Plant operators rely on plant air pressures to maintain properly working equipment and systems. One of the most common problems affecting processing plants that use compressed air systems is the ability to maintain reliable air pressure throughout the distribution system. Undersized distribution piping may create insufficient air pressures, but more often the cause is flow restrictions in the distribution system such as filters, check valves and fittings, as well as flow meters and gauges. Leaks in the distribution system actually rank low as the common cause of pressure drop. Pressure drop is the loss or reduction of pressure from the compressor discharge to the actual point of use. The system will appear as though there is a lack of air pressure, but the real problem is pressure drop, which will cause excessive energy consumption. This article will explain the causes of pressure drop, a variety of solutions and ultimately how to eliminate costly downtime.
The Challenge
Unfortunately, the solution is not as easy as just cranking up the air pressure at the delivery point, as this will cause other issues such as leaks, excessive component wear and maintenance. Every one pound per square inch (PSI) of excess operating pressure increases air compressor power consumption by around 0.5 percent. As can be seen from the pressure drop formula, increasing the system pressure will actually increase the pressure drop (see Equation 1). Unregulated equipment on the system will increase demand and increase inefficiency of the system.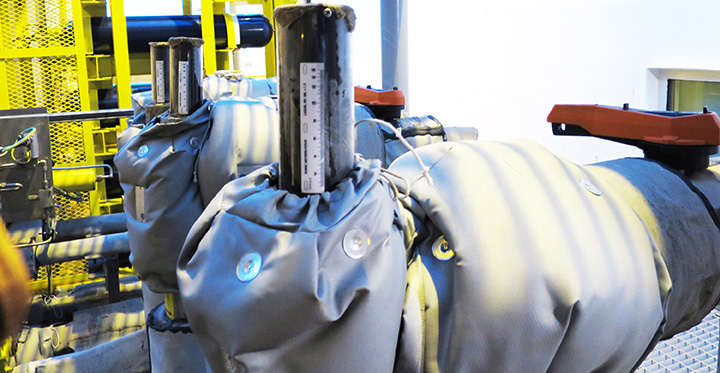
The Solution
Users can minimize pressure drop by selecting equipment such as filters, dryers, flow meters, air treatment equipment and instrumentation with the lowest amount of pressure drop. Additional ways to decrease pressure drop would be to maintain air filtering and air treatment to reduce moisture that can create corrosion and increase friction on the piping system. Also, users should reduce the distance the air travels through the distribution system so as to create the shortest runs possible to reduce loss. Select the correct pipe sizes and pipe material with an effort to avoid hoses or corrugated products that will reduce pressure. Sizing pipe is critical for efficiency with the goal of keeping air velocities in the distribution header under 20 to 30 feet per second. Increased velocities will increase pressure drop. The calculation for pressure drop is called the empirical formula (see Equation 1).dp = 7.57 q1.85 L104/(d5 p) Equation 1 Where: dp = the pressure drop measured in kilograms per square centimeter (kg/cm2) q = the air volume flow at atmospheric conditions measured in cubic meters per minute (m3/min) L = the length of pipe measured in meters (m) d = the inside diameter of pipe measured in millimeters (mm) p = initial absolute pressure in the system measured in (kg/cm2). This is the rating of the compressor, which gives the pressure expected at its outlet valve.
Another major influence to pressure drop has to do with the quality of the air flow. Air that flows in a swirling and turbulent path inside the pipe is called turbulent flow, which is the most inefficient flow condition. Air molecules spend so much energy bouncing off of pipe walls in all directions that they have less energy for moving down the pipe. The ideal flow condition is for the air molecules to all move in a direct path down the pipe together. This flow condition is called laminar flow. Turbulent and laminar flow can be calculated as well, using Equation 2 to determine the Reynolds number.
Re = ρvd/μ Equation 2 Where: Re = the Reynolds number ρ = the air density v = the mean velocity d = the diameter of the pipe μ = the dynamic viscosity
An efficient air flow system should have a Reynolds number of less than 2,300. If it is greater than 3,000, the air flow in the pipe will be turbulent, and corrections should be made.
