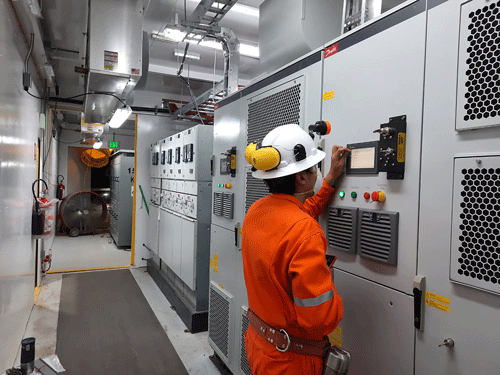
The topic of water management is always top of mind for any company affiliated with the mining sector. Underground mining operations require constant removal of water from the deepest parts of the mine. Ground water, runoff and seepage from nearby sources all contribute to this challenge. Pumps located deep within the mine can be subject to harsh environmental conditions. In addition, the water pumped from the mine typically cannot be discharged off-site in its current state. Auxiliary equipment is also required to purify or reuse this resource.
In regions where surface mining is more prevalent, the availability of freshwater resources is limited and may only be used for human consumption and not industrial applications.
For access to needed freshwater, mining companies often find it necessary to build and maintain desalination plants to purify nearby seawater for use in the plant.Often, the distance between the variable frequency drives (VFDs) and pumps can be long and present several challenges for end users. Common issues associated with long cable lengths can be excessive current draw, premature bearing failure and winding failures in pump motors. Many times, these issues can be resolved by installing output filtration on the drives, specifying inverter duty rated motors, engineering a sophisticated cabling with a grounding system for noise immunity and installing motor filtration and mitigation devices.
In addition to long cable lengths between the motor and drive, another challenge is that a robust power grid might not be available. Even in some of the largest cities in North America, a clean and strong electrical supply is not always accessible and can contribute to less-than-desirable reliability and performance from your drive system. Premature drive failures due to brownout conditions, transitions to generator power and back, power factor correction devices and excessive harmonic content produced by other devices can have an impact on the overall reliability of the drive system at the facility.
Having an intelligent drive solution that can help predict internal failures, correct for harmonics and alert owners of potential problems with the pumps can save mining companies millions of dollars in unexpected downtime. Partnering with a VFD supplier that can offer these types of drives and who has the level of expertise necessary to identify and design an electrical system that can withstand these variables is important.
Case Study
Faced with the challenge of pumping stagnant water from depths of more than 400 meters, the Cerro Los Gatos mine opted for medium-voltage variable speed pump control. Drives were delivered and installed in 14 weeks from factory acceptance test.
The Cerro Los Gatos Mine, the Esther Deposit and the Amapola Deposit are three silver-lead-zinc sites forming part of the 14 mineralized zones of the Los Gatos District, the center of the Mexican silver belt.
The Cerro Los Gatos Mine is the first commercially successful mine in the region. Concentrated material is sold in Mexico, to foundry facilities in Japan and to other locations through intermediaries. The annual production of the mine is about
9.2 million ounces of silver equivalent per year through the mine in stock. Cerro Los Gatos mine has one of the best total maintenance cost profiles according to the American Institute of Steel Construction (AISC) in the silver industry.
The mining industry operates 24/7, and this specific mine site includes several vertical shafts, which are connected and form a network of galleries below the surface of the basin, where flooding naturally forms a large underground reservoir. For the Cerro Los Gatos mine to maintain excavation and production, it is necessary to pump out the underground water. With stagnant water at more than 400 meters deep, the Cerro Los Gatos Mine decided to specify two air-cooled standalone 128 amps/4,160 volts medium voltage drives.
These drives were installed in Mexico, and the mine became one of the first in the country to implement a solution of this nature to deal with pumping water from great depth.
Installing an effective water pumping system became a multiphase project. Firstly, the diagnosis was made following on-site visits, then evaluation and selection of solutions commenced. Finally, the solution was installed and commissioned. Thanks to a collaborative approach, manufacturing time was only 14 weeks, a record time for projects of this magnitude.