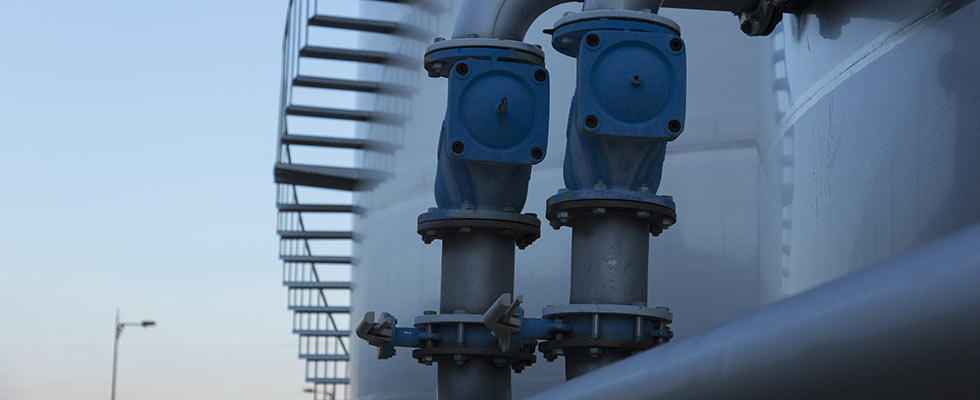
In the petroleum extraction and refinement processes, pumps are used to transfer product from one location to another, with many different methods used depending on the product type, density and volume. Most pumps use electric motors as the prime driving force to transfer fluids.
Monitoring the properties of the electrical power supplied to the pump will provide maintenance personnel with data that can be used to prevent failure of the pump as the equipment wears.
The pump is exposed to the surrounding environment and the transferred product itself, which are both potentially corrosive to the interior and exterior of the pump.
With the continued emergence of condition monitoring as a path toward predictive maintenance, and the industrial internet of things (IIoT) cloud storage for collected data, many processes are producing important information from a multitude of sources.
Vibration measuring sensors, temperature monitoring with standard thermocouples or resistance temperature detectors or infrared cameras, acoustic emission devices to detect the sound of equipment wearing down, and current and voltage measurement transducers are all proven approaches to spotting problems in the drive system before they become catastrophic failures.
While most of these approaches use sensing technologies that are mounted on or near the machines, current and voltage transducers can be mounted a great distance from the contaminates. Therefore, widely varying ambient temperatures may be seen at the equipment installation point in the regulated environment of a control center enclosure.
Using Sensors to Measure Electrical Properties
Single-phase or three-phase alternating current (AC) and direct current (DC) power all reflect the condition of the electrical system in the same manner.
Current increase over normal represents a mechanical problem.
A bearing may be failing, causing the drive motor to work harder to accomplish its task. The pump impeller may show wear from cavitation, making it more difficult to pass the transferred liquid through the pump volutes smoothly. Foreign material sucked into the pump can impede the movement of the impeller, inhibiting the free movement across a bearing surface or becoming entangled with a rotating shaft.
Overcurrent conditions are generally protected by circuit breakers, fuses or overload protection as part of the
contactor assembly and often by two or three of these options. These options will de-energize the pump in a certain amount of time depending on the magnitude of the overload.
A current-operated relay or switch can be used to trip an alarm as a warning when current rises over the set point, or to trigger a sequence through logic to shut the pump down. They also will react to overcurrent conditions faster than other overload protection methods when the current increase is relatively low when compared to short circuit or locked rotor conditions.
Current decrease occurs:
- when a shaft coupling is loose or sheared
- when the pump discharge is open or leaking
- when the intake is partially or completely blocked
Undercurrent conditions can be as damaging as overcurrent but require sensors that are not required by the National Electrical Code or in most project specifications. Using a current sensing relay or switch with single or multiple set points, installed over a lead powering the pump drive system, and adjusted so a contact (often solid state) closes (or opens) when the current draw of the pump exceeds a limit or set point.
The contact can be adjusted so that it is in the tripped condition while the pump is running normally and will reset to trigger an alarm or open the circuit to the contactor operating coil when current falls below this trip point.
More conventional control approaches like mechanical interlocks mounted on contactors are not enough to detect when motors are operating but not securely connected to the pump drive shaft. They will show when the contactor is closed but not that the motor is drawing normal running current. The motor will be spinning away while the pump is not, but at a lower-than-normal amperage.
Voltage sensitive relays are designed to detect phase loss, voltage spikes and sags. Energizing a motor with lower than the voltage on the nameplate is a primary cause of pump failure as this causes the current to increase. An undervoltage event to 90% of nameplate voltage will cause an increase in current of about 11%. This type of detector should spot a phase loss by tripping an output if the voltage imbalance between the three phases exceeds 5%.
A three-phase motor will generate up to 92% of the normal voltage when a phase is lost, in turn causing overheating due to the eddy current in the windings. A phase loss will also raise the current in the connected phases by 150%. An imbalance of 3% of design voltage will cause excessive heating in the motor windings, which is covered under National Electrical Manufacturers Association (NEMA) standards. But a 5% imbalance will cause 50% overheating and an imbalance of 7% causes overheating by 98%.
Current sensors will react to changes in the load faster than bimetallic or eutectic overload elements; so, they are often designed with time delays to bypass starting current inrush or momentary overload conditions.
Underload conditions might be detected by monitoring the speed of a rotating shaft with optical sensors, although they are often difficult to mount and calibrate and usually subjected to adverse environmental conditions like dust, water and vibration. There would be a need to install several motion detectors at various locations on the equipment to obtain the information produced by one current relay.
Current sensors are mounted in the electrical control or distribution panel, protected from the outside world alongside contactors and circuit breakers or fuses. This eliminates the need for extra shielding of the sensors from adverse conditions such as volatile gases and moisture in the environment or chemical contaminants.
The output of an analog or digital transducer will provide constant data of the current used in each phase, and that data can be trended over time to spot over or undercurrent conditions as they become worse. Action can be taken in many cases before the problem causes a halt to production. Any breakdown is disruptive and it is optimal to plan for repairs to a pump system to be implemented during a planned shutdown.
Monitoring current, voltage and power is a minimally invasive approach to keeping pumps and associated equipment turning and working with fewer catastrophes.