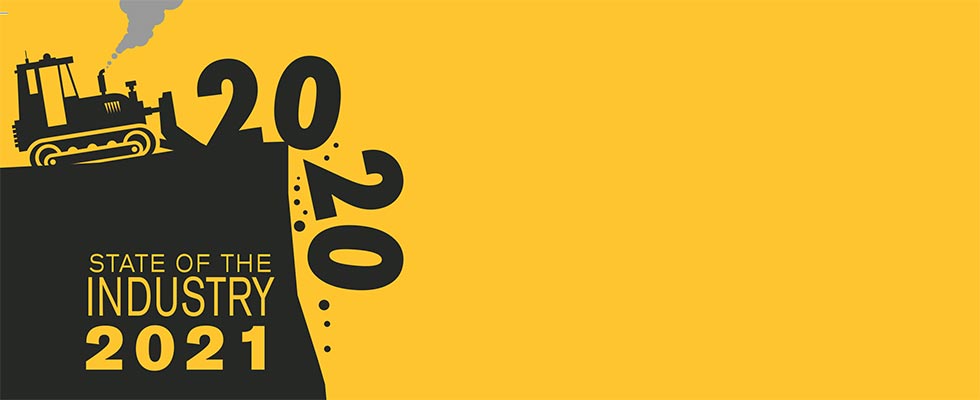
If you’re reading this in January 2021, congratulations! You made it through one of the most trying years since the Great Depression. I trust you are as hopeful as I am to move forward with 2021 and take advantage of the lessons learned in 2020.
One of the most used phrases in 2020 was “remote work” (yes, I know, “you’re muted” was another). The COVID-19 pandemic forced organizations to keep employees safe by physically distancing on-site or having them work remotely. Of course, countless businesses were forced to shut down, too, at least temporarily.
Among the things we’ve learned about remote work:
- Thanks to cloud-based computing and meeting tools such as Zoom and Microsoft Teams, many organizations stayed productive, even if sales took a hit. When required to do things differently to get our work done, many of us found that we could.
- The office environment and commercial real estate may be impacted for years to come because of the above. Even after we return to some state of normalcy, millions of people will continue working from home in 2021 and beyond.
Lessons For Maintenance Pros
For those in my profession, maintenance and reliability, 2020 was a bit more complicated. Maintaining previous asset service levels was challenging and not always possible. Maintenance teams at a sizable percentage of organizations in North America (which may be up to half) lacked the tools to effectively keep machines and equipment in peak condition with people working remotely.
My company develops cloud-based technologies to enable remote condition monitoring. Our solutions are built to help get through a pandemic, though we’d never thought of it in those terms. We’ve been doing it because, pandemic or not, leveraging the cloud and the industrial internet of things (IIoT) is the best way to bring maintenance and reliability into Industry 4.0 and beyond.
So, while 2020 set our profession, our industry and our economy back considerably, it did advance our argument that the digitalization of maintenance technologies is the right move for any company with assets to maintain. We say this with all due respect—it is certainly not the type of year we wanted to see.
Keeping this in mind, here are other things many of us learned in 2020:
1. Most asset maintenance doesn’t stop, even in a pandemic.
To keep our economy going and our homes and businesses juiced with electricity, some things have to keep running. Think power grids, oil rigs, nuclear sites, data centers and the like. Think machines and companies of all sizes struggling to stay open. Many did that in 2020, especially those with the most advanced maintenance tools and systems.
2. But, overall maintenance productivity was in decline.
In a mid-June 2020 webinar, we asked the 260 attendees from companies of all sizes, “Based on how it was before COVID-19, how effective is your business today?” More than 35% responded “at least 20% less productive,” and another 31% said “slightly less productive” (another 26% said “about the same” and 8% said “actually doing better”). Granted, this was mid-year, but it was representative of 2020 as a whole. Maintenance productivity declined for most organizations, which means many machines were not as well maintained as they would be in normal years. Many teams were forced to react to equipment problems rather than take proactive or predictive steps, and many technicians were overwhelmed and not always available to complete maintenance tasks.
3. Interest in remote monitoring technologies surged.
Legacy maintenance systems are paper-based and generally involve manual inspections of asset conditions as well as manual data entry into spreadsheets or computerized systems. Today’s advanced systems feature sensors, cloud-based connecting software, interactive mapping capabilities, and computerized maintenance management system (CMMS) or enterprise asset management (EAM) software. Some organizations are doing piecemeal updates to jump-start the move away from legacy systems, but these do not connect all the data sources.
The pandemic made clear the advantages of investing in a remote system for 24/7 monitoring—fewer people are required to maintain assets from inside the plant. Some monitoring and scheduling of work orders can be done from home. We saw lots of light bulbs turned on in people’s minds about this in 2020.
In a May webinar, more than 42% of 340 attendees said they had begun to plan for increasing the digitalization of their systems. Another 39% said they were lobbying to expand their maintenance technology budgets.
4. But, adoption grew slowly.
The pandemic certainly sabotaged technology budgets for companies not named Amazon, Microsoft, Google and Facebook. While inquiries and fact-finding soared, the funding wasn’t yet behind it. Many were experiencing downturns; others were cautiously awaiting the end to a global crisis that never really came. Still, others wanted immediate answers to their questions about ROI.
As manufacturers and others accelerated planning but not spending, those of us on the supply side spent months in a “develop-and-wait” holding pattern. Developing and partnering are efforts that we believe will pay off in 2021. Ultimately, the pandemic put everything in fast-forward, except the deal-signing.
5. Customers want complete and connected solutions.
Technology upgrades that were piecemeal, often involving a single piece of hardware or software application, have been common. In 2020, more companies inquired about full-on solutions, which makes sense because remote condition monitoring doesn’t work effectively without cloud-based connectivity. The pandemic has enabled us to work together to take the complexity out of developing end-to-end solutions. Yes, partnerships and connectivity are the order of the day.
6. They want advanced systems for more than just critical assets.
As cloud-based and IIoT platform solutions have come down in price, companies have begun moving toward outfitting more of their assets with advanced systems—not just the most critical 10% to 20% of machinery. The ability to incorporate flexible cloud offerings (public, private, or hybrid, which is an especially popular combination) has been a factor in influencing potential customers to roll out advanced solutions more broadly.
7. A technology explosion in 2021?
There’s a lot of pent-up demand. And companies are mindful that pandemic-like disasters may come around again in future years. But the downturn has hit many hard. Expect a ramp-up period where businesses remain cautious until the current crisis recedes, and we begin to move forward in a positive direction. All things considered, I do see 2021 potentially being the year of technology. We could be on the cusp of mass deployment.
8. Technology adoption means more maintenance jobs, not fewer.
Traditional maintenance jobs have been and will continue to diminish as fewer people will be needed inside manufacturing plants and other maintenance facilities.
But I see the requirements for data integration, data analysis, software account management, data center management, robotics maintenance, and even workplace sanitization growing. I also see more maintenance jobs ahead. The office and plant environment will change, but the jobs should increase.