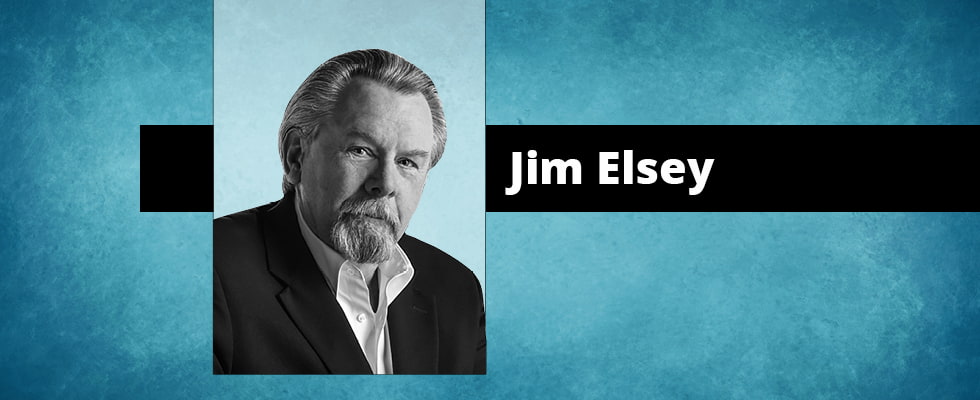
Editor’s Note: This is a continuation of Jim Elsey’s column from the November 2019 issue of Pumps & Systems titled “Wanted: Great Pump Salespeople.”
The myriad list of things that can go wrong with pumps in the field is long. In the confines of this column, I can list only a few examples. For today, we will assume all applications are centrifugal pumps.
Rather than explain one or two examples in detail, I thought it may be more interesting to provide a list of problem-based scenarios and the solution. These are all cases I have worked on in the last few years. Most examples will have more than one correct answer.
What’s Wrong with These Applications?
Problem: On a self-primer lift application the new pump is running erratically and performance is poor. This should be an easy application because the lift is only 10 feet on clean water.
Solution: In this frequent issue, the temperature of the water was ignored. The temperature of 160 F resulted in a (negative) vapor pressure of almost 11 feet, which when combined with the lift of 10 feet and the friction loss negated the positive contribution of the ambient pressure in the net positive suction head available (NPSHa) formula. The pump will cavitate, but it won’t lift the water.
Another common issue is an air leak in the suction line. People are surprised that ambient air can leak in without water leaking out. Wrap the suspected leak area with plastic and/or duct tape as a temporary measure to find and confirm the leak location.
Next on the list is submergence. With an insufficient height of liquid above the suction pipe entrance, air is introduced into the line. We assume the suction line, foot valve or strainer is not clogged in all of these cases.
Problem: A few miles away from the previous problem is yet another new self-primer pump application. The pump is attempting to pump treated water at ambient temperature from a wastewater treatment tank to a retention pond. The pump will not prime on a simple lift application of 5 feet.
Solution: The customer checked the 10 most common reasons for self-primers not to prime, but to no avail (see my article on this in the September 2016 issue). Turns out there is an 11th reason as a result of solving this issue. Self-primers are not well suited to pump water treated with surfactants. The surfactant caused the water to disassociate and foam in the priming chamber. The issue was solved by using a submersible pump.
Problem: The customer purchased a beautiful six-stage BB3 pump, driven by a foot-mounted condensing steam turbine. The pump is designed for continuous service on 450 F hydrocarbons. During the first six months of operation, the pump bearings have failed three times. The radial bearings are a fluid film type and the axial bearings are tilting pad thrust shoes. The customer is using a high-quality, mineral-based hydraulic oil in the bearings.
Solution: For this application, the customer should be using a turbine oil, not a hydraulic oil. Further, they should be using a synthetic based oil or a blend for this temperature range. The turbine oil will at a minimum contain rust and oxidation inhibitors, which the hydraulic oil does not.
