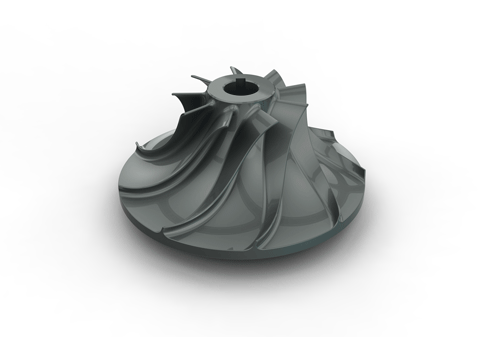
Many discussions surrounding pumps start with the impeller, be it a call with an application engineer assisting with pump selection, a specification document for a pump bid or perhaps this learning series. The impeller is the critical component that transfers power created by the motor into the movement of fluid.
While all impellers share the same task of moving fluid, they come in various shapes, sizes and materials to fit requirements of a specific application. It may seem overwhelming to differentiate between the numerous options, but an understanding of impeller basics will go a long way in making a proper pump selection.
Impeller Geometry
It is important to know the anatomy of a typical centrifugal impeller. The center of the impeller is referred to as the impeller’s eye. Moving out from the center are the impeller’s vanes. Impeller vanes are curved blades that catch and move fluid as the impeller rotates. The large circular component behind the vanes is the impeller’s hub. This hub provides support to the vanes while connecting all the vanes to the impeller assembly. The outer diameter of the hub is where one could find the impeller’s shroud. A semi-open impeller has a shroud that encloses the top of the impeller vanes. An enclosed design refers to an impeller that has a shroud covering both the top and bottom of the impeller vanes. Alternatively, an impeller may not have a shroud, and that type is referred to as an open impeller.
Impellers may vary in design, but some basic principles are constant across all impellers. The outer diameter of the vanes dictates the pressure generated by the pump. A small outer diameter will generate lower pressure than a similar impeller with a larger diameter. The height of the impeller vane dictates the flow generated by the pump. A shorter impeller vane will generate less flow than an impeller with taller vanes. These impeller geometric features provide context on why impeller styles are designed the way they are.
Impeller Physics
Impellers are the link between the power input (motor) and power output (fluid movement) of pumps. The pumping process starts as the motor rotates the impeller via the shaft. As the impeller turns, water is pushed from the center outward along the edge of vanes, which increases pressure. The high-pressure water is released from the ends of the vanes to the pump’s volute. Traveling the path of the volute, the water is discharged at the flow and pressure as dictated by the impeller’s geometry. Acceleration of water along the impeller vanes creates low pressure at the eye of the impeller. Atmospheric pressure, greater than the impeller eye’s low pressure, exerts force on the surface of the fluid being pumped and allows for a constant flow of fluid to the impeller eye.
Solids Handling
Many applications require pumping fluids with solids. This is often the case for submersible pumps where the pump
sits low in a reservoir designed to collect runoff and waste. One impeller style known for its solids handling capabilities is the channel impeller. Channel impellers allow for efficient solids passage between the impeller vanes. This impeller design is often used for sewage and wastewater applications.
Another common solids handling impeller is the vortex style, which is also known as a recessed impeller. This impeller sits recessed in the volute, creating a large open space between the impeller and suction port. Unlike other impellers that rely on the vanes pushing the water, this impeller creates a vortex in the open space of the volute. The vortex generated by rapid impeller rotation moves fluid and solids with minimal contact to the impeller. Lack of contact between the pumped fluid and impeller is beneficial in applications with abrasives or large solids.
Cutters & Choppers
For applications prone to clogging, there
are impeller styles designed to handle these troublesome solids. One such design is the cutter pump. The cutter pump’s impeller has a leading sharp edge often constructed in a hard material such as tungsten carbide. This sharp edge is designed with a tight clearance gap to a mating suction plate with its own sharp, serrated edges. As the impeller picks up solids, one portion of the solid is caught in the stationary serrated edge on the suction plate, allowing the rotating cutter impeller to cut the solid. Cutter pumps reduce clogging by various solids and debris such as rags, “flushable” wipes and even clothing to reduce pump downtime. These cut solids can then be filtered downstream of the pump.
Another impeller design for clog-prone applications is the chopper pump. A chopper pump is mechanically similar
to a cutter pump. Solids are torn between a sharp leading edge on the impeller and a sharp stationary edge on the suction inlet.
Unlike the cutter pump, which uses a serrated edge on the suction plate, a chopper pump has a chopper knife mechanism mounted externally toward the impeller’s eye. Tight tolerances are maintained between the chopper blade with the impeller eye, vanes and suction plate. These tight tolerances provide cutting across the entire vane, preventing clogging throughout the volute.
High-Pressure Applications
There are some applications that require higher pressure such as pumping to high elevations or in situations where system design requires small diameter pipe. To achieve this high pressure, the impeller’s design can be altered in a few ways. One way to increase pressure is to increase the outside diameter of the impeller.
Another method to increase pressure is to enclose the impeller vanes with a shroud both above and below. Enclosing the area between the impeller vanes reduces flow recirculation, which leads to a more efficient high-pressure output. While enclosed impellers are effective to increase pressure, they limit the solids-handling ability of the impeller.
High-pressure pumps often have a strainer to prevent the enclosed impeller from clogging. However, if large amounts
of solids are present, a grinder pump may be better suited for the application. Grinder pumps have a grinder blade on the outside of the suction port. As this sharp blade rotates, it minces solids into fine pieces that flow into the pump through a suction strainer plate. Finely ground solids are then moved through the pump, typically by a high head impeller. Grinder pumps are often found in municipal wastewater collection in areas with uneven terrain. These areas rely on small-diameter, high-pressure pipelines to transfer wastewater. Grinder pumps are critical to providing the high pressure required but also to cut solids down to reduce clogging the smaller piping.
Impeller Materials
Selecting the proper material of construction is just as critical as selecting the impeller style. The impeller may come in various materials, such as varied grades of cast iron, stainless steel, bronze and resin plastic. Cast irons offer good abrasion resistance at an economical cost. However, cast iron may not hold up to highly abrasive or corrosive fluids. To prevent premature impeller failure from corrosion, a stainless-steel impeller may be necessary. While stainless steel is more expensive than cast iron, it typically offers better protection against aggressive chemicals.
Bronze is another corrosion-resistant material that is often found near coastal applications. Bronze protects against salt water in applications near the sea or processes that use brine. Some smaller pumps may utilize a plastic impeller. These molded impellers offer excellent chemical resistance and high abrasion resistance and are cost effective compared to stainless steel or bronze alternatives.
The fluid being pumped, as well as the system’s conditions, will dictate the type of impeller needed. It is important to communicate this information to your pump provider to ensure proper impeller and pump selection.