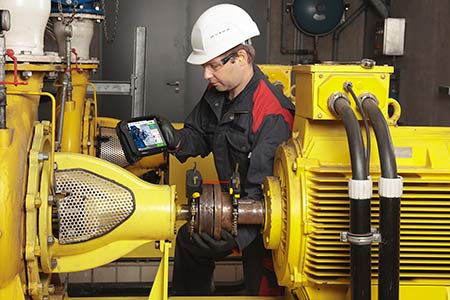
Maintenance professionals take a simplified view of machinery misalignment (pumps, motors, fans and more). There are two things they want to know: how to determine what is wrong and how to make it right.
This article will first discuss how to figure out what is wrong when rotating shafts are not running correctly, and then offer ways to correct the problem.
What Is Misalignment?
When two rotating shafts are not in line with one another—whether it be an offset or an angular gap at the coupling—the result is misalignment. Machinery misalignment is common in rotating machinery and is typically the root cause of machine failure.
Simply identifying misalignment issues in machinery such as motors, pumps, fans and blowers used to take considerable time and require a skilled technician. But today’s technology makes it quicker and easier to identify these issues. And once they are diagnosed, there are better tools available to tackle these challenges and achieve precise machinery alignment.
What Causes Misalignment?
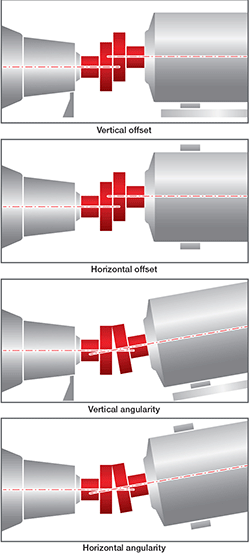
So, what causes rotating shafts to become misaligned in the first place? These are the primary triggers:
- settling of a baseplate resulting in soft foot
- shaft deformation caused by torsion during startup
- insufficient or poor-quality alignment measurements due to human error
- pipe strain that leads to parallel and angular misalignment
- a thermal expansion that can make one piece of equipment move proportionally to another
Misalignment of shaft centerlines can result in shaft wobbling and vibration, leading to seal damage and destroying the bearings and coupling. Identifying misalignment and the underlying causes is imperative if a machine is to reach its expected life.
4 Types of Misalignment
Experts generally agree on these four types of alignment:
- Vertical offset misalignment occurs when the two shafts to be aligned have centerlines parallel to each other, but the centerlines are offset vertically.
- Horizontal offset misalignment is similar to vertical offset misalignment but occurs in the horizontal plane.
- Vertical angle misalignment is an angular misalignment of two shafts in the vertical plane.
- Horizontal angle misalignment is similar to vertical angle misalignment but occurs in the horizontal plane.
The alignment issue is almost always a combination of both an angular and offset misalignment in both planes. This is a compound misalignment.
4 Ways to Detect Shaft Misalignment Issues
1. Diagnosis via laser shaft alignment system
Checking for shaft misalignment is often the first course of action when a machine starts having a problem. A laser shaft alignment system determines misalignment at the coupling and calculates the appropriate machine movement to be performed at its base. Laser systems provide real-time, accurate and precise measurements that tell users exactly when alignment is achieved.
Unlike the other three approaches described below, laser shaft alignment systems enable users to both diagnose and correct alignment issues.
Laser systems can be either dual- or single-laser types. However, a dual-laser alignment system is not as capable as a single-laser system. Often, technicians find it hard to maintain the line to the detector when correcting an angular misalignment. Unfortunately, as the measurement distance increases, so does the difficulty. As a result, technicians must restart measurements that require them to stop, loosen the feet, move the machine and retighten the feet—all with no guarantee that the detector will then be in range. With every repeat, process time increases and the potential for error grows.
A single-laser alignment system eliminates these dual-laser system problems. It more effectively addresses most shaft alignment challenges, from the straightforward to the complex—such as a vertical flanged machine with right-angle gearboxes. A single-laser system leverages two optical detector planes in a single sensor, eliminating the technician’s need to perform a rough alignment just to get both lasers on target.
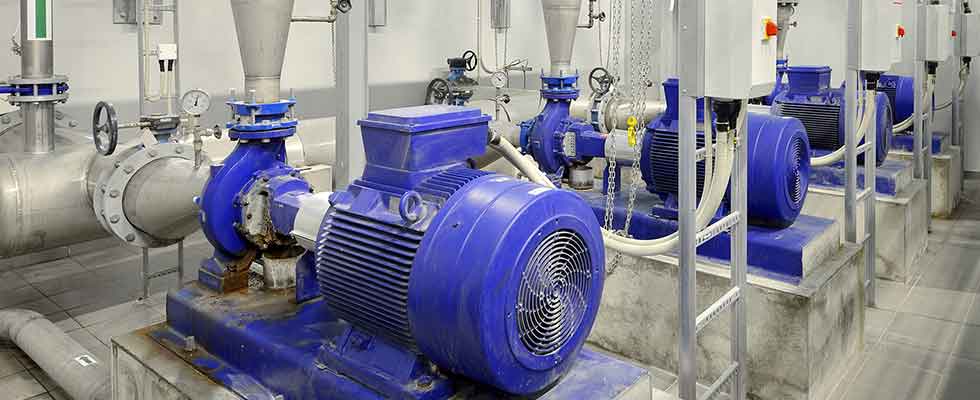
2. Vibration analysis
Because of the speed at which modern data collectors can process triaxial sensor signals, vibration monitoring and analysis are becoming more commonplace. Every machine has its normal vibration level, but there are instances when machine vibration increases or exceeds acceptable parameters.
