This pump setup allows the ability to add or subtract flow capacity.
Grundfos
01/29/2019
Many of today’s pumps are installed to operate under variable flow conditions, so understanding the concept of parallel pump control is a must. First, it is critical to know how parallel pumps will operate upon installation. The idea behind parallel connected pumps is the ability to add or subtract flow capacity and/or provide redundancy. Image 1 shows three parallel connected pumps. For the purpose of this discussion, assume they are each of equal capacity. The pump head-capacity curves are shown in Image 2.
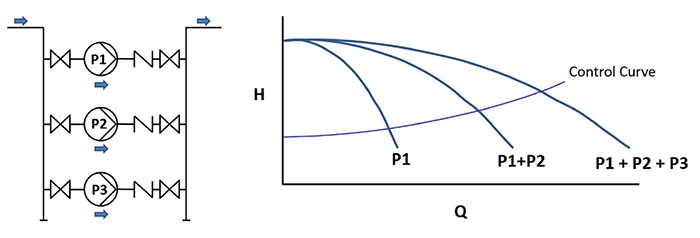
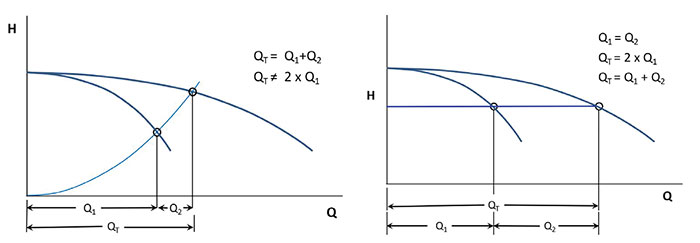
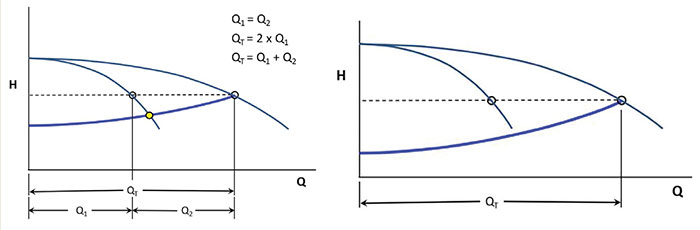
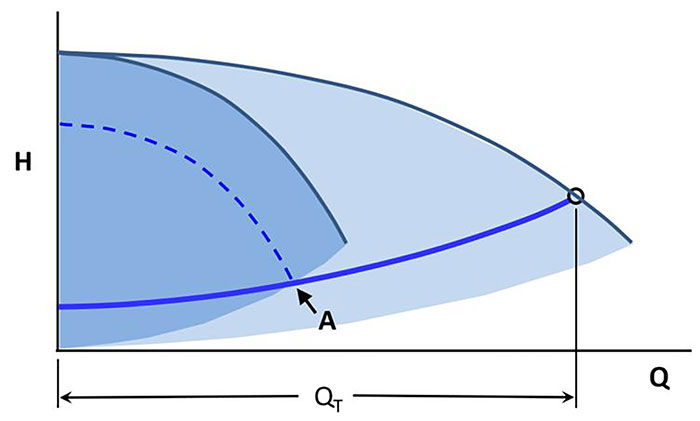