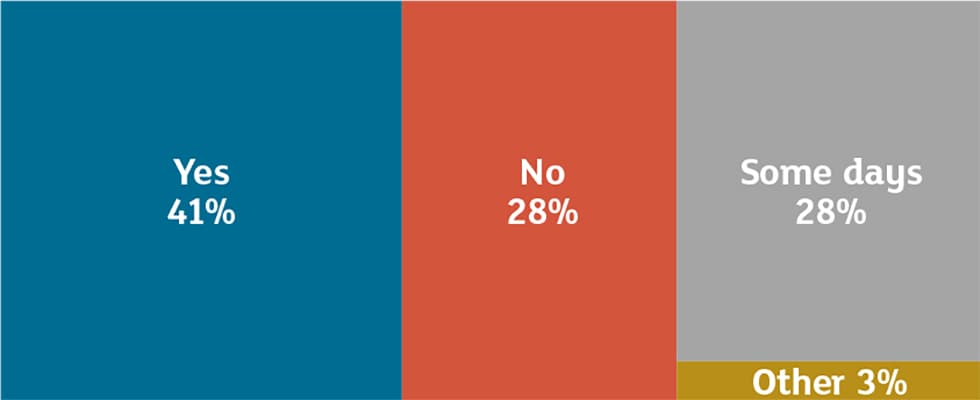
The 2021 Pumps & Systems Workforce Survey was deployed at the end of April, just as vaccinations to adults were fully opened across much of the United States. Meanwhile, COVID-19 infections were surging at a staggering rate in India.
While much of the data retrieved from this year’s survey centered around workplace information, the editors at Pumps & Systems wanted to know how much of the pumps industry’s everyday work life was still impacted by the pandemic. Not surprisingly, 41% of the 181 respondents said they are still continuing to work at home, while 28% said they are working from home only some days of the week. The pandemic continues to affect work habits such as travel, which some respondents said is still limited. Other impacted habits include in-person training and networking opportunities, and of course enhanced safety protocols and rigorous disinfection of premises. Some noted that the supply chain has been affected and some projects have stopped.
Aside from the continuing challenges of the pandemic, each year the survey results show that a top issue facing the pumps industry is hiring qualified employees. This year, 36% of respondents said it is somewhat difficult to find qualified workers, while 31% said it is very difficult. With approximately 36% of respondents losing coworkers to retirement this year, finding competent replacements is dire.
The survey results show that companies are finding ways to retain institutional knowledge, through “comprehensive succession planning,” paying retirees as mentors or consultants, enlisting senior professionals to lead training seminars and scheduling employees to work in parallel shifts for training. One respondent said, “My former company did nothing to retain institutional knowledge. They are now hiring former employees on a consulting basis to fill the knowledge void.”
This year, most respondents were engineering or maintenance and operations professionals. Respondents represented engineering contracting and design, oil and gas, wastewater treatment, chemical processing, power generation, and other industries such as HVAC, pulp and paper, mining, construction and more.
Roughly 25% of those who responded have been in the industry for 21 to 30 years; 25% for 31 to 40 years; and 19% for 11 to 20 years. Just under 24% had been with their current employer for three years or less, and 17% had been with their current employer for 21 to 30 years.
The number of respondents who make more than $165,000 per year stayed the same this year at just over 11%. There was an increase of 1 percentage point of those who make under $50,000 a year to 24%. About 13% of respondents said they make $50,000 to $65,000 and $95,000 to $110,000, respectively.
Tuition reimbursement is holding steady, with survey respondents this year saying 48% have this benefit available through their company. About 52% also have an internship or apprenticeship program available. Respondents were asked to select all answers that apply concerning training, and 79% said in-house training is made available, 52% are allowed time off for training, and 49% received reimbursement for online training classes.
For a look at survey results from previous years, visit www.pumpsandsystems.com/workforcesurvey.
