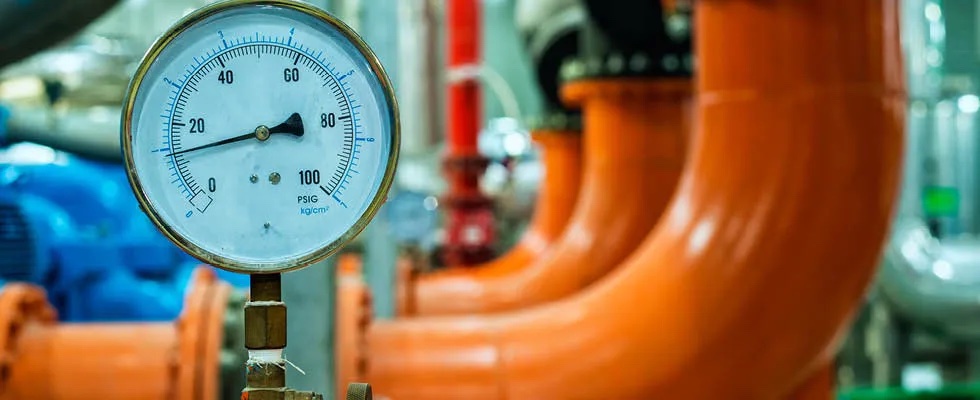
Pressure switches are important components, and accurate and reliable pressure measurements are key to ensuring a safe and efficient process. An incorrectly specified pressure switch could lead to actuation errors, damaged equipment, worker injury or other dangerous issues. How can a user know if they have the right pressure switch and what factors should they consider if they need a new one?
What Makes a Quality Switch?
Over 50% of pressure switch applications require the switch to be used to provide safety, whether it be to start or stop a device or to send an alarm signal to the user. Thus, picking the proper pressure switch for an application is critical.
There are many considerations when selecting the best pressure switch for an application, including the style of switch, wetted materials, housing construction, setpoint requirements, application pressures (working and maximum) and whether any approvals are required. Another important attribute of a pressure switch is the accuracy of the setpoint. Accuracy is also known as the repeatability of the switch, or the ability of the switch to provide the same setpoint time after time.
Different styles of pressure switches have all sorts of different accuracies. Electronic switches can have very good accuracies, while some basic switch designs can have very poor accuracy specifications.
Make sure the switch is manufactured by a trustworthy organization using quality manufacturing and engineering practices. The switch should be built and calibrated to industry standards for accuracy and reliability. Remember that pressure switches are calibrated sensors that may require recalibration over time based on the application.
Price can also be a consideration. Users can find low-cost switches using simpler designs and low-cost materials (e.g., acrylonitrile butadiene styrene [ABS] plastic) and switches that are higher cost but can provide better accuracy, reliability and safety. It is vital to understand the requirements of the application to pick the best switch. Here are more considerations when choosing a pressure switch:
1. Identify the standard operating pressure along with the maximum possible pressure of the application.
Users must make sure the pressure switch can be safely used in their application. Choose a switch that is ranged to handle not only the normal operating pressure of the application, but also any pressure spikes it may encounter.
2. Determine if the required setpoint can be achieved by the switch.
Regardless of whether users choose a mechanical or electronic pressure switch, there are limitations as to what setpoints can be achieved that are directly tied to the specific range of the switch. For example, with mechanical pressure switches, the setpoint range of the switch is often limited by the speed and travel of the actuator assembly, meaning the switch cannot provide setpoints in the lower 10% to 15% of the range. Electronic switches can provide setpoints almost anywhere in the range of the switch. Users should also determine if they need single or dual setpoints. Having two setpoints can be useful for having two separate alarms.
3. Consider the compatibility of process fittings and/or other wetted materials such as diaphragms and pistons/O-rings.
Be sure to check the compatibility between the process media and the wetted materials of the switch. Incompatibility can cause corrosion issues, safety concerns, leaching into the process media, etc.
4. Recognize any high temperatures and compare them to the capability or specifications of the switch.
The datasheet typically lists the temperature specifications. As mentioned, using a switch beyond its stated temperature specifications can lead to setpoint drift, component issues and possible safety concerns.
5. Select a microswitch based upon the application’s electrical requirements.
The electrical ratings of the microswitch are guidelines of the voltages and currents that the switch can be used with to ensure the maximum cycle life. The listed ratings provided by microswitch suppliers are the voltages and currents tested by third-party independent test labs for the required cycle life. Keep in mind that microswitches are mechanical pass-through devices that send the supplied voltage and current to the load. This means the microswitch can be used with many voltages and currents but may see a reduction in the cycle life.
6. Identify what approvals the application requires.
This includes hazardous approvals such as explosion-proof, intrinsically safe, non-incendive/increased safety as well as industry-type approvals like boiler and steam limit control approvals. Determining if an application requires hazardous area approval and general-purpose/safety approvals dictate which switch can be used for these types of applications. These approvals are provided by independent and nationally recognized test laboratories.
7. Determine if the switch needs additional options.
Does the user require a factory setpoint, tags, oxygen cleaning, special materials for housing/enclosure, wall/pipe mounting brackets or specific certifications? One of the most common variations is to have the setpoint of the switch calibrated at the factory. This is known as factory set (XFS). Using this ensures switch accuracy when received by the user and adds to the ease of installation. Other options include material choices, special enclosures, National Association of Corrosion Engineers International (NACE) certification, metric labeling, pilot lights and much more.
8. Fixed or adjustable deadband.
The term deadband in pressure switches is the difference between the pressure at which the switch activates and the pressure at which the switch deactivates. Switches can have two different kinds of deadbands, fixed or adjustable. Switches with fixed deadbands have a deadband value that is determined by the mechanical properties of the switch. Items such as diaphragm material, the switching mechanism and the pressure range of the switch all influence this fixed value. Adjustable deadband switches have deadbands that can be adjusted or selected within a specific range to meet a user’s application requirements.
9. Using a switch indoors or outdoors.
The environment in which a pressure switch is used can impact its functionality. There are many challenges when using a switch outdoors, including temperature and weather effects. Users must also consider what ingress protection (IP) and National Electrical Manufacturer’s Association (NEMA) ratings they need to satisfy the location of their pressure switch.