Some of the reasons for vibration increases include looseness, resonance, unbalance and, of course, misalignment. Vibration is most often measured by using accelerometers, followed by proximity sensors or velocity transducers. Once these signals are acquired with a data collector and sensors, a vibration analyst can further diagnose the machine’s faults.
3. Thermography
Thermography is able to provide early detection of alignment issues by identifying abnormal hot spots. Misalignment can cause an increase in friction within a machine and the corresponding rise in temperature. A thermal imager detects and measures an object’s infrared energy and turns the infrared data into an electronic image showing its apparent surface temperature.
4. Oil analysis
When an abnormal condition or parameter is identified through oil analysis, immediate actions can be taken to identify the root cause or act on the emerging failure. Oil analysis can help detect misalignment by providing the general condition of an asset, oil and contaminants. Because oil analysis can be complicated, many organizations use specialty companies.
Misalignment causes many symptoms, along with severe machinery issues. Implementing a preventive maintenance routine to verify precise machinery alignment will save money and time. Keeping shafts aligned also improves energy efficiency, increases uptime and maximizes production output.
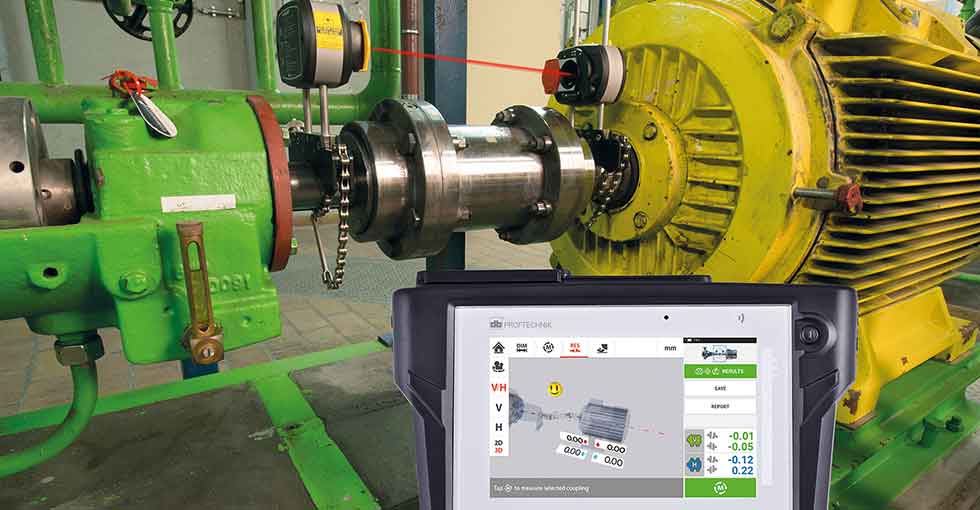
Laser Shaft Alignments to Correct Misalignment
Maintenance teams regularly face unique alignment challenges, from basic alignment jobs to more complex and challenging tasks. And, because today’s machines and their misalignment problems vary, teams require hardware and software alignment systems that can adapt to virtually any situation in the field. Teams also need tools that adjust to different team members’ experience and skill levels—especially as veteran employees move on or retire and newcomers assume their duties.
This flexibility is what they get with advanced laser shaft alignment systems containing software and other features that enable them to adapt to the situation, the asset and the user experience level. These systems maximize production time and minimize unplanned downtime without sacrificing ease of use. A laser alignment system with adaptive features eliminates human error while delivering new levels of accuracy and speed. Here are two components to seek out:
1. Single-laser technology. With a single-laser system, users have just one sensor and one laser to set up. Not only is this faster than with a dual-laser system, but it also eliminates the many frustrations and risks of inaccuracies that occur when working with two lasers firing in opposite directions. Single-laser technology enables rapid completion of alignment tasks and improves precision.
2. Intelligent software. The right software tools help maintenance teams by providing them with real-time, actionable intelligence and filtering out low-quality measurements. This software is situationally aware and delivered as work is being done. It dynamically reacts to everything involved in the alignment process and provides predictive intelligence to allow technicians to evaluate different possible courses of action before embarking on the time-consuming task of moving a machine.
By leveraging these two technologies, maintenance teams can deliver on the promise of adaptive alignment in all three critical areas common to every alignment task: the asset, the situation and the maintenance team.
- Adapting to the asset. Basic laser alignment systems are not engineered to support the broad range of critical rotating asset types and can be difficult to use with them. This deficiency makes for a costly and time-consuming problem for plants that rely on those assets or specialized but standard asset configurations. When laser alignment systems support the broadest range of assets and configurations—as adaptive alignment systems do—they eliminate manual workarounds and inaccuracy problems that are common to nonadaptive systems.
- Adapting to the situation. Perhaps the most vital attribute of adaptive alignment is its ability to adjust to many different variables—including the degree of rotation angle, speed and evenness—all while delivering a smooth, rapid and accurate alignment experience. This enables technicians of all skill levels to take high-quality measurements by following the steps and tips displayed on a screen. The software evaluates many quality factors simultaneously in real time and provides instantaneous feedback. Included among those factors are common issues such as instant coupling backlash filtering and environmental vibration.
- Adapting to the team. The ideal alignment tool has the intelligence to discard many errors a technician may inadvertently make. It uses analytics in real time, removing the incorrect data. With basic laser alignment systems, both experienced and inexperienced technicians often obtain different results. So-called adaptive systems unlock team capacity; even if an inexperienced technician is doing the alignment, the system corrects common errors to enable the technician to obtain the same high-quality results as those of a more experienced engineer.
Read more Back to Basics articles by clicking here.