Workforce Overview
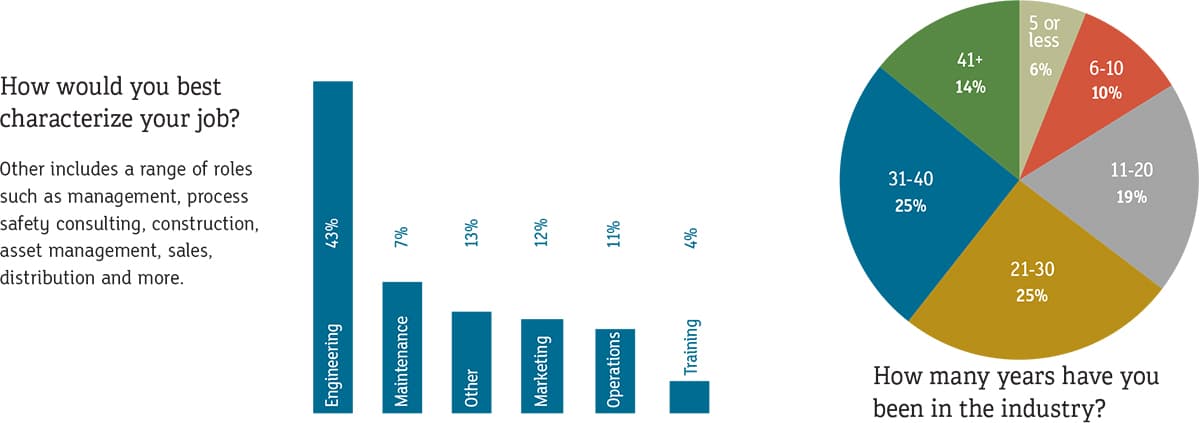
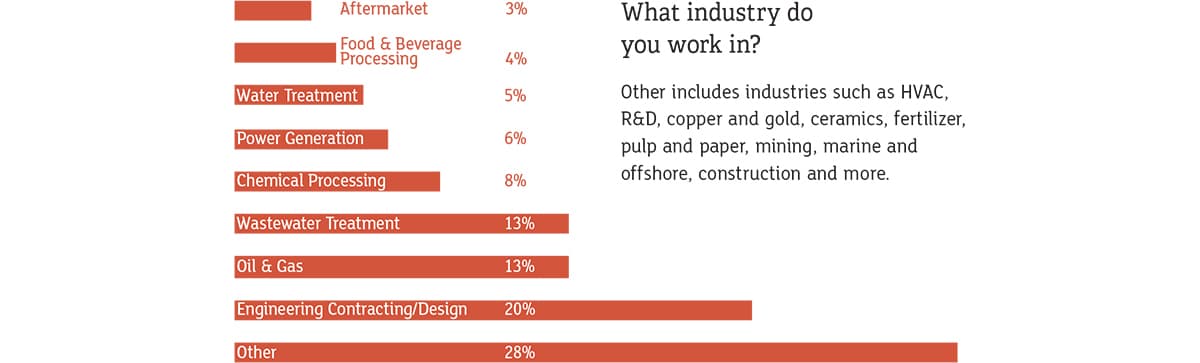
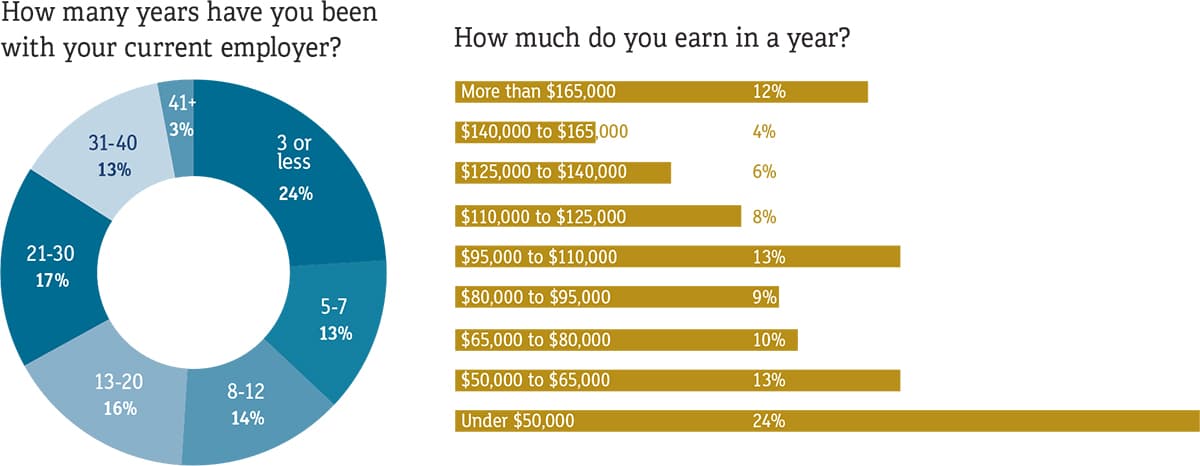
Workforce Development

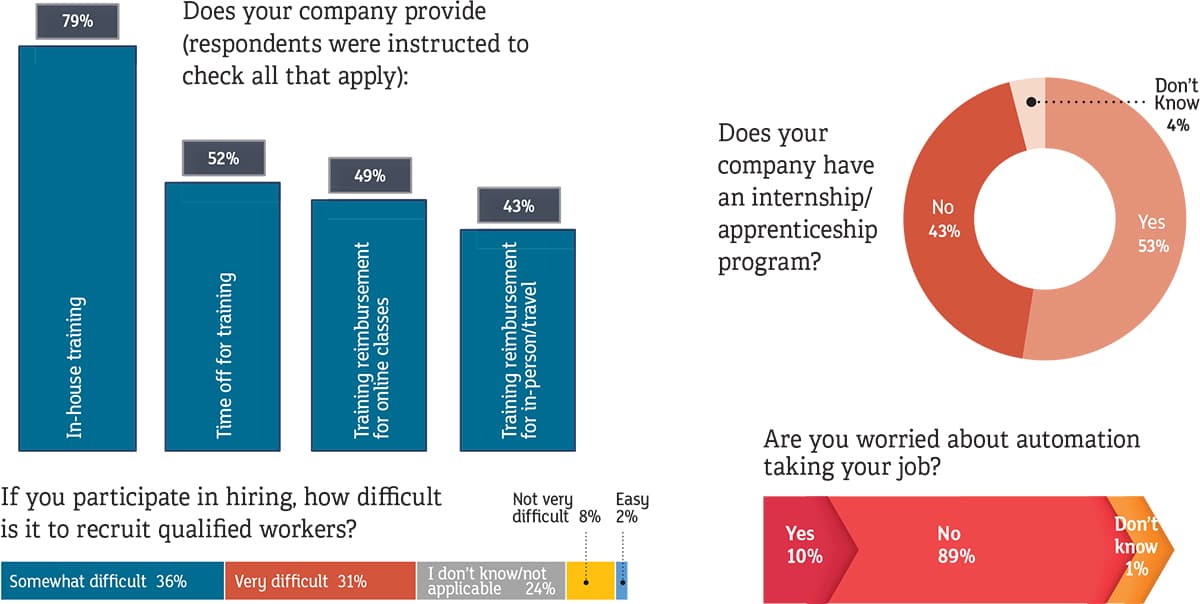
What is your company doing to retain institutional knowledge as employees retire?
Of the 133 respondents who answered this question, 53 said “nothing” or “not much.” Others said:
- Training with senior employees.
- The company has embarked on comprehensive succession planning.
- Mentorship of more junior associates.
- Senior people work closely with junior-level people for transfer of knowledge. Also, senior people do training seminars for the whole department.
- Using support from retired engineers.
- Operations and maintenance (O&M) documentation.
- Making them [retirees] consultants.
- I am an independent engineer. My former company did nothing to retain institutional knowledge. They are now hiring former employees on a consulting basis to fill the knowledge void. Purely next quarter mentality.
