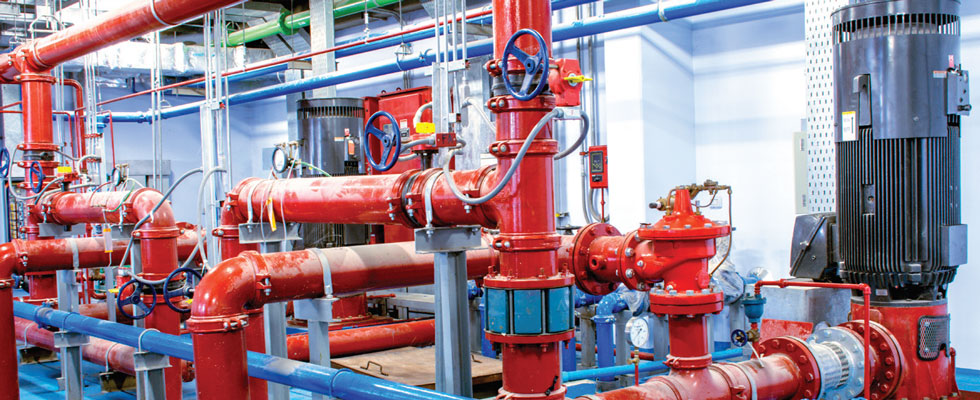
The pump regulations communicated in National Fire Protection Association (NFPA) 20, the standard for the installation of stationary pumps for fire protection, are designed to ensure fire protection systems work as intended when needed to deliver adequate and reliable water supplies. The NFPA 20 2019 edition includes several changes that impact variable speed fire pump motors, which are growing in popularity as the number of applications they serve grows. Here are five items of interest for users who manufacture, specify, install and oversee fire protection systems.
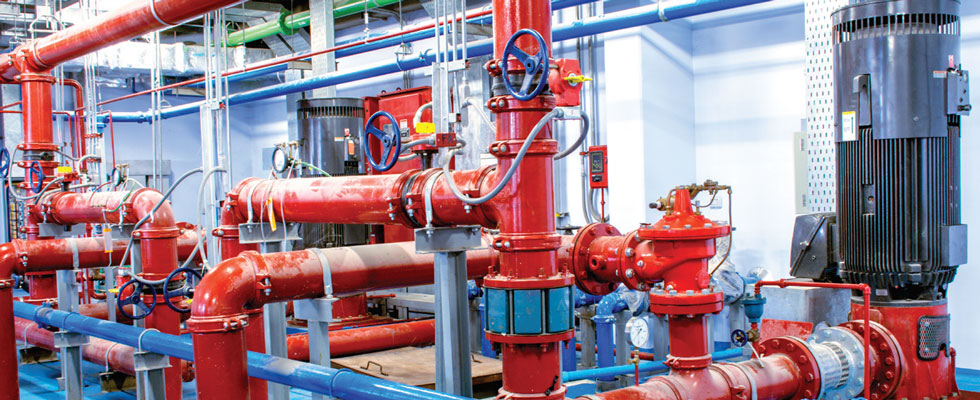
1 - While service factor has previously been allowed on sine wave motors, the 2019 edition allows it to be applied to fire pump motors driven by variable frequency drives (VFDs).
In general terms, service factor is a measure of the overload capacity a motor can operate at periodically without incurring damage. A motor that operates continuously at a service factor greater than 1 will typically have a shorter life expectancy than one operating at its rated nameplate horsepower (hp).
NFPA 20 defines service factor as “a multiplier of an alternating current (AC) motor that, when applied to the rated hp, indicates a permissible hp loading that can be carried at the rated voltage, frequency, and temperature.” A multiplier of 1.15 indicates that a motor is permitted to be overloaded to 1.15 times its rated hp.
Section 9.5.2.4 later adds, “General-purpose (open and drip-proof) motors, totally enclosed fan-cooled (TEFC) motors, and totally enclosed nonventilated (TENV) motors shall not have a service factor larger than 1.15.”
NFPA 20 Section 9.5.2.2 explains how to apply service factor to fire pump motors. It states, first, that “the maximum service factor at which a motor shall be used is 1.15.” It adds that “where the motor is used with a variable speed pressure limiting controller, the service factor used shall be as marked on the motor, but in no case exceed 1.15.”
NFPA Section 14.2.6.6.5 states, “For electric motors operating under varying voltage, the product of the actual voltage and current demand on each phase shall not exceed the product of the rated voltage and rated full-load current times the allowable service factor.”
2 - The relationship between VFD ratings and motor service factor is detailed in the 2019 edition.
According to NFPA 20 Section 4.8.7, “The current rating of the variable frequency drive (VFD) shall not be exceeded when operating in the motor service factor.” Further, Section 9.5.1.4.2 states, “Motors shall be listed, suitable, and marked for inverter duty.”
This means that fire pump motors are labeled as inverter duty motors, with amps based on the motor running on the VFD. When selecting motors, it is critical to understand how the motor manufacturer interprets NFPA 20’s language on service factor limitations.
The selections should also consider that NFPA 20 allows up to a 5 percent drop in voltage at the contactor and the voltage drop must also account for voltage unbalance.
There are other restrictions to consider. Section 9.4.4 states that “the voltage at the contactor(s) load terminals to which the motor is connected shall not drop more than 5 percent below the voltage rating of the motor when the motor is operating at 115 percent of the full-load current rating of the motor.”