Reliable Measurements
Making smart measurements of the compressed air system will reduce maintenance and energy cost and ensure proper operation for all equipment requiring consistent air delivery. Measurement equipment is inexpensive. Monitoring power use, air flow and air pressure is all that is required to ensure a properly working system. Other measurements like dew point and temperature can also help your system operate with better results. By measuring the air flow, pressure and energy use, users can generate a baseline of the system operation. Typical flow data in a compressed air system is measured in cubic feet per minute (CFM). By knowing the volume of air use, system pressure measured in pounds per square inch (PSI) and energy use measured in kilo-watt per hour (KWH), you can create a baseline of efficiency.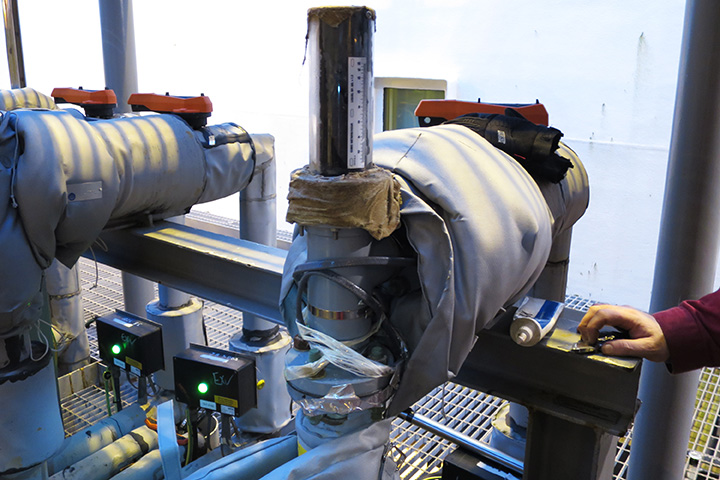
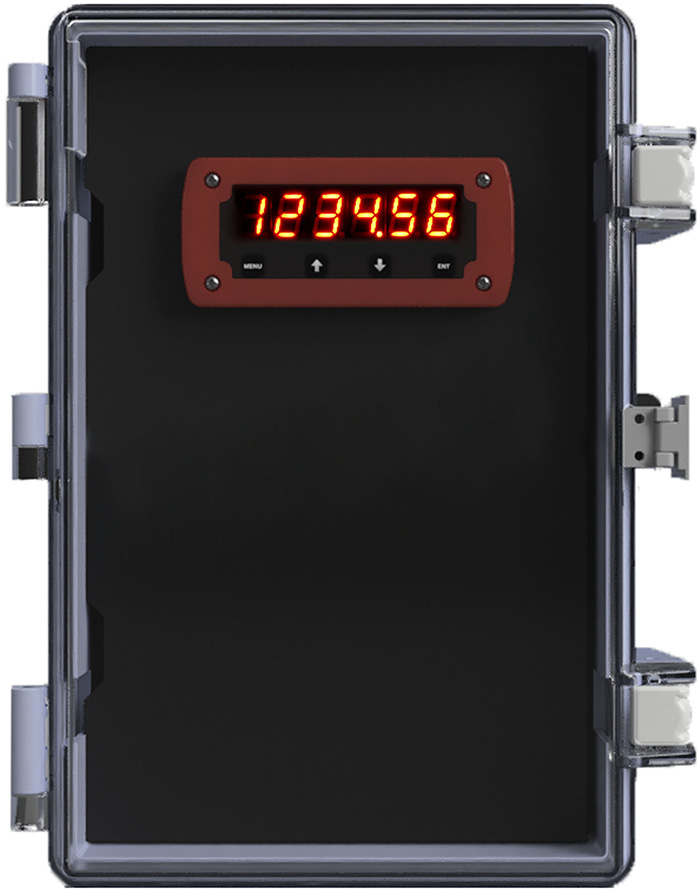