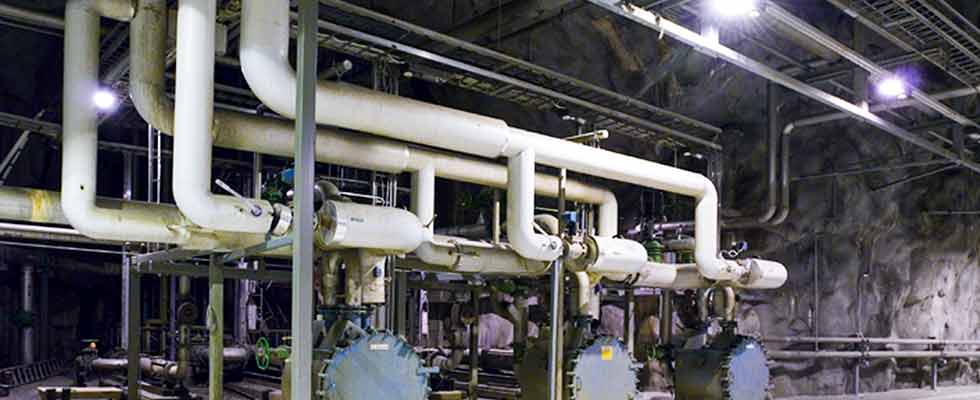
Variable frequency drives (VFDs) are commonly seen in industrial facilities, commercial buildings and water/wastewater (W/WW) facilities. For W/WW applications, VFDs can provide the ability to control the speed of the process pumps or blowers allowing facilities an improvement in controlling their processes to the actual demand of their incoming flow.
Process to Drive Plant Efficiency
By controlling the facilities process to the actual operating demand, VFDs can increase the overall efficiency of the entire facility. When facilities operate without VFDs, pumps and blowers are often run at full speed regardless of whether or not full speed is required. In this case, if the process demands are lower, mechanical devices such as valves are used to limit or bypass excessive pressures or flows.
This is effective, but it can be an inefficient method of controlling to setpoint. With the use of VFDs, operators are able enter a setpoint into the facilities’ supervisory control and data acquisition (SCADA). Based on process feedback, the VFDs will operate application pumps and blowers at actual required speeds to maintain the SCADA setpoint, regardless of how the facility’s incoming flow changes throughout the day. This method optimizes the overall facility process allowing for the most efficient operation.
In addition, operating pumps or blowers at reduced speeds based on feedback from process sensors can reduce or even eliminate the destructive forces on mechanical equipment caused by water hammer, restricting flows and pressures, cavitation, etc. This can increase the efficiency of oxygen transfer and reduce chemical usage and foaming issues.
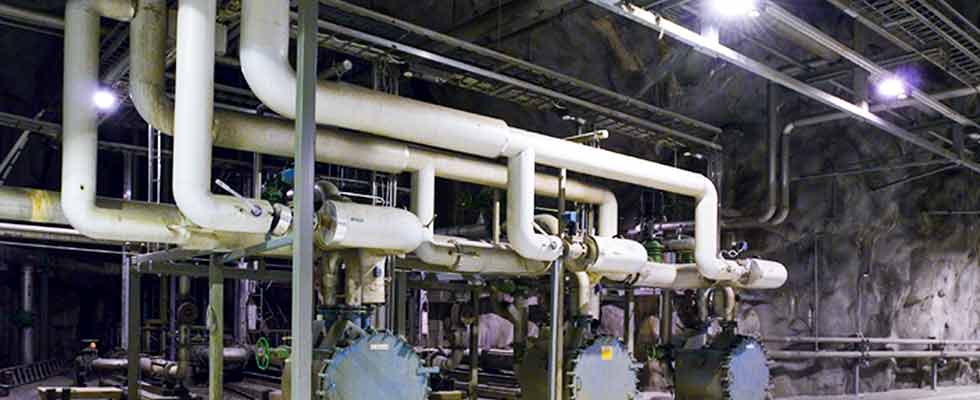
Providing Facility Resiliency
VFDs are also capable of providing resiliency to facilities. VFDs have become smart since they were introduced and some of the system control, typically provided by programmable logic controllers (PLCs) or SCADA in the past, can now be accomplished in the VFD.
Or, if desired, the PLC or SCADA can continue to operate as a primary control, and the VFD can provide the backup if the primary is lost.
Today’s VFDs are smart enough to switch between the systems.
Aiding Aging Infrastructure
VFDs can also help alleviate the stress of aging infrastructure. Facilities can get more life out of mechanical equipment by no longer having to run everything at full load. Operating the facility at process demand by using VFDs can reduce reliance on inefficient and maintenance demanding throttling valves or other mechanical pressure controls. Running process equipment at the required speed can result in longer pump, seal and bearing life.
In addition, because VFDs can provide a smooth ramp during starting and stopping, they open and close check valves smoothly, eliminating slamming and vibration to piping.
Pipes will see constant pressure or flow reducing water hammer incidents that crack and damage pipe walls, welds, flanges, seals and heavy loading on elbows.
By not running everything at full load and reducing reliance on throttling valves or other mechanical pressure controls, users can get more life out of existing mechanical equipment.
