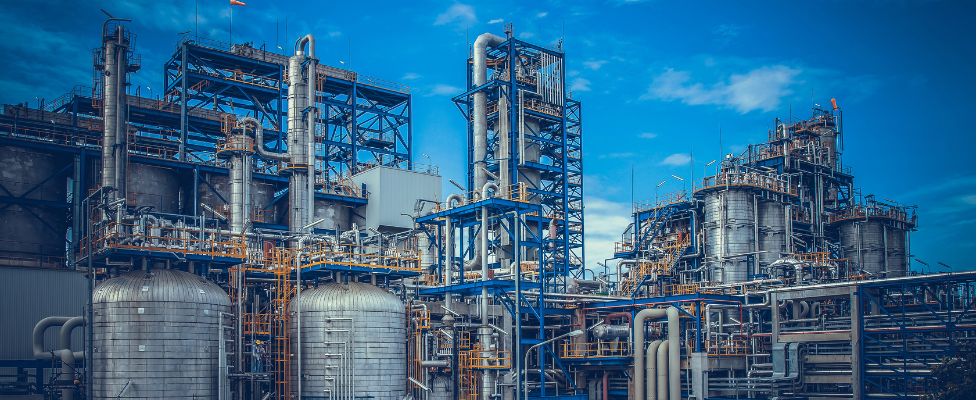
The oil and gas industry continues to be the backbone of the global energy supply chain, powering economies and fueling innovation. Fossil fuels account for nearly 80% of the world’s energy use, according to the Energy Institute. Countries like India (89.2%), Russia (87.5%), China (81.5%) and the United States (80.5%) are leading consumers of these traditional energy sources.
Pumps play a pivotal role in this industry, ensuring the smooth transport of natural gas, oil and other liquids across various stages of production. Oil and gas applications, however, provide multiple challenges for pumps. The products that pass through these pumps range from natural gas and petroleum to crude oil and even biofuels.
These raw materials present pumps with a multitude of difficulties, such as the range of viscosities between crude oil and natural gas vapors, for example. Some oil and gas liquids contain solids and particulates, creating additional processing challenges.
Other times, there is not sufficient product passing through the pump, creating a dry run environment that can cause catastrophic damage over time.
Another challenge is keeping the valuable oil and gas liquids contained within the pump. Some pump technologies, especially those not well suited for a wider viscosity range, are prone to leaks. This may lead to potential safety risks, negative impacts on the environment and ultimately a loss of product.
This article dives into the role of magnetically driven sliding vane (mag drive) pumps, exploring their unique capabilities and how they function in demanding environments.
Centrifugal Pumps & Gear Pumps
Operators in the oil and gas industry have no shortage of pump options. The range of applicable pumps means operators must consider the benefits and drawbacks of each pump before making their final decision.
The most common pump found in oil and gas operation is the centrifugal pump. These pumps use impellers with a radial outlet to transfer rotational mechanical energy to the liquid by increasing its kinetic energy, which is then used to transport the liquid to the discharge port. Centrifugal pumps excel at transferring low-viscosity fluids at high flow rates.
Despite their popularity, centrifugal pumps can struggle in oil and gas applications. While some models offer a sealless and leak-free option, they can struggle with solids, abrasive media and vapor mixtures. They also may not be equipped for dry run operation and can lose efficiency when conditions change.
Centrifugal pumps operate most effectively at their best efficiency point (BEP), but their operating performance may suffer when they deviate. This is especially true when centrifugal pumps fall out of their BEP when dealing with fluctuations in viscosity, pressure and flow rate.
Gear pumps are another common choice for oil and gas operations. This technology uses meshing gears to move liquids. Liquid enters the suction port within the teeth between a rotor gear and idler gear, creating an atmospheric vacuum that pulls the liquid into and through the pump. Two variations of this pump—internal and external—effectively process high-viscosity liquids. Similar to centrifugal pumps, some gear pump models may provide sealless, leak-free operation, but they are generally not well suited for dry run operation or vapor mixtures. The wear parts on this pump can also affect their longevity and effectiveness as time goes by. The gears in gear pumps can wear down over time, impacting flow rate performance.
Magnetically Driven Sliding Vane Pumps
Magnetically driven sliding vane pumps are another option for use in the oil and gas industry. Sliding vane pumps feature self-adjusting vanes that ensure the pump functions at its optimal efficiency throughout its lifetime. These pumps use a rotor with sliding vanes that draw the liquid in behind each vane, through the inlet port and into the pumping chamber. As the rotor turns, the liquid is transferred between the vanes to the outlet, where it is discharged as the pumping chamber is squeezed down. Each vane provides a positive mechanical push to the liquid before it.
Mag drive sliding vane pump technology does not contain dynamic seals, providing a leak-free pumping solution capable of handling pumping conditions that feature varying system pressure, near-zero net positive suction head available (NPSHa), liquid/vapor mix and suspended solids.
The composition of some mag drive vane pumps allows them to provide indefinite dry-run capability. To achieve this benefit, operators should consider a variation that includes a nonmagnetic containment shell, a noncantilevered rotor design, self-lubricating vanes and sleeve bearings, optimized porting and clearances and a lower running speed to create less frictional heat during a dry run event. When these operational features are in place, this type of sliding vane pump can run dry continuously with minimal risk of damage or failure.
While there is some skepticism about a pump’s ability to run dry for longer stretches, mag drive sliding vane pumps with composite containment shells do not suffer the same drawbacks as some other pump technologies. Those pumps that falter from longer dry run cycles tend to have bushings made from sensitive ceramics, temporary coatings or soft composites, all of which can suffer under extended dry run times.
Mag drive sliding vane pumps can also handle contaminants, with the ability to process liquids with suspended solids levels of up to 20%. These pumps also function as a near-zero net positive suction head required (NPSHr) solution, making them a fit for challenging pump inlet conditions. They can sustain optimal performance standards with liquids containing up to 20% vapor or air.
Viscosity fluctuations also do not impact these pumps the way they sometimes do with other pump technologies. When mag drive sliding vane pumps include the characteristics that allow for extended dry run times, they can also handle a wide viscosity range from 1 centipoise (cP) to 4,250 cP, which is ideal for oil and gas applications. Their performance will not degrade if the liquid’s viscosity drops below 1 cP or rises above 1 cP. Other technologies can handle varying viscosities, but not as wide of a range as the oil and gas industry encounters. Sliding vane magnetic drive pumps do well in oil and gas applications because they are viscosity flexible.
Pumps will always play a pivotal role in the oil and gas industry when transporting raw materials from the wellhead to the city gate. As such, operators must select a pump that meets all their processing and transporting needs. While the options are plentiful, sliding vane magnetic drive pumps may be worth considering, as they provide an array of performance benefits without many of the common pitfalls.