Problem: The customer needs to increase throughput in the facility and added a third horizontal split case pump to the cooling water system. All three pumps are the same size, model and hydraulic rating (exact same size impellers). When the third pump was added, the overall flow rate only increased by a small percentage. The bearings subsequently developed issues due to excessive heat, so maintenance ran plant service water on the outside of the housings to keep them cool.
Solution: Bottom line issue in this case is that the pipe is too small to handle the flow rate. Pumps will operate where the system tells them to run. Adding the third pump just forced each pump to run back to the left on its operating curve and far away from the best efficiency point (BEP). In this operating range the pump dynamics place an increasing load on the bearings (see my March 2016 article for more details on the subject).
Running water on the outside of a hot bearing housing just makes the situation worse. The hot inner bearing is trying to expand due to the higher (hot) temperatures. The outer surfaces are contracting due to the lower temperatures offered by the cooling water. The difference puts the bearing in a mechanical bind and shortens the life.
Problem: A simple single-stage pump in a flooded suction application on ambient temperature water. The pump ran fine for several years, but now suddenly performs at about 65 to 70 percent of expected performance and the motor runs hot with increased vibrations.
Solution: An issue you will not frequently encounter, but these symptoms are classic for a motor that is single phasing. That is, one of the three phases has shorted out, and the motor is operating on two phases.
Problem: A customer starts up a new pump and within an hour the operator calls the supplier because the bearings are running hot and they need to shut down and perhaps replace the pump.
Solution: I am using this example to illustrate a common issue, in that the word “hot” is subjective, not objective. Operators will feel the bearing housing with their hand, which feels hot to them, but note for the average person items that are 120 F will feel really hot. It is not uncommon for a pump bearing housing to operate at temperatures in the 140 F to 170 F range. Use a thermometer or other device like a handheld infrared thermometer to measure temperature. There was nothing wrong with the pump in these cases.
Problem: A large single-stage horizontal split case pump is overhauled in your pump maintenance shop. When the pump is reinstalled, the performance is markedly off.
Solution: There can be a multitude of reasons why the performance is off, but the often overlooked reason on horizontal split case pumps is that the impeller can be installed backwards and so, even if the pump is running in the right direction, the impeller is not.
Problem: The suction pressure added to the discharge pressure far exceeds the flange ratings and pump limitations.
Solution: Customers will often review pump pressure ratings without consideration of the suction pressure, which must be added to the discharge pressure. This oversight can easily place a pump in a system that it is not rated for.
Problem: On a self-primer application, the suction line is more than 200 feet long from the sump to the pump. There are several high point inverted Us in the suction line.
Solution: The simple answer here is the pump should be as close to the sump (suction supply source) as possible. Proximity minimizes priming time (air removal process) and mechanical seal exposure to dry running. Further, the fluid in the priming chamber will overheat due to the long recirculation time and possibly flash to vapor.
The suction line geometry should be a continuous slope up to the pump to preclude air and noncondensable gases from trapping in the high spots.
Problem: On a heavy slurry application with a neutral pH, the pump casing is made from 304 stainless steel and the speed is 3,550 rpm.
Solution: The 304 stainless steel material is too soft for this application and will erode prematurely. Stainless is not required for corrosion protection since the pH is neutral. High chrome iron, which is a hard material, would be a better selection. Depending on the rheology and the size and shape of solids in the slurry, a rubber-lined pump may be a good candidate.
The speed of 3,550 rpm will be too high. Wear is proportional to the speed as a cube function (think of this as a factor of eight times). If a high head is required due to pipeline length, consider two or more larger and slower pumps spaced out over the system. If high head is required due to the pipe diameter, then the pipe is the wrong size, unless the diameter of the pipe is the required size to keep the velocity at a specific rate to preclude the slurry particles from dropping out of the liquid (critical carry velocity).
These are just some common examples of easily solvable field issues that a knowledgeable pump salesperson could help correct.
While resolving these issues, a good pump salesperson would also help the customer become a better pump owner in the process. Are you a good pump salesperson?
Read more Common Pumping Mistakes articles here.