- Succession planning, employee development and having some time overlap (about six months to a year) between the new hire and the one who is going to retire.
- Apprenticeships and in-house training.
How has the coronavirus changed the way your company does business?
- Working from home became normal now.
- Most of the business is being done online. Direct contact with suppliers/contractors has been discouraged.
- Shift start times offset to reduce interactions.
- Few to no in-person visits at first. Now, facilities are allowing visitors in with precautions. It also pushed us to implement a remote, real-time troubleshooting system to help end users and other customers.
- Meetings have gone more virtual than before. Some face to face as necessary. It’s seriously affected my client’s ability to meet new customers for marketing of new products in development.
- Helped facilitate more automation and paperless processes.
- Main impacts have been market-driven, price of oil, demand outlooks, and how our customers are reacting to the suppressed global economy and trade status.
- We no longer have in-plant training for our customers/vendors.
- Remote customer support has become extremely important. Our factories have created programs to all our customers to witness factory acceptance tests remotely. Our field engineering teams have created remote commissioning protocols.
- There has been no change in how maintenance performs their tasks.
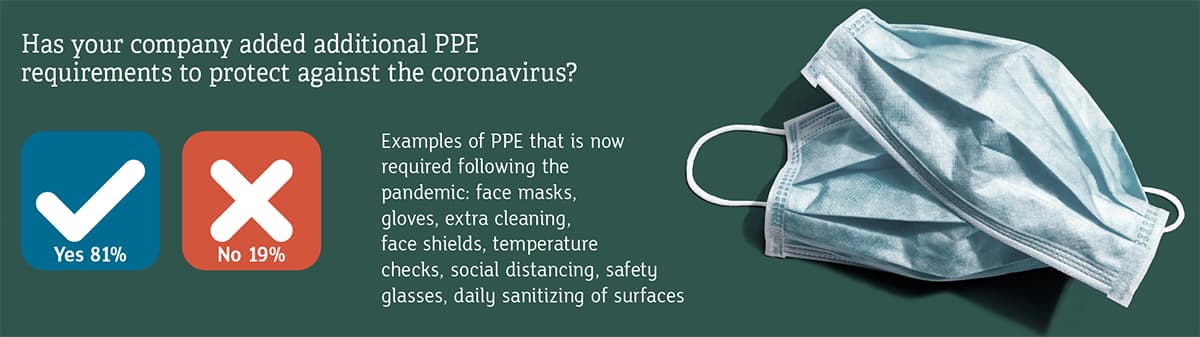
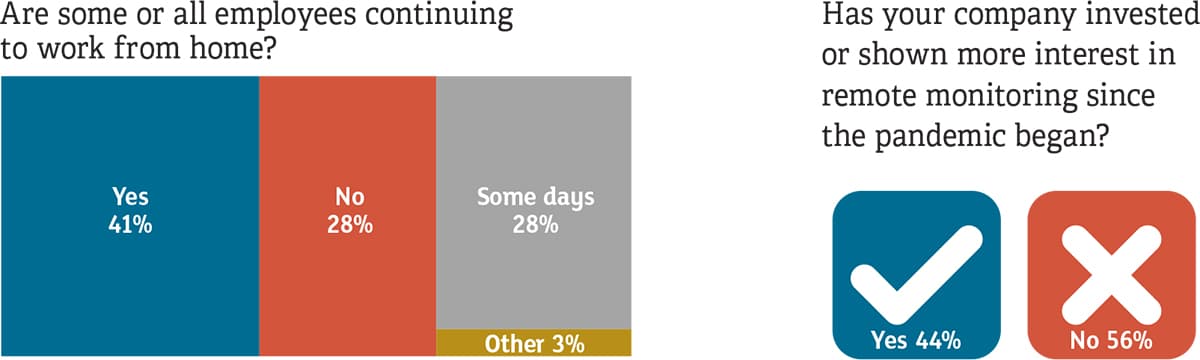