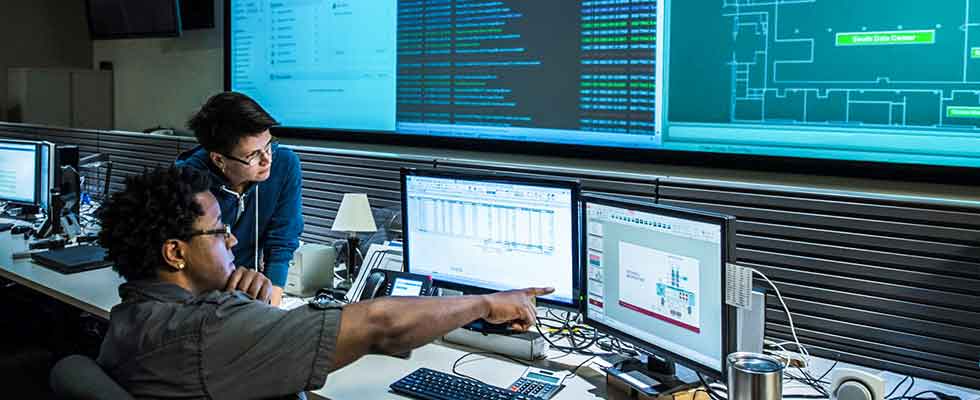
Many industrial companies face challenges that include aging generating assets, a growing knowledge gap, changing generation profile and utilization, and the growing need for transparency with regulatory agencies. A key to meeting these challenges is the design and standardization of an asset management process that optimizes maintenance strategies with a focus on improving work management, reliability, advanced technology, information management and asset planning. In asset-intensive industries, asset management is moving from simple maintenance to a business operation’s core competency.
This points to the rising need for risk-based maintenance, the need to maximize economic return on assets, and the increasing adoption of cloud-based applications to support global business.
Energy and utility companies have been challenged repeatedly by changes brought on by globalization and new environmental policies. Among these companies, operational excellence means getting more from the assets that serve their customers.
Consider these seven strategies that companies can employ to ensure their assets keep running to minimize disruption in operations.
1. Gather Data & Correlate It
Multiple systems of machine data, alarms and alerts can create a chaotic environment. The inability to create a single view of time-based data means that operations must manually attempt to understand dependencies and downstream impacts. The ability to gather all the data into one secured environment for correlation and management, specifically designed for machine data analytics, is the first step in optimizing control of a user's operating environment.
Asset management solutions can collect data across operating assets and environments, with self-service visualizations that provide a window into key performance indicators, asset relationships, and data analysis as well as other data sources, like work order history and weather.
2. Filter Out the Noise
Projections for autonomously connected industrial endpoints are only set to grow as the industry continues to automate. The value of data collected from these connections depends on systems that can identify key events, correlate alerts and alarms, and grant operators a view into actions that are of primary importance.
Alarm management has been part of plant operations for years. However, filtering out false positives and understanding priorities in an automated way has been a challenge. Analytics (descriptive, diagnostic, predictive and prescriptive) are now core elements of asset management systems, where individual asset sensor data as well as relationships between multiple asset information can be examined.
Analytics are employed to identify which alerts are likely to be critical, guiding operations staff with action prioritization. Using this data, sophisticated algorithms can filter out random variation and key in on critical issues.
3. Get a Bird’s-Eye View With a Zoom Lens
Traditional operations consist of multiple systems, each designed to measure and monitor singular machines or small groups of equipment. Asset management solutions can provide the ability to consolidate and provide that “single pane of glass” that operations management and staff need to see how operations are performing—holistically—across the plant and across multiple plants.
The truth is that both are required: the ability to drill down to each piece of equipment, but also to understand how an issue will influence the overall health and production output of the environment.
Asset management solutions are designed to provide this level of visibility, with understanding of individual assets as well as interdependencies between assets and workflows. With case management combined with decision analytics, operators can assess their environments at the portfolio, plant, asset class and equipment layers, allowing them to drill down to meet their immediate needs.
4. Enable Mobility Anytime, Anywhere
Modern industrial companies must optimize for mobile form factors (smartphone, tablet, etc.) to provide the most effective workflow in an operating environment. Mobile workers need to be able to measure performance and input data directly into their systems. Applications must allow a mobile worker to be “in the facility” around all equipment, across the plant.
The benefit of this configuration is that issues with the equipment can be addressed quickly through maintenance data captured by the system in real time, reducing incidents of lost data and errors that can occur when manual paper processes are used.
In addition, the current COVID-19 pandemic situation is making it important for power generation companies to enable remote operations solutions to ensure worker safety and operations continuity with secure remote/mobile operator controls.
These solutions ensure operational reliability to leverage worker location flexibility, allow operators to cope with reduced staff by using centralized remote expertise to augment essential local staffing, and provide the ability to act with urgency as needed.
5. Proactively Respond Before Incidents Occur
The results of unplanned downtime can be severe for every industrial company, with real bottom-line impacts. Predictive maintenance uses machine data and analytics to understand when components are likely to fail. Proactive measures can then be taken to order new parts and schedule maintenance during off-production peak times, providing longer windows of continuous operation.
This also has positive impacts on workforce efficiencies, emissions controls (fewer startup emissions) and asset life extension for improved capital management. Asset performance management software solutions must leverage analytics to identify assets that are likely to fail, the root cause of the failure, and the priority of impending events.
These solutions can perform automatically, continuously and relentlessly—24 hours a day—for optimized or for the most reliable asset operation under the existing conditions.
6. Improve Your Safety Profile
There is always a need to create safer work environments by reducing the number of emergency incidents and creating more organized and scheduled maintenance that drive improved safety key performance indicators (KPIs).
Whenever an unexpected failure occurs in an operating environment, there is a level of uncertainty and risk. Risk can come in the form of worker exposure to toxic materials, electrical components and combustible elements.
It also comes in the form of vehicle accidents or environmental hazards that put workers and the public in danger.
Following predetermined procedures proven to reduce safety and environmental hazards results in fewer incidents overall. Capturing responses and actions and then leveraging process-based analytics can inform safer responses in the future.
7. Reduce Dependence on Communal Knowledge
Operator response is often based on an individual’s historic knowledge of an asset’s idiosyncrasies rather than a systematic approach. This situation is acceptable only if that operator remains working in the same capacity. What happens as employees retire and that communal knowledge is lost?
Leveraging machine data collected and correlated in a common repository provides the basis for leveraging prescriptive analytics to understand operator responses in an automated way. This data store is the basis of a knowledge center that can support a “recommendation engine,” finely tuned to provide the best response results. Over time, common patterns emerge, and best practices are identified that become part of recommended operator responses. The result is greater consistency and automation for incident management and response across all employees and functional teams.
The challenges of aging generating assets, knowledge gaps, changing generation profiles and increasing transparency demands by regulatory agencies are real.
Using an asset management approach with digital solutions focused on asset management practices can help to optimize maintenance strategies, provide deeper insights of assets, systems and processes, and can help to address these challenges in ways that can optimize plant operations and increase asset availability while mitigating the risks of business evolutions.