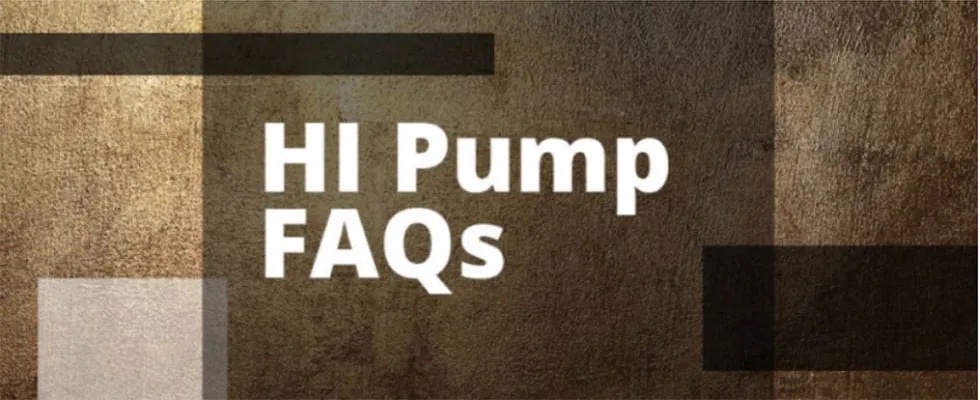
Series pumping is when the outlet of one pump supplies the inlet of another pump. This is much like the concept of multistage pumps, where within a single pump the outlet of one impeller supplies the inlet of the next. In series pumping, each pump will operate at the same flow rate unless some flow is directed elsewhere prior to the next pump. It is important to size series pumps to have nearly identical best efficiency point flow rates. Additionally, it is important to consider that each subsequent pump (if at the same location) will have higher inlet pressure, so the subsequent pumps may need to be designed to operate at a higher working pressure. Image 1 shows that operating three identical pumps in series triples the total head at a constant flow rate.
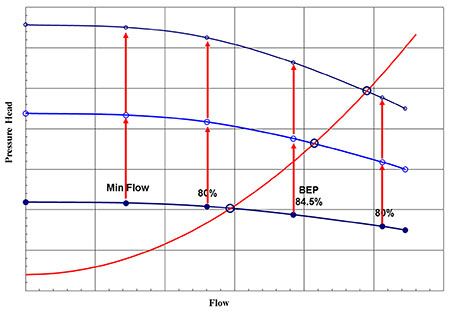
The two main reasons for series pumps are booster pumping to increase the inlet pressure of a second pump or when there are system high head requirements that cannot be accommodated by a single pump.
Some applications require an initial booster pump designed with lower net positive suction head requirements (NPSHr), which then boosts the pressure to a second pump. A common application for this occurs in the electric power plant steam cycle, where high energy pumps may be used that require high NPSH margin for reliable operation.
Some applications have high system head requirements along with high volumetric flow rates. An example of this is oil and gas pipeline applications that pump large volumes over thousands of miles. It is common to have four double suction between bearing pumps that operate in series to overcome the high friction head loss in the long pipe line. The first pump may be designed to operate at a lower speed (with lower NPSHr), which also acts as a booster pump for the subsequent pumps that operate at higher rotational speeds.