Few deny that demands from the manufacturing and energy sectors will continue to drive industry growth. In this era of demanding conditions, operational efficiency has never been more vital. International pressures require machine shops to compete at a higher level, doing more with less, and manufacturing facilities have been forced into 24/7 operation. As a result, equipment reliability has become a core industry concern. With increased competition saturating topline revenue growth, businesses are focusing on improving operational efficiencies and managing cost centers to impact their bottom lines. To achieve the coveted near-zero downtime, companies begin by evaluating their maintenance programs. Preventive maintenance had its place 20 years ago, but new technological advances allow for more refined and reliable methods of tracking machinery health and avoiding potential failures. Predictive maintenance—as the name suggests—leverages data collection to enable users to predict when equipment failure might occur so they can implement maintenance before equipment breaks down. Several reliability-centered maintenance (RCM) programs attempt to do this with monthly or quarterly samplings of temperature, vibration, lubrication, loads, pressures and other parameters. Analytics enable engineers to move from an original equipment manufacturer (OEM) specified maintenance regimen to one that is defined by actual usage and observed failure intervals.
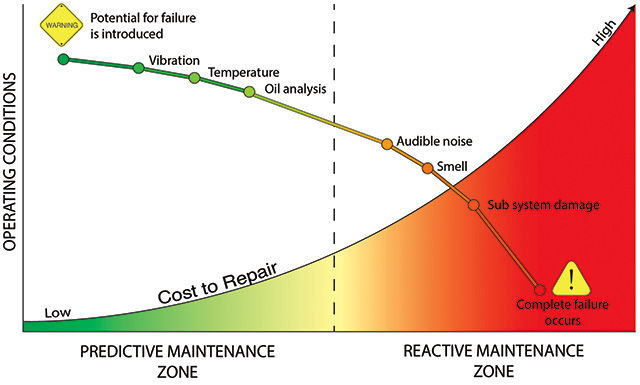
1. Percentage Yield
Manufacturing companies often measure operational efficiency by percentage yield. This strategy involves optimizing equipment and processes to produce the greatest number of quality products possible. Continuous tracking and quality testing are key to optimizing yields, but monitoring machinery also may help achieve this purpose. Continuous machine monitoring empowers engineers with a real-time stream of information regarding the status and health of equipment. It unlocks (through data analytics) real-time insights into the slightest changes in operating conditions—changes that directly affect the quality of the products. This varies from traditional maintenance programs, which are limited by intermittent information and a lack of real-time insights. Because parts rarely fail without warning, the goal of continuous monitoring is to identify weak or poorly implemented controls so that they can be corrected or replaced before yield is affected. Consistency in operation and smoothly running machines directly contribute to a higher percentage yield.2. Capacity Utilization
Capacity utilization is ensuring a facility operates at maximum production capacity by improving equipment availability. If a facility uses a predictive and prescriptive approach via continuous monitoring, it will reduce the amount and cost of downtime. To achieve more uptime and better capacity utilization, plants should plan maintenance around load rather than planning load around maintenance.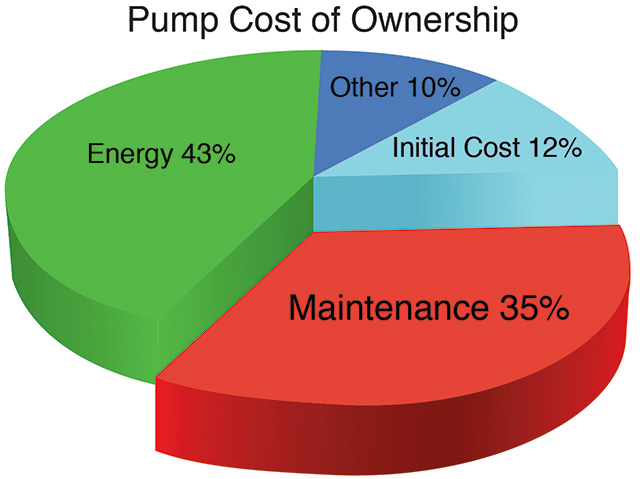
3. Overall Equipment Effectiveness
Operational efficiency is often measured by overall equipment effectiveness (OEE), which breaks a manufacturing facility’s performance into three measurable components: availability, performance and quality. Continuous data gathering and analytics are key to understanding how assets are functioning in real time. Continuous monitoring offers actionable insights that empower operators to make better decisions. If machinery does not meet its intended level of performance, machine operators must be alerted immediately, not with uninterpretable numbers, but with actionable information (i.e. imbalanced loads, power mismatch, over/under lubrication, etc.). This information is especially imperative given that 5 to 15 percent of machine failures are a direct result of improper maintenance and incorrect usage.