Many pumps fall prey to a myriad of problems that include corrosion and being crushed by heavier machinery.
Tsurumi America
12/12/2016
No industry puts its pumps through the ringer quite like mining. When the price of commodities such as gold spike in the short term, there is no time to lose—companies have to act fast to extract whatever they can as quickly as possible. While this flurry of activity is great for stockholders, it is not ideal for equipment. Many pumps end up falling prey to a myriad of problems that range from corrosion to being crushed by heavier machinery. To protect mine dewatering pumps to the fullest extent, consider these six common threats that pumps may encounter during mining operations.
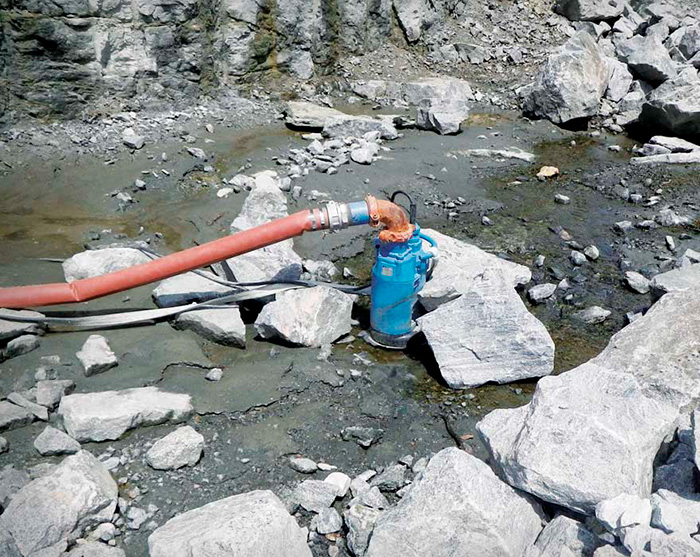
1. Suspended Solids
The most prevalent cause of mine dewatering pump failure is clogging from gritty, suspended solids and slurry. Water that makes direct contact with the operation is often dirty, containing foreign materials such as drill cuttings or solids generated by underground ramp traffic. When combined with the clean water that is removed from an aquifer, the result is a slimy texture that can clog pumps. The key to overcoming this challenge is proper sump design. Clean water should be collected at the source, while abrasive solids-laden water should be separated into an isolated area within the sump.2. Corrosion
The fluids in mining applications are among the most volatile a pump can move. From superheated water laden with pyrite, iron or sand, to emulsified brine phase drilling fluid, there is no shortage of liquids that will punish a pump over time. If a pump is constructed using solid metallurgy, the corrosion process can be slowed to a degree. Stainless steel pumps are preferred in these applications, including one new series of submersible dewatering pumps that are manufactured using SCS14, a cast equivalent of 316 stainless steel. Even the hardiest equipment can succumb to corrosion, so it is important to make use of sacrificial anodes to increase the life of cathodic protection. An anode made of metal with a lower electrode potential—such as magnesium, zinc or aluminum—will take the brunt of corrosion during the pump’s application, protecting the metal that composes the pump. These protection plates must be monitored and replaced before they corrode completely.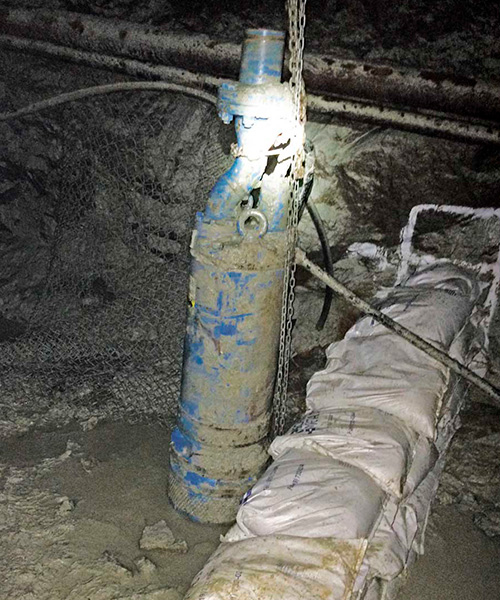
3. Impact
This is as simple as it sounds: If a pump is not kept sufficiently away from mine traffic, there is a greater risk of crushing the pump with larger, heavier equipment. Location is key, and keeping a pump away from the mine’s primary activities can mean the difference between getting the job done and halting everything for a costly pump replacement.4. Overheating
Overheating can occur in any pump application—and mining is no different. If water levels are too low in the sump during prolonged operation and the unit’s control panel lacks any sort of underload protection, the pump will run dry and overheat. Suspended solids also can cause overheating by accumulating in the cooling chamber and, if concentrated enough, around the motor frame. Suspended solids are another reason to carefully monitor water levels and make sure dirty water is kept separate from clean water.5. Cord Damage
When a pump’s power cord is cut or otherwise damaged, water can pass into the copper conductors through the point of cable entry and wick back to the motor. This will lead to motor failure or a short circuit in the cable. Pulling on the cord during improper lifting or moving of the pump is often the culprit. This kind of cord damage is a symptom of hasty mining operations and results in costly repairs. Careful handling of pumps is necessary to keep cable entry intact.6. Unexpected Culprits
While this may come as a surprise to some, about 20 percent of all mining pump failures stem from clogs caused by everyday materials. Chief among these culprits are earplugs, which all workers need and often discard; assorted types of fibers, such as the steel fibers used to reinforce shotcrete; and blasting wire, which can wrap around the pump’s impeller. All of these materials are ubiquitous in mines, which makes them all the more likely to cause clogging issues. Any one of these items, if improperly discarded, can jam a pump’s impellers. It is not uncommon for a mining operation to send a pump to a distributor for repair, only to discover that improperly discarded debris has caused the unit to fail.Mitigate Abuse in Mining Applications
Many advancements in pump technology can mitigate the abuse pumps face in a mine, such as anti-wicking cable entries, silicon carbide mechanical seals or high chrome impellers. But these six hazards listed can befall even the most reliable equipment. By taking the time to safeguard an operation from these six common, simple mistakes—preferably with assistance from engineers throughout the job’s life cycle—mining operations can extend the lifespan of mine dewatering pumps well past what is expected in such a demanding application.
See other Maintenance Minders articles here.