Changing needs and requirements have caused pump technology to evolve.
IWAKI
09/02/2016
In the American National Standards Institute standard 7.0, the Hydraulic Institute defines controlled-volume metering pumps as “reciprocating positive displacement pumps typically used for the injection of chemical additives, proportional blending of multiple components, or metered transfer of a single liquid. These types of pumps are used in applications requiring highly accurate, repeatable and adjustable rate of flow.”
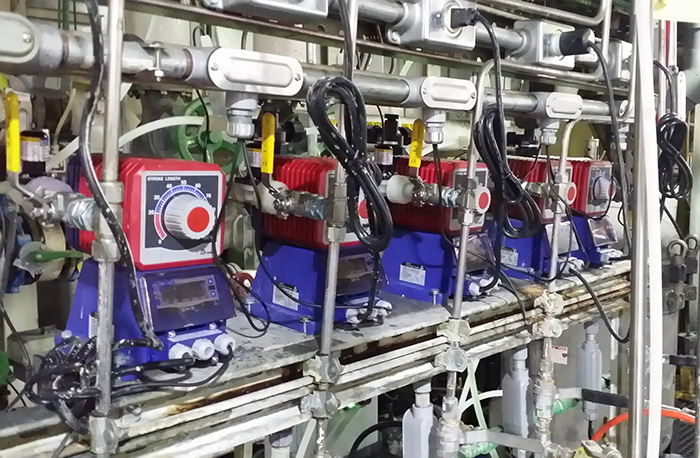
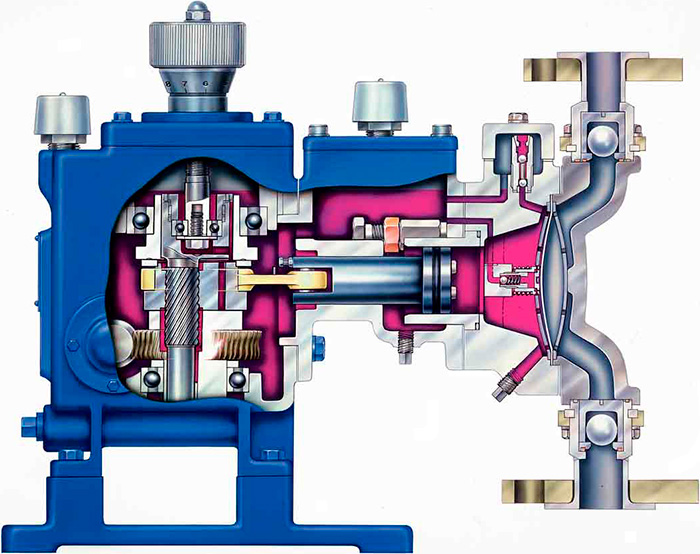
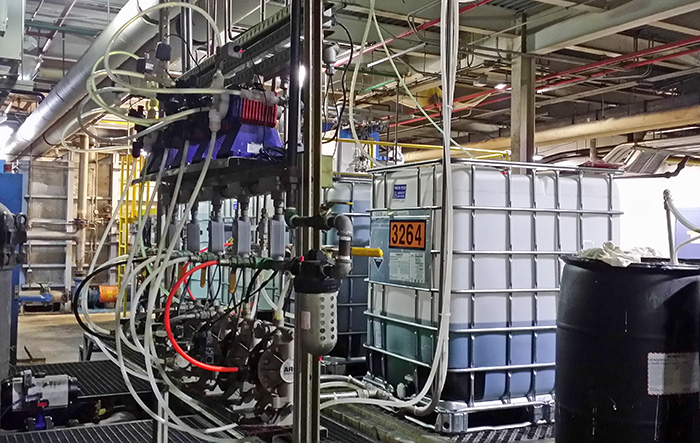
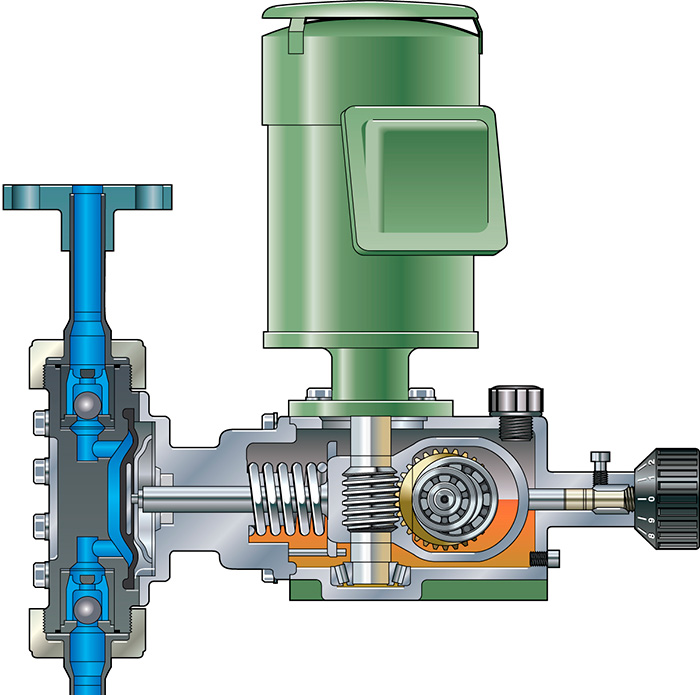
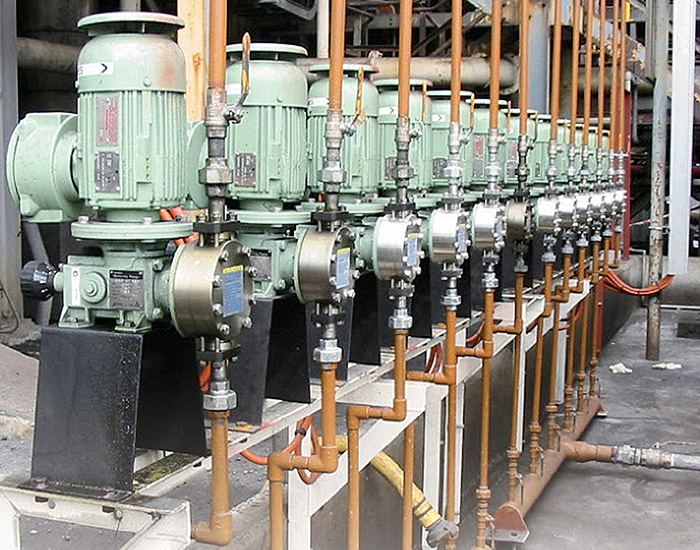