3 - NFPA 20 states that service factor is about amps, not power.
The 2019 edition includes an important specification related to ampere ratings. The standard does not allow amps for a motor at 1.15 service factor to exceed 115 percent of the full-load current of the motor—despite that being a typical condition.
As Section: 9.5.2.1 explains, “The motor capacity in horsepower shall be such that the maximum motor current in any phase under any condition of pump load and voltage unbalance shall not exceed the motor-rated full-load current multiplied by the service factor.” This point cannot be overstressed. The load on the motor is limited by the full-load amps multiplied by 1.15. Traditionally, service factor is applied to the power. Here, it is applied to current.
To be clear, NFPA also specifies that other system electrical equipment be sized at around 115 percent of the full-load current. A couple of those components include the isolating switch and the circuit breaker. Section 10.4.3.3.1 says circuit breakers “shall have…a continuous current rating not less than 115 percent of the rated full-load current of the motor.”
If motor amps at a 1.15 service factor exceed 115 percent of the motor’s full-load current, the motor under NFPA is restricted to the amp limitation, not the power limitation. Consider a 100-hp, 3,600-revolutions per minute (rpm) motor with nameplate sine wave full-load amps of 113 and service factor amps of 131. Because 113 x 1.15 is equal to less than 130 amps, the service factor amps of 131 exceeds the standard’s limit. In this case, the motor will most likely only be able to deliver 114 hp at 130 amps, rather than the 115 hp expected by the 1.15 service factor in traditional thinking.
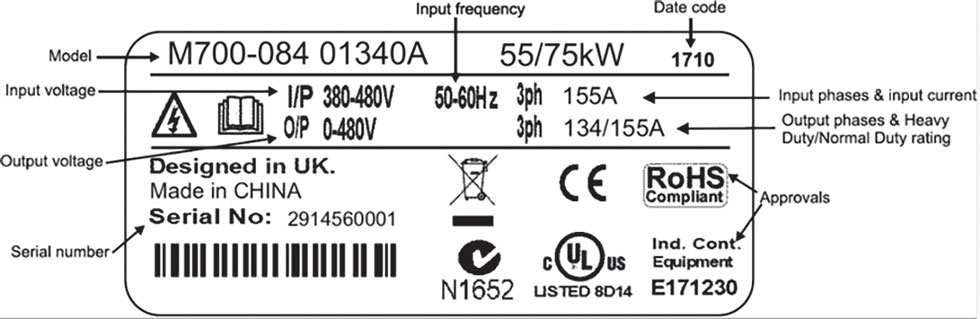
4 - Name-plating policies and harmonic- and waveform-induced increases in motor amps require special consideration.
It is generally accepted that motors on VFDs draw higher current than when running on sine wave power based on the harmonic content and the non-sinusoidal waveform of the insulated-gate bipolar transistor (IGBT) switching device. (IGBT is a three-terminal power semiconductor device that combines high efficiency and fast switching.) A switching frequency on the low end of the IGBT spectrum, such as 2 to 4 kilohertz (kHz), tends to have higher motor amps, compared to a motor that runs toward the higher end of the IGBT spectrum at 12 to 15 kHz. Because a higher switching frequency lowers the efficiency of the VFD and can require a de-rate of the VFD output, switching frequencies are often set at the default level of a lower switching frequency.
A motor manufacturer’s inverter duty motor name-plating policy now must be considered. NFPA 20 requires that fire pump motors intended for use on a VFD be labeled for inverter use. Members of the motor industry vary on their approach to this issue, with some manufacturers listing only the sine wave amps value described earlier.

The actual amps increase over the sine wave level varies by VFD, switching frequency, cabling and other factors. A conservative multiplier is 5 percent.
Consider the same 100 hp example cited above, only now with a VFD. A 100-hp, 3,600-rpm motor with nameplate sine wave full-load amps of 113 would have a limit of 130 amps. If a full-spectrum frequency current measurement device is used by the inspector at the motor terminals at a full 1.15 of load point, the amps measured would likely be 131 x 1.05 = 138 amps. If measured from the full-load sine wave amps, the actual maximum hp may be as little as 110 hp.
If the inverter full-load amps are used, the result would be 113 x 1.05 = 119 amps. The 1.15 amps value in that case is 138, which leads back to the same result as sine wave at 114 hp maximum.
The choice of labeling for the full-load nameplate amps on the motor is critical to the hp output that will be allowed per the standard upon installation. Other factors to consider based on amps limitation include voltage lower than the rated system voltage or any level of unbalanced voltage in the power supply.
5 - Complying with NFPA 20 requires fire pump motors and VFDs to be limited and sized for amps, not power.
While pumps are traditionally sized around torque and power, the translation to amps is essential for meeting the NFPA 20 standard. All electrical items in a system must be sized for amps.
Section 10.10.1.3.1 also reminds us that “the current rating of the variable frequency drive (VFD) shall not be exceeded when operating in the motor service factor.”
VFDs are certainly amp-rated products. In fact, VFDs often conveniently list hp, a reference that is helpful when selecting the VFD for an application. Historically, VFD amps for the referenced hp were sized and based on the NFPA 70 amp ratings for electric motors.
Be aware of the rating values and make selections based on amps and loading values. The table below is a good reference for NFPA 70 values, as well as motor values on sine wave and VFD for full load and service factor. As the table makes obvious, a VFD based purely on NFPA 70 amps values will not meet the NFPA 20 fire pump VFD amp capabilities for use of the motor service factor.