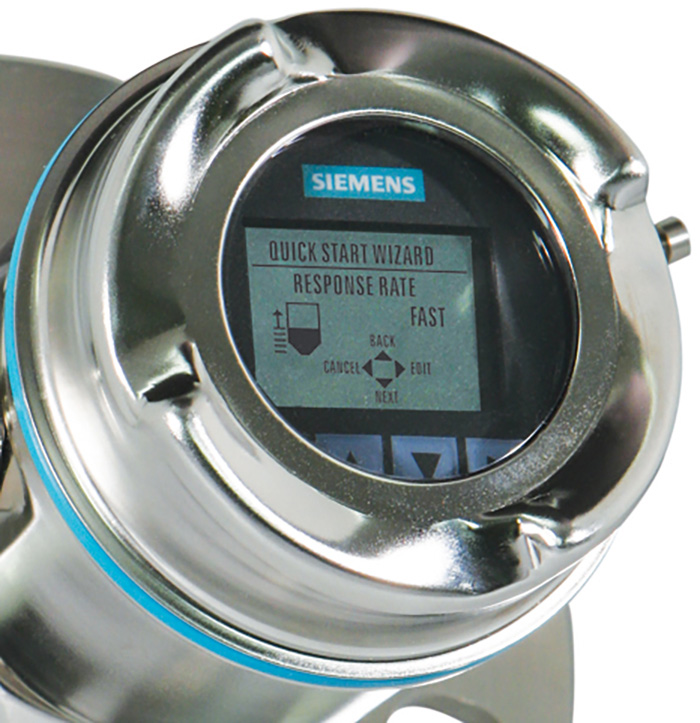
4. Taking the Uncertainty Out of Pump Control
In a peaceful Canadian city, a wastewater pumping station had difficulties with its existing level controller. Pumps were turning on and off randomly—and not at the desired set points. This type of malfunctioning can result in potential flooding of the well or can cause damage to the equipment.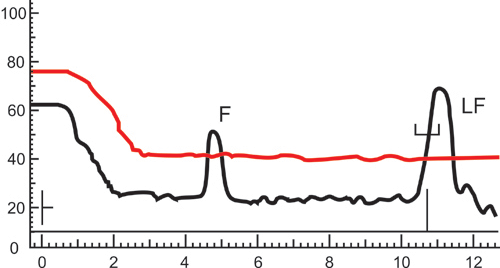