Running the equipment at the required speed can also protect swinging check valves by opening and closing more smoothly so they do not slam and shake the pipes. Pipes will see constant pressure or flow reducing the water hammer incidents that crack and damage the walls of the pipes, welds or joints, and elbows through the path of the pipes.
Generator Sizing
When the existing generators in the facility initially look as though they might be undersized for a future expansion because of low harmonic drives, that generator may need to be replaced or upgraded. Purchasing a new generator may not be required due to the low harmonics that are generated on the line side of a low harmonic drive. In addition, using low harmonics VFDs allows for closer actual sizing of utility transformers, circuit breakers and power cables, and no longer affects the efficiencies of across-the-line direct connected motors.
With today’s low harmonic drive technology, users no longer experience stability problems or require generator oversizing. Traditional drive technology may require extensive filtering to accommodate power problems created by legacy technology. Newer VFD technology can be more generator-friendly and may not require new generators or infrastructure installations.
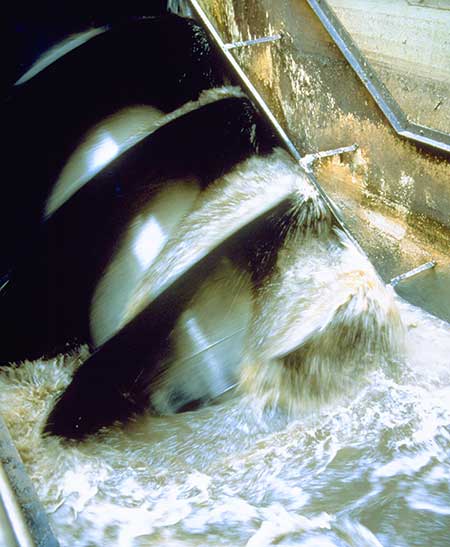
Condition Monitoring
Most modern VFDs offer the ability to monitor the motor and its load. The VFD is in constant control of the speed and current of the motor.
Given this data and the data entered at startup, the VFD can provide overload and overheating protection and can export this information and other operating data to a condition monitoring system. Using a simple Ethernet connection, VFDs can provide important data on the motor and the load conditions.
This data can be used to develop a predictive and preventative maintenance program, supported by a VFD life analysis. As a result, manufacturers can offer a lifetime analysis tool that, based on experience with the VFDs in the facility and the actual hours of operation, can provide preventative maintenance plans for all drives from that manufacturer. This plan can extend equipment life, reduce downtime and save labor costs from emergency repairs or replacements.
Benefits of VFDs
By combining the VFD with these or other feedback type sensors, like a pressure transmitter instead of a pressure switch to control pressure in the system, the VFD can maintain constant pressure.
Constant pressure will help aging infrastructure and reduce energy consumption. Fluctuation can reduce nonrevenue water losses as the higher pressure causes more water to flow out of the pipes by supplying constant pressure instead of on/off pressure.
VFD features that impact operations can also help extend the life of aging infrastructure. The VFD itself has pump features to help facilities operate more efficiently and with less cost and/or labor.
These features include pump clean, which is designed to remove strings, rags, wipes or other debris from a pump impeller simply by cycling the impeller directions to dislodge the debris.
VFD ramping brings the pump up to speed gradually to prevent water hammer and hydraulic surges from damaging the infrastructure and reduce electrical surges that cause overheating on power cables. Then on the slow down, it gradually reduces the flow to gently seat the check valve and ramp down the motor/pump.
Enclosure protection can offer protection to the VFD itself using a UL TYPE 12 enclosure offering protection against dust, dirt and debris flying around inside the facility and keeps it out of the VFD, thus helping to increase the life of the VFD. In addition, protecting the printed circuit boards of the VFD will help it withstand corrosion and other gases that are frequently part of the municipal process. A conformal coating process will help seal the printed circuit boards (PCBs) from the corrosive gases and help to extend the life of these critical components.
Facility safety in operations is key to facility management, and VFDs can help make facilities safer. When starting up a motor connected to another piece of equipment, the VFD may not be in the same room as the equipment itself. Using the Bluetooth keypad allows the technician to either be in the room with the equipment or, if it is in a hazardous location in a safe room, starting and stopping the motor or piece of equipment.
The VFD will monitor the motor/pump and trip when a potentially dangerous condition occurs, like a ground fault, thus protecting employees, equipment and the facility.
Supporting redundancy is a critical element to municipal operation. If the SCADA or PLC signal is lost, most smart VFDs now recognize the loss of signal and revert to a backup operational program that might use a level transmitter, float switches, a flow meter, dissolved oxygen (DO) meter or other sensor that offers a 4-20mA signal so the VFD can use a setpoint for operation.
Benefits of Standardization
And finally, if users can standardize on a single VFD manufacturer or product, this can benefit users in a couple of different but critical-to-operation ways.
Most VFDs built today are rated for constant torque and variable torque, which means that one series of VFDs can typically operate every application in the facility.
Secondly, in training, benefits arise if the staff can learn to operate the VFDs and know how to navigate the data available in the keypad.
This can save time and may allow them to predict or analyze a situation that has arisen. It will also help in troubleshooting, since typically a manufacturer builds VFDs in similar ways and uses the same keypad for an entire product series, which makes troubleshooting much easier in comparison to other VFDs or knowing and understanding what the readout should be.