The vertical turbine pump is a trusted and proven workhorse pump found in industrial environments around the world. This pump design is continually improving operations in key global industries such as oil and gas, petrochemical, chemical, power, desalination and mining. Vertical pumps are designed to handle challenging applications and have a long legacy going back to their invention in the Los Angeles area more than one hundred years ago. The earliest vertical pumps were created for agricultural purposes. Now verticals are frequently selected as a strong solution to common challenges where low flow and high head pumps are required. Despite this, there can be a lack of understanding for design engineers, plant managers and site operators about when a vertical turbine pump is an optimal solution compared to traditional horizontal pumps.
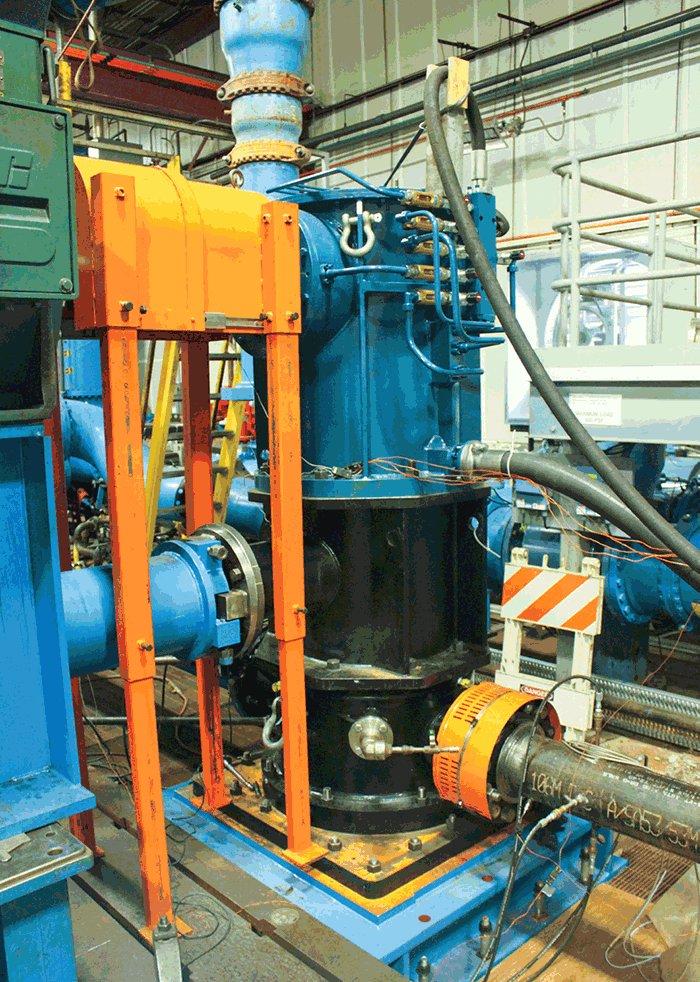
Considerations for a Vertical Pump
Scalability The length of a vertical pump can be extended going below ground as needed to ensure positive suction head. This flexible design offers a clear advantage with the ability to customize, essentially right sizing through stacking stages, or impellers, as needed. This feature allows for phasing and adjustment over time resulting in reduced operating costs because the pumps offer customizable installations suitable for any facility’s current and future needs. Size Vertical pumps can fit in tight spaces and require a much smaller footprint compared to their traditional horizontal pump cousins. This is an important consideration in environments with size limitations. Additionally, the base materials in a vertical pump can be upgraded, resulting in less wear and tear, decreasing plant downtime and maximizing the life of the pump. Efficiency Another challenge that verticals can bypass is priming because many of them are self-priming. This means that in a vertical, the operator does not need to remove air, vacuum the pump and fill it with liquid prior to starting operation of the pump. Instead a vertical pump starts without filling with liquid and will operate properly if a minimum level is achieved for the first stage impeller to start pumping. On verticals, it is possible to combine different hydraulic models to meet the specific conditions for the application. The flexibility enables customization that otherwise would not be possible. Safety, hydraulics & mechanics Vertical turbine pumps also tend to offer differences when it comes to safety, hydraulics and mechanics. Their features often become more important in tight spaces and hazardous environments typically found in many energy applications. When it comes to safety, verticals feature a submerged pump element and steeper head-flow curves. Another feature from vertical pumps is that the motor is on the top of the unit. It is easy to monitor and offers some protection since it is not as low to the ground as a horizontal pump. In flood zones, damage can potentially be averted due to the pump motor being elevated high enough above the ground. Vertical turbine pump hydraulics offer increased flexibility across a range of factors: an ability to handle lowest net positive suction head available (NPSHa), pressure by staging, broad specific speed (Ns) range and eliminating the need to prime. In certain instances, horizontal pumps might not have enough pressure at the suction port from the system to prevent cavitation. The vertical design eliminates the need to ensure that the NPSH liquid pressure versus liquid vapor pressure is adequate.Applications Where a Vertical Pump is a Better Fit
Tight spaces and size requirements Horizontals can be bulky and heavy. Due to the entire pump being above ground and a horizontal footprint, a horizontal pump sometimes cannot meet strict foot print and weight requirements. Also, horizontal pumps are limited to handle challenging pressure and low flow applications. Vertical pumps can often meet the requirement for smaller, more compact pump designs that enable maximizing floor space and make it easier to interchange pump components. On a vertical pump, it is possible to change the complete pump hydraulics without modifying your nozzle location. Pump operators can sometimes interchange in horizontal pumps, but there are often challenges in matching the nozzle to the existing piping location and drilled down bolts on the baseplate. The vertical pump’s lower portion, or bowl assembly, is the pumping element and can interchange without moving the location of the nozzles. On a horizontal, it’s the pump itself within the casing, if it needs to be moved then you must also accommodate the piping to match the new location or exact height with the new piping bolts. In contrast, many of today’s most advanced vertical turbine pump designs are compact, vertically suspended, with radial impellers, demonstrating an ability to handle multi-stage low flows and high-heads. The radial type impellers applicable for low flows and high heads are commonly needed in the petrochemical industry including light hydrocarbons, refining, production, storage and distribution of crude oil. The verticals can stack up many number of stages to make high heads as needed. For example, an operator seeking high pressures with volumes ranging from 30 gallons per minute (gpm) to 2,800 gpm and high heads to 4,500 feet or more can achieve this with a vertical multi-stage low-flow, high-head pump. The latest vertical turbine pump technology makes it possible to provide a 30-stage pump with less than 7 feet height featuring a short compact stack of impellers. An example of an industry benefiting from this pump design and technology are boiler feed applications in the power market. Traditionally, some of these applications are supplied by horizontal pumps. Verticals can be an improved solution in this type of scenario. Challenging Field Environments Sometimes installations are in environments with extreme temperatures. A vertical pump can go below ground, away from the elements, avoiding exposure of equipment and liquids to extreme, frigid temperatures at ground level that can wreak havoc on a traditional horizontal pump. Being below ground at more stable temperatures can often eliminate the need to make additional accommodations to equipment to enable the pump to function properly. Some of the latest vertical technologies feature radially split, double-walled pressure casings with metal-to-metal fits and controlled compression gaskets. This design functionality is ideal for light hydrocarbon applications. Finally, some regions or markets have limitations due to regulations. A vertical pump can feature reduced can length and low specific speed Ns resulting in minimal excavation to meet uploading and storage of light hydrocarbons in a confined space.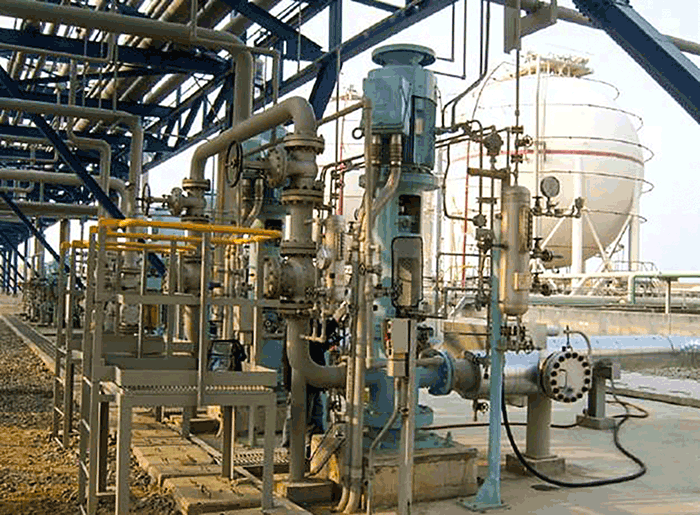