Past Pump System Improvement columns have focused on piping systems made of one or two circuits. These systems often are found in process systems where fluid is pumped from a supply tank acting as the inlet boundary, through the system’s process elements to make the product, and then through the control elements to adjust the system’s flow rate to maintain the desired operating condition. This month’s column examines multi-loop closed systems used to recirculate a heat transfer fluid to heat or cool loads in the system. These systems often are used in commercial buildings for heating, ventilation and air-conditioning (HVAC) chilled water cooling or hydronic heating, closed-loop cooling systems to keep operating equipment cool, and hot oil systems to provide process heating. Figure 1 shows a closed-loop cooling system consisting of four circuits. As always, this system is made of three elements working together. The pump elements (Pump P-1 and Pump P-2) provide all the hydraulic energy to the system. The process elements consist of a tank providing a point of known pressure, the interconnecting pipelines and the air handlers used to remove heat from the conditioned system. The control elements consist of control valves CV1 through CV4, which regulate the flow rate through each circuit to the specified value.

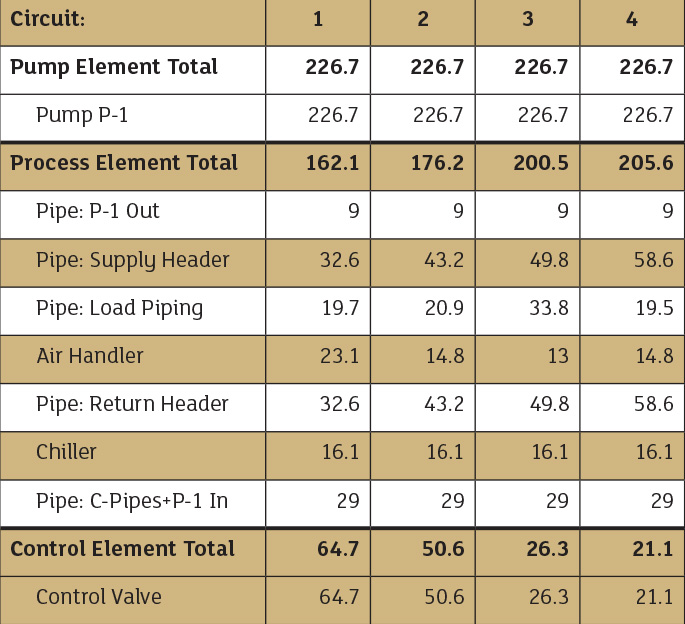