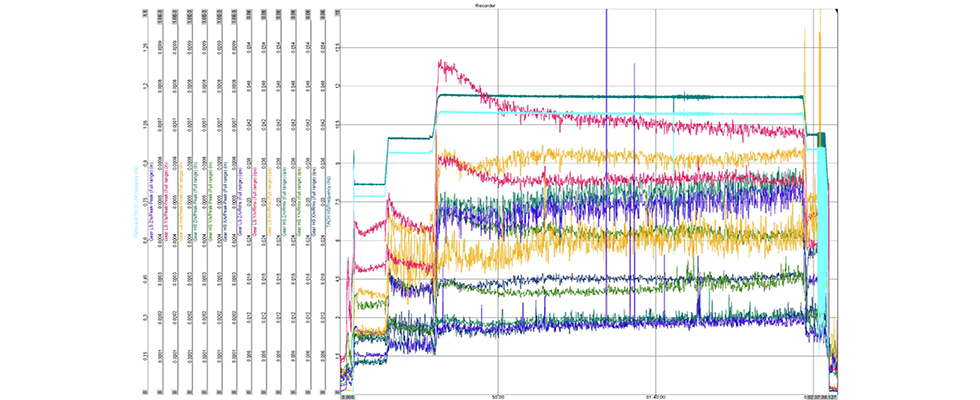
Wastewater pumping stations represent one of the most critical areas of public infrastructure in the U.S. They are an essential part of protecting public health and safety in communities across the nation. Modern wastewater infrastructure is a marvel of engineering, yet it faces a major dilemma—the equipment is often outdated and in dire need of replacement or repair.
A nationwide push for establishing water treatment plants in the 1960s and 1970s helped develop the system in existence today, but many of these plants are nearing or have exceeded their useful life span. According to the 2021 American Society of Civil Engineers (ASCE) Infrastructure Report Card, the average water piping network is 45 years old, with some dating back over a century. The pumps that power these systems face the same predicament. Furthermore, the federal funding boost that accelerated the creation of water infrastructure 50 years ago has declined and most of the financial burden for upkeep has been placed on states and municipalities.
The current condition of water infrastructure in the U.S. is being recognized as a major national issue concerning human and environmental health. While efforts are being made to focus government assistance on this need, political and other factors lead to uncertainties in scope and timing. In the meantime, plant operators and local governments must address immediate concerns of replacing and repairing aging equipment. Proper assessment of pump health is therefore more important than ever. Several advanced diagnostic methods are available to help identify the correct remedy for failing and underperforming pumps. When used correctly and diligently, these tools can keep costs at a minimum and reduce risks while ensuring vital pumps perform at the standards needed to continue protecting public health.
Trending Diagnostics & Predictive Maintenance
Trending diagnostic tools refer to continuous monitoring of conditions such as vibration, flow, pressure, speed and more. Advanced data acquisition software records more than 20 analog inputs, allowing a user to visualize the various data streams at once, making it much easier to detect anomalies and diagnose issues. Trending diagnostic monitoring can be a time- and cost-saving endeavor for pump owners, helping to identify the source of equipment problems without stopping operation or dismantling machinery.
In the case of vibration monitoring, the data software generates time waveform (TWF) and fast Fourier transform (FFT) outputs, which help determine failure modes. Several advanced analysis techniques for TWF and FFT data can be utilized to determine the cause of vibration issues. When viewing these results alongside other monitored conditions, operational deficiencies can be identified and transient events like startups, shutdowns or valve closures can be captured. Based on this multitude of information about a pump system, equipment can then be fine-tuned to optimize performance.
The accumulation of data over longer time periods also allows for analysis of historical trends and frequencies of issues. This assists greatly with the effort to pinpoint the source of a known issue, and it also enables predictive maintenance by helping to detect imminent malfunctions that may have otherwise gone unnoticed. Identifying and addressing equipment issues early can lead to significant cost and labor savings by reducing downtime.
Viewing Natural System Frequencies With Modal Analysis
Experimental modal analysis (EMA) is a valuable tool for measurement and analysis of modal properties of a pump system, such as damping and shape. EMA techniques aim to align an analytical model of a structure’s dynamics with measured data that reflects its actual behavior. The measured data comes in the form of frequency response functions (FRFs), allowing the natural frequencies of a system to be visualized. By examining relative movements and mode shapes, users can determine the ideal points where a structure can be stiffened to alter the natural frequencies. Targeted corrective action can lead to cost reduction and increased resolution speeds. Remediation based on EMA can prevent a catastrophic failure of a pump.
Vibration Modeling With Operating Deflection Shape
Operating deflection shape (ODS) is a modeling technique used to measure and visualize the vibrations of a pump system while it is operating. An animated 3D model highlights the amplitude and direction of vibration at various points on the pump. Often deployed following EMA, the ODS provides in-depth data on the actual vibration forcing function of the system and corresponding dynamic behavior. This visual portrayal of the movement of a system allows for quick and focused solutions to reduce vibration.
The ODS can also be used to identify the root cause of vibration issues. Through shape estimation of the pump equipment, foundation and piping, it can be determined if excessive vibration is caused by a structural defect with the pump or by external factors such as a poor foundation or misaligned piping. ODS can even assist with preventive maintenance efforts by monitoring pump vibration patterns over time to detect potential problems before they reach a critical stage. Overall, ODS modeling is extremely important in vibration analysis because of the depth and quantification of information generated. It can reveal not only the location of unwanted vibration, but also the amount and direction of the movement under normal operating conditions. This information is paramount to determining corrective measures to reduce vibration.
Motion Amplification Video
An alternative to ODS is the motion amplification video (MAV) technique. Using a high definition and high dynamic range camera with proper lighting, every pixel of the recorded video acts as an individual sensor, generating millions of data points. MAV offers an advantage over ODS through quick setup time, as the data is collected and analyzed in a matter of seconds.
An additional advantage of MAV is the ability to capture data over larger areas of the system, providing an extensive view of the asset. A single data capture can be used for multiple pumps, motors, piping networks and other large structures. Analysts can then fixate on particular problem areas seen in the video or pointed to by the data. The closer examination might use a higher frequency data collection or a different camera angle.
MAV can also offer a baseline set of data conveying the behavior of a pump during commissioning, allowing pump owners and the OEM to be aligned during installation. This initial data can then be used as a reference for future diagnosis of the pump’s health. MAV also enables analysis of areas in a pump system that cannot be accomplished through traditional vibration measurement methods. Small-bore piping vibration is typically not analyzed because of the large quantity of measurement points that would be required, but a complete system view through MAV can easily pinpoint areas in the piping where shaking is occurring. Mechanical seals can also be examined through MAV because of the procedure’s noncontact nature. Finally, the ability to see motion at specific frequencies supports the diagnosis of all failure modes of a pump system, such as misalignment and poor foundations.
A Pump Diagnosis Toolbox Can Reduce Costs & Risks
Lack of federal funding and the ever-increasing environmental and quality standards imposed on wastewater treatment plants are causing a strain on the local governments that manage these facilities. A comprehensive assessment of pump health can help explore all possibilities for rehabilitation before replacement is considered, helping to avoid unnecessary spending. A full suite of diagnostic tools can also allow users to employ predictive maintenance on their equipment, helping to reduce the risk of failures and catastrophic events, leading to additional cost savings.