Q. What does the term “balance” mean when referring to a mechanical seal? A. A balanced seal is a mechanical seal configuration in which the fluid closing forces on the seal faces have been modified through seal design. Seal balance, or balance ratio of a mechanical seal, is simply the ratio of two geometric areas. These areas are called the closing area (Ac) and the opening area (Ao). The closing area is different when pressure is on the outer diameter of the seal than when the pressure is on the inner diameter. When the pressure is on the outer diameter, the closing area is from the seal face outer diameter down to the lowest point, where the secondary seal rests against the shaft or sleeve. When the pressure is on the inner diameter, the closing area is from the highest point, where the secondary seal rests against the primary ring counter bore, down to the sleeve diameter.
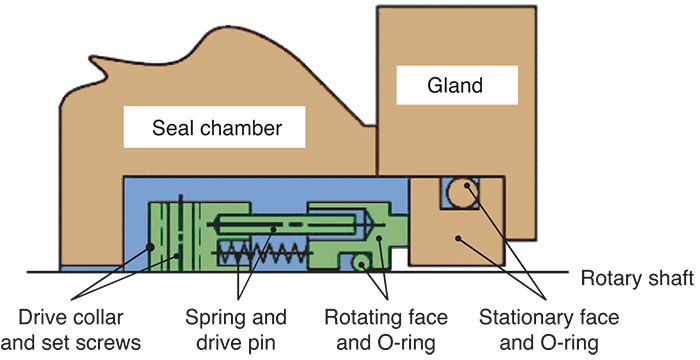
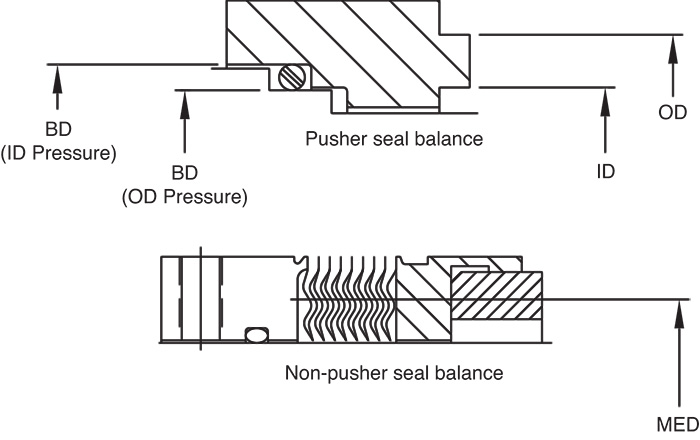
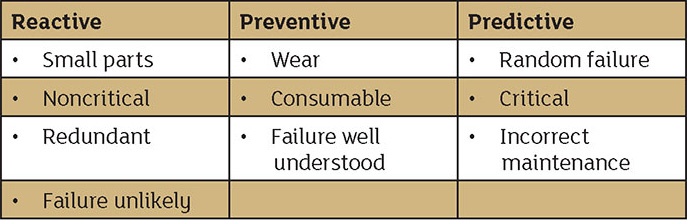
- all parts and labor costs
- all clean-up and decontamination costs
- all preventive maintenance activities (inspections, lubrications, etc.)
- all lost revenue from production downtime during maintenance (only if sold out)
- all rework costs associated repairs